- Features Overview
- anyLogistix vs Excel
- Supply Chain Network Optimization
- Supply Chain Simulation
- Supply Chain Digital Twins
- Greenfield Analysis
- Supply Chain Risk Mitigation
- Safety Stock Estimation
- Supply Chain Network Design
- Inventory Optimization
- Supply Chain Risk Assessment
- Sourcing Optimization
- Cash to Serve
- Supply Chain Master Planning
- Bullwhip Effect Quantification
- Case Studies
- ALX Textbook
- White Papers
- Training and Events
- Documentation

Supply chain optimization explained—with example
November 15, 2021 Anastasiya Malinovskaya
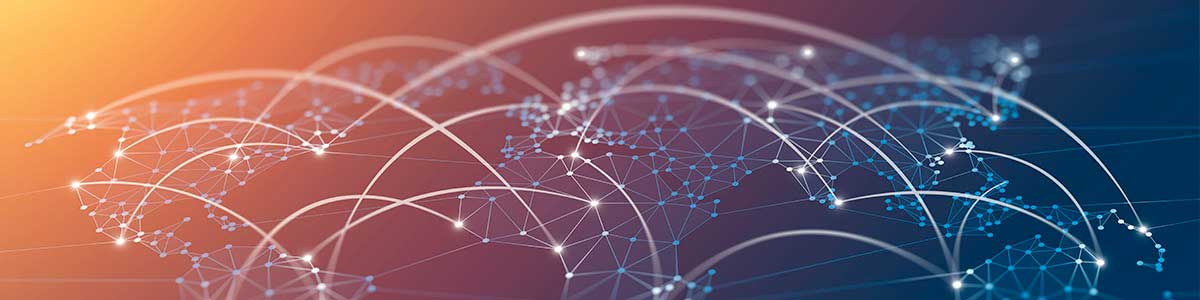
Creating and maintaining a result-oriented, efficient supply chain can be tricky since it brings together the procurement, production, transportation, sales, and financial sides of your business. This is where optimization can help.
In this article, we explore what ‘supply chain optimization‘ means, look at the typical supply chain management and optimization problems, and go through a practical example to learn how to solve those problems.
- What is supply chain optimization?
- Typical problems supply chain network optimization solves
- Example: Facility location problem and production planning
WHAT IS SUPPLY CHAIN OPTIMIZATION?
Many definitions of supply chain optimization exist but all generally fall into two categories:
- In the broad sense, the term refers to all kinds of processes that help improve supply chain performance and efficiency. It applies to managerial approaches, both quantitative and qualitative, that help make a supply chain more lean and agile, grow profit, and reduce costs.
- The narrower meaning of supply chain optimization focuses on a mathematical problem-solving method. Also called supply chain network optimization , this is a quantitative approach for finding the best combination of facilities, warehouses, the flows between them, production resource allocation, and other elements under specific constraints. Such optimization can solve large-scale data-intensive problems and uses mixed-integer and linear programming solvers (such as IBM ILOG CPLEX®).
In this article, we will focus on the narrower term, because it is the one that usually causes the most confusion, and we will show you how to perform supply chain network optimization .
Network optimization, as a quantitative approach, combined with management-based qualitative methods (case study research, action research, etc.) helps solve various supply chain challenges. Managers typically divide those challenges into three levels:
- Strategic issues include size and location of manufacturing plants or distribution centers, the structure of service networks, and supply chain design .
- Tactical issues include production , transportation, and inventory planning while balancing supply and demand.
- Operational issues address production scheduling and control, inventory control, and vehicle routing.
Optimization usually deals with the problems on the first two levels – strategic and tactical. Let us have a closer look at them.
TYPICAL PROBLEMS SOLVED WITH SUPPLY CHAIN NETWORK OPTIMIZATION
Supply chain design – Includes finding optimal locations for new facilities (distribution centers, warehouses, and plants), defining the flows between them, and balancing costs. An optimal supply chain design should be reliable, cost-efficient, and ready to deal with supply and demand uncertainty.
Master planning by period – Its goal is to align production, storage, and transport with demand fluctuations. When aligned, they help maximize a supply chain’s efficiency, cut costs, and increase profit.
Transportation – The objective is to transport products from one facility to another (from warehouses to customers, for example) while satisfying supply and demand and keeping the transportation costs at the lowest level.
Now let us see network optimization in action.
EXAMPLE: FACILITY LOCATION PROBLEM AND PRODUCTION PLANNING
From the supply chain network optimization example below, you will learn to:
- Find optimal locations for several distribution centers ( supply chain design problem ).
- Plan production and analyze demand fulfillment for the main and by-products ( master planning and production planning problems ).
Linear and mixed-integer programming are commonly used methods for solving supply chain optimization challenges. While many companies use MS Excel to implement these methods, we would like to show a more efficient and easier way to solve the same supply chain problems in anyLogistix software.
Sunflower Oil Supply Chain Model Description
A company acquires sunflower oil factories in several countries and wants to merge its supply chains. These are zero-waste factories that produce sunflower husk and pressed cake as by-products. The by-products are then further processed into fuel and animal food.
A supply chain network design for the model consists of Suppliers (which transfer raw materials to factories), Factories , Distribtion centers (DCs), Ports (used to transfer products by sea), and Customers . The screenshots below show this network’s structure and on-map view.
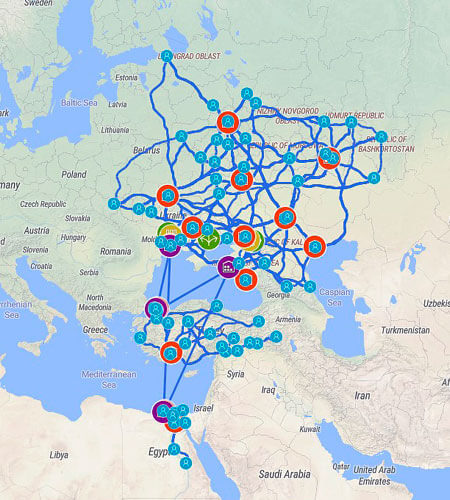
The supply chain’s on-map view (left) and its network’s structure (right) in anyLogistix supply chain optimization software (click to enlarge)
Main Characteristics of the Supply Chain Model
Distribution Centers, Factories, and Ports
- In total there are 14 potential DCs but we set a constraint that the optimizatior must only select up to 7.
- The maximum stock level and storage expenses differ for DCs, factories, and ports.
- Factories also have maximum monthly throughput of refined and unrefined sunflower oil – 4,000 and 2,000 tons respectively.
- Selling price and production cost differ for each product.
- Tariffs (customs duties) are considered. They are calculated when importing or exporting a certain number of products.
- By-products don’t have their own bills of materials (BOM) defined. But their production is set as a ratio of the main products and the by-products.
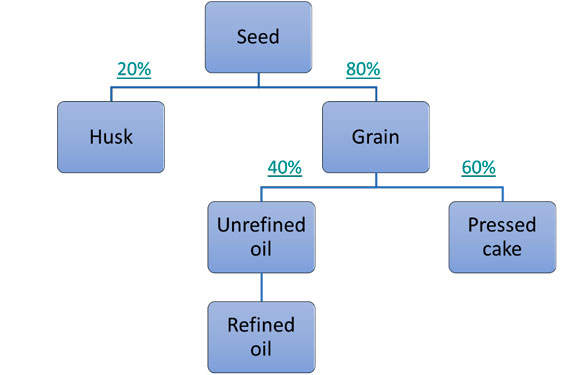
Production of the main and the by-products in the supply chain optimization model
We have a demand forecast for the next three years . The demand
- Is constant during the first year for all products;
- Increases for oil by 30% in August and September during the second and the third years;
- Decreases for pressed cake by 30% from April to October during the third year.
Demand also varies for each product. If demand fails to get fulfilled, penalties (or SLA violation fees) per product unit are charged.
- anyLogistix software uses online GIS map providers to identify real roads between supply chain facilities.
- Transportation costs are calculated according to distance travelled and transportation load .
- We use two vehicle types : trucks and container ships.
- Each vehicle type has certain capacity and speed values .
Why Do You Need Optimization in This Case?
The dilemma lies in the balance between demand and production for both the main products and by-products.
If we try to completely fulfill demand for the main products, we end up with too many by-products than required to meet demand and must therefore find storage for them, at a cost.
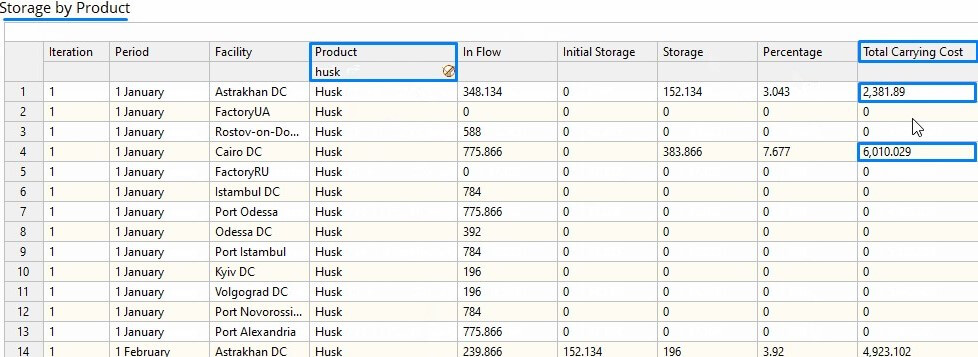
After running the scenario, we see that the demand for oil is completely fulfilled, however, inventory carrying costs for husk are charged
Alternatively, the company can choose to reduce the production volume . In this case, factories only produce a certain amount to avoid expenses for storing unsold main products. Average demand is fulfilled this way but demand peaks are not. Eventually, the company will have to pay SLA penalties.
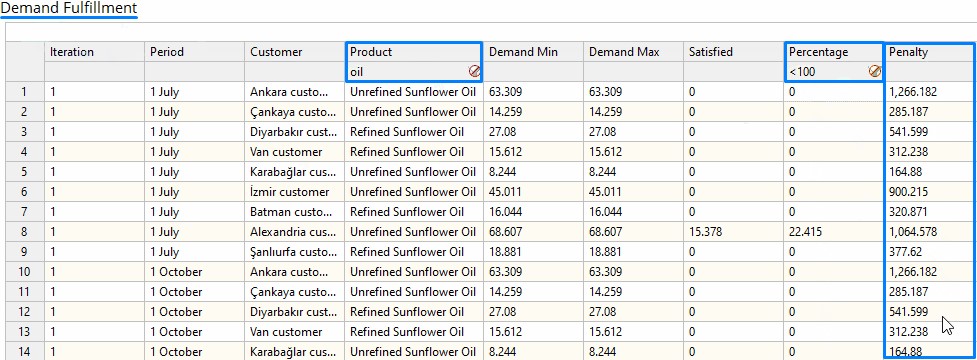
After running the scenario, we see that while the average demand for oil is satisfied, the company fails to do that during demand fluctuations. As a result, SLA penalties are charged
Network optimization aims at finding the best configuration alternatives for our sunflower oil supply chain. While striving to reach the optimal balance between demand and production , it also considers our costs, penalties, and other constraints. For example, it takes into account the total amount of DCs that we can include in our network and the maximum throughput of the factories.
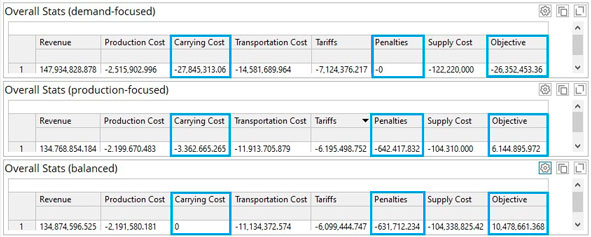
Statistics for the three supply chain optimization scenarios described earlier. Compare (Inventory) Carrying costs, Penalties, and Objectives (profit in US dollars)
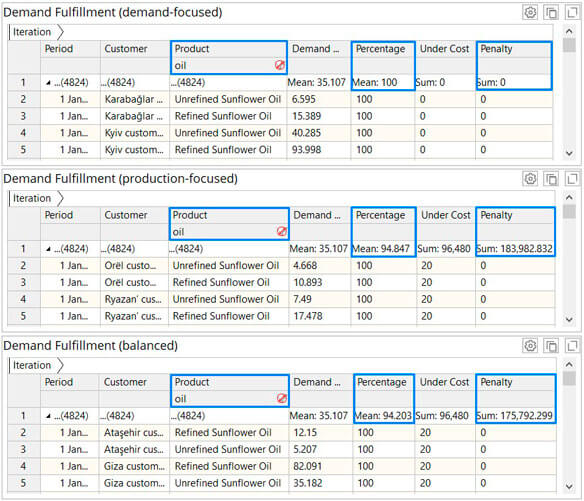
Statistics for the three supply chain optimization scenarios described earlier. Compare Demand fulfillment (in %) and Penalties
Supply Chain Optimization Results
Running the network optimization experiment for the sunflower oil supply chain model in anyLogistix, provides several network configurations with detailed statistics.
For example, the statistics show that during the first modeled year, the demand for sunflower oil was completely satisfied, while for the by-products, it was only partially satisfied. Therefore, no penalties are charged for oil, as you can see in the table below.
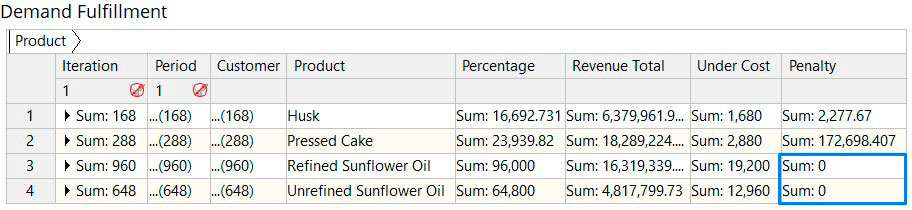
During the first modeled year, the demand for sunflower oil was completely satisfied, while for the by-products, it was only partially satisfied
Producing additional batches to completely satisfy demand for the by-products would have created an excess of the main product. This, in turn, would result in extra storage costs and decrease supply chain operation profits.
The result of this supply chain optimization example is a three-year production plan that was calculated considering all constraints. This optimization example can be adapted and applied to your real supply chain tasks.
Together we have explored what supply chain optimization means and the problems it solves. Now what?
To start, download the the sunflower oil example and import it in anyLogistix Studio Edition (File → Import → Import Scenario from File or follow the guide ). Then explore the network structure, and examine the tables to see all the settings and parameters for the supply chain. Finally, you can run the optimization experiment in anyLogistix and analyze the results yourself.
If you don’t have anyLogistix Studio, we recommend you watch these short videos on related supply chain optimization topics and try the corresponding examples yourself in anyLogistix PLE for free .
Supply chain master planning
Learn how to organize a two-tier network and estimate the amount of product a cheese plant should produce each month.
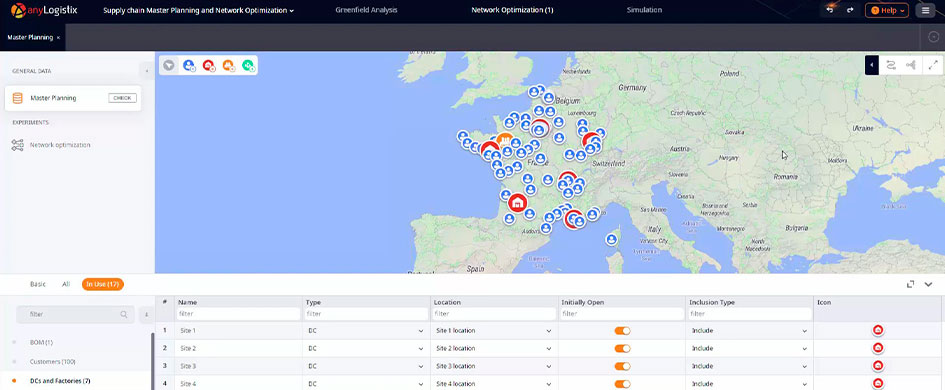
See the example’s description in anyLogistix Documentation
Global network optimization
Discover how to organize a multi-tier network. The goal of this example is to find the best configuration of DCs while considering transportation, initial, carrying costs, and the list of locations where a company could build warehouses.
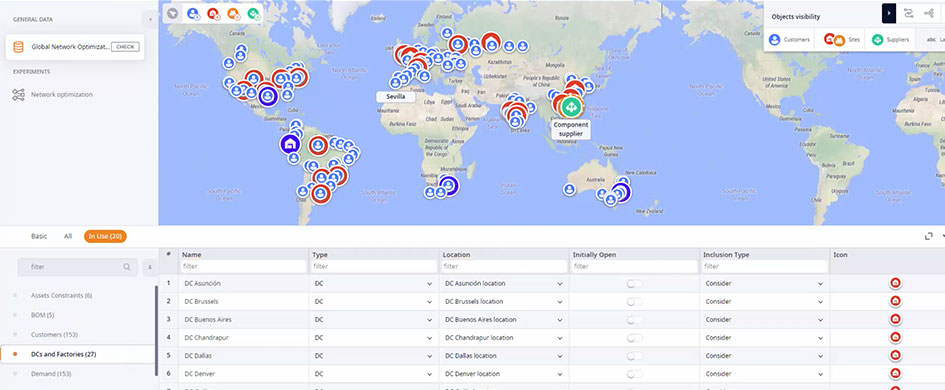
try anyLogistix for free
- academic [3]
- anyLogistix PLE [1]
- case studies [9]
- events [16]
- features [8]
- feedback [1]
- greenfield analysis [9]
- network optimization [26]
- new version [19]
- simulation [30]
- supply chain analytics [5]
- telecoms [1]
- transportation optimization [7]
- white paper [8]
How to Conduct a Problem-Solving Session with Supply Chain?
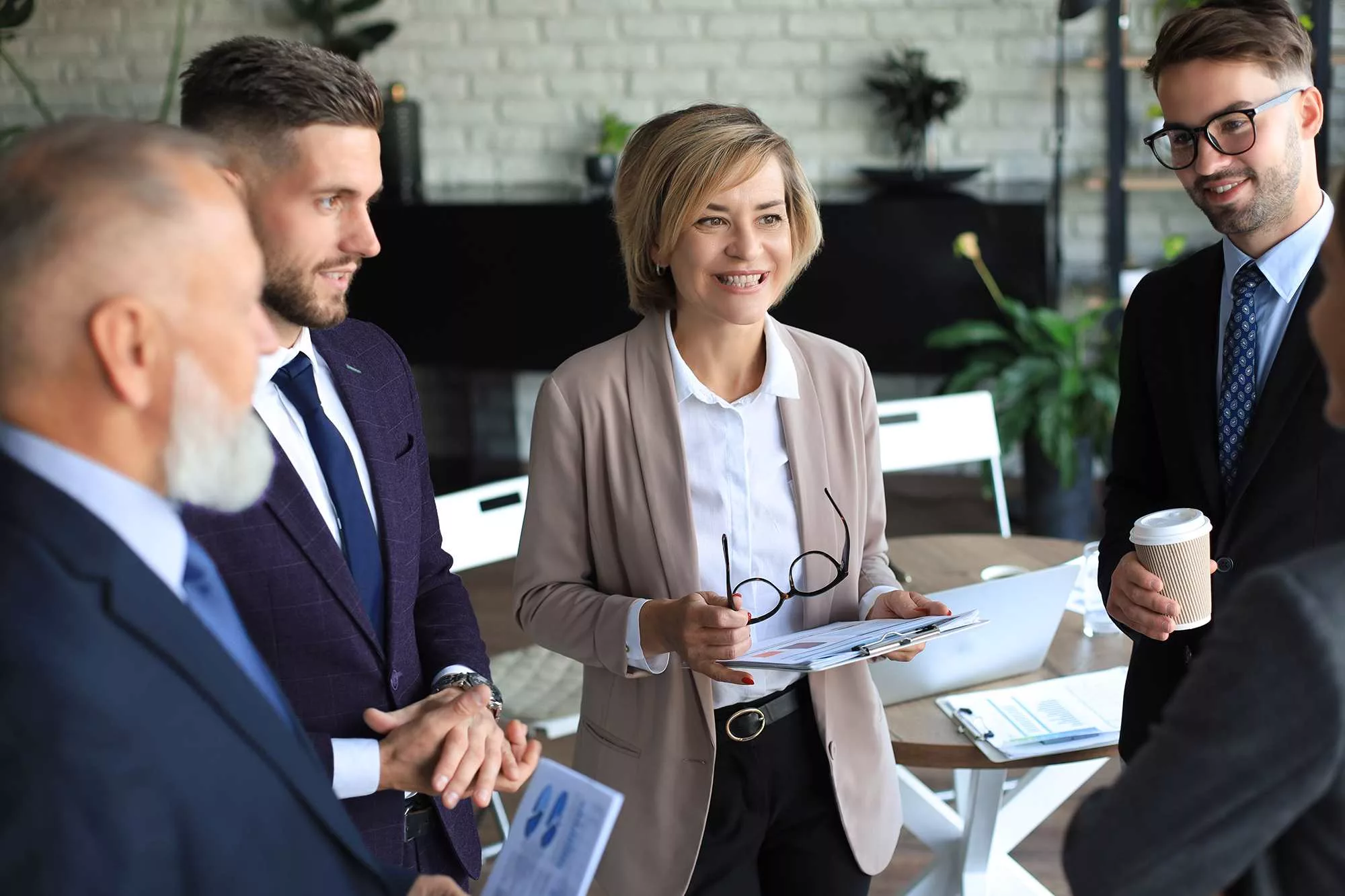
In today’s complex business landscape, the ability to solve problems efficiently and effectively is crucial for supply chain management. Whether it’s addressing bottlenecks in the production line or finding solutions to logistics challenges, problem-solving sessions play a vital role in optimizing supply chain operations. This article will guide you through the process of conducting a problem-solving session, from understanding its importance to overcoming common challenges.
Understanding the Importance of Problem-Solving in Supply Chain
Problem-solving is not just about finding quick fixes; it is about identifying root causes and implementing sustainable solutions. In the context of supply chain management, problem-solving helps organizations improve efficiency, reduce costs, and enhance customer satisfaction. Effective problem-solving also fosters a culture of continuous improvement, enabling businesses to stay ahead of the competition.
When it comes to supply chain management, problem-solving plays a crucial role in ensuring smooth operations and overcoming challenges. It involves a systematic approach to identify and resolve issues that may arise at different stages of the supply chain process. By addressing these problems head-on, organizations can minimize disruptions, optimize performance, and achieve their strategic goals.
One of the key factors in successful problem-solving sessions is effective communication. It is essential to create an environment where all participants can openly discuss the issues at hand, share ideas, and collaborate on finding solutions. Clear communication ensures that everyone is on the same page and helps prevent misunderstandings or conflicts that could hinder problem-solving efforts.
During problem-solving sessions, it is important to encourage active participation from all stakeholders involved in the supply chain. This includes representatives from procurement, production, logistics, and customer service departments. By involving individuals with diverse expertise and perspectives, organizations can gain valuable insights and develop comprehensive solutions that address the root causes of problems.
Furthermore, problem-solving sessions should not be limited to addressing immediate issues. They should also focus on identifying potential risks and developing proactive strategies to prevent future problems. By taking a proactive approach, organizations can minimize the impact of disruptions and build resilience within their supply chains.
The impact of effective problem-solving on supply chain efficiency cannot be overstated. By identifying and addressing bottlenecks or inefficiencies, organizations can streamline processes, reduce lead times, and optimize resource allocation. This, in turn, leads to cost savings, improved productivity, and increased customer satisfaction.
For example, through effective problem-solving, organizations can identify areas where there is a lack of coordination between different departments or suppliers. By addressing these coordination issues, organizations can improve the overall flow of goods and information, resulting in faster order fulfillment and reduced lead times.
Moreover, problem-solving sessions enable organizations to identify opportunities for automation and technology integration. By leveraging technology solutions such as supply chain management software or predictive analytics, organizations can enhance visibility, track performance metrics, and make data-driven decisions. This not only improves efficiency but also enables organizations to adapt to changing market demands and customer expectations.
In conclusion, problem-solving is a critical aspect of supply chain management. It helps organizations overcome challenges, improve efficiency, and enhance customer satisfaction. By fostering a culture of continuous improvement and effective communication, organizations can stay ahead of the competition and achieve long-term success in today’s dynamic business environment.
Preparing for a Problem-Solving Session
Before conducting a problem-solving session, it is crucial to lay the groundwork for success. This involves identifying key participants and setting clear objectives.
Problem-solving sessions are an essential part of any organization’s continuous improvement efforts. They provide a platform for teams to come together and brainstorm innovative solutions to complex challenges. However, without proper preparation, these sessions can become unproductive and fail to yield the desired outcomes.
Identifying Key Participants
Identifying the right participants for the problem-solving session is essential. These individuals should have a deep understanding of the supply chain process under review and possess the necessary expertise to contribute effectively. Involving representatives from different departments or functions allows for a holistic and diverse perspective.
When selecting participants, it is important to consider their roles and responsibilities within the organization. Including individuals who are directly involved in the problem or have a stake in its resolution ensures that the session is well-informed and comprehensive. Additionally, incorporating cross-functional team members fosters collaboration and encourages the sharing of different viewpoints.
Moreover, it is beneficial to involve individuals who have experience in problem-solving methodologies or have a track record of successfully addressing similar challenges. Their expertise can guide the session and provide valuable insights to the team.
Setting Clear Objectives
Clearly defining the objectives of the problem-solving session is crucial to ensure focus and alignment among participants. The objectives should be specific, measurable, achievable, relevant, and time-bound (SMART). This clarity of purpose helps keep the session on track and ensures that solutions are tailored to address the identified challenges.
When setting objectives, it is important to consider the desired outcomes of the session. Are you looking to improve efficiency, reduce costs, enhance customer satisfaction, or address a specific bottleneck in the supply chain? Clearly articulating these objectives helps participants understand the purpose of the session and enables them to contribute more effectively.
Furthermore, setting SMART objectives allows for better evaluation of the session’s success. By defining specific metrics and timelines, you can measure the impact of the solutions generated during the session and track progress towards achieving the desired outcomes.
Additionally, it is beneficial to communicate the objectives to all participants before the session. This ensures that everyone is on the same page and can come prepared with relevant information and ideas. It also helps create a sense of ownership and accountability among the participants, fostering a more productive and engaging problem-solving session.
Conducting the Problem-Solving Session
When conducting the problem-solving session, it is important to create a conducive environment for open discussion and utilize problem-solving techniques effectively.
Problem-solving sessions are a crucial part of any organization’s decision-making process. They provide a platform for teams to come together, analyze complex issues, and find innovative solutions. However, conducting a successful problem-solving session requires more than just gathering people in a room. It requires careful planning, facilitation, and the use of effective problem-solving techniques.
Facilitating Open Discussion
The facilitator plays a crucial role in encouraging open and constructive discussion. They should create a safe space that allows participants to voice their opinions, share their perspectives, and challenge existing processes. This collaborative approach fosters engagement and creativity, leading to more effective problem-solving.
One way to facilitate open discussion is by establishing ground rules at the beginning of the session. These ground rules should emphasize respect, active listening, and the importance of considering diverse viewpoints. By setting clear expectations, the facilitator creates an environment where everyone feels comfortable expressing their thoughts and ideas.
In addition to ground rules, the facilitator can also use various techniques to encourage participation. For example, they can employ brainstorming exercises to generate a wide range of ideas or employ breakout sessions to allow smaller groups to delve deeper into specific aspects of the problem. By incorporating these techniques, the facilitator ensures that all participants have a chance to contribute and that no valuable insights are left unexplored.
Utilizing Problem-Solving Techniques
There are several problem-solving techniques that can be applied during the session, such as root cause analysis, fishbone diagrams, or the 5 Whys. These techniques help identify the underlying causes of the problem and generate potential solutions. Each technique has its strengths, so it is important to choose the most appropriate one based on the nature of the problem at hand.
Root cause analysis is a systematic approach that aims to identify the fundamental reason behind a problem. By asking “why” multiple times, the facilitator can uncover the underlying causes that may not be immediately apparent. This technique helps teams move beyond surface-level symptoms and address the root issues, leading to more effective and sustainable solutions.
Fishbone diagrams, also known as cause-and-effect diagrams, are visual tools that help teams identify the various factors contributing to a problem. By categorizing these factors into different branches, the facilitator can create a comprehensive overview of the problem’s causes. This technique encourages a holistic understanding of the issue and enables teams to explore potential solutions from multiple angles.
The 5 Whys technique is a simple yet powerful tool for uncovering the underlying causes of a problem. By repeatedly asking “why” five times, teams can peel back the layers and get to the core of the issue. This technique helps teams avoid jumping to conclusions and encourages a deeper analysis of the problem at hand.
While these problem-solving techniques are valuable, it is important to remember that they are not standalone solutions. The facilitator should adapt and combine these techniques as needed, depending on the complexity and nature of the problem. By using a flexible and tailored approach, the facilitator can guide the problem-solving session towards meaningful and actionable outcomes.
Post-Session Actions and Follow-ups
Conducting a problem-solving session is just the first step; it is equally important to analyze the outcomes and implement agreed-upon solutions.
Analyzing Session Outcomes
After the problem-solving session, it is essential to analyze the outcomes and identify patterns or recurring issues. This analysis helps validate the effectiveness of the solutions proposed and highlights areas that require further attention. It also provides valuable insights for future problem-solving sessions and continuous improvement initiatives.
Implementing Agreed Upon Solutions
Implementing the solutions agreed upon during the problem-solving session is crucial to achieving tangible results. This requires assigning responsibilities, establishing timelines, and monitoring progress. Clear communication and collaboration across different teams or departments are essential to ensure successful implementation and drive sustainable change.
Overcoming Common Challenges in Problem-Solving Sessions
Problem-solving sessions are not without challenges. However, by being aware of common obstacles, you can proactively address them and keep the problem-solving process on track.
Dealing with Resistance to Change
Resistance to change is a common challenge when implementing new solutions or processes. It is important to address concerns or objections from participants and emphasize the benefits of the proposed changes. Communicating the rationale behind the solutions and involving key stakeholders throughout the problem-solving process can help alleviate resistance and foster a sense of ownership.
Ensuring Continuous Improvement
Problem-solving sessions should not be seen as a one-time fix but as part of an ongoing journey towards continuous improvement. It is crucial to cultivate a culture that values feedback, encourages innovation, and embraces change. By continuously evaluating and refining processes, organizations can adapt to evolving market demands and maintain a competitive edge.
In conclusion, conducting a problem-solving session is a vital component of effective supply chain management. By understanding the importance of problem-solving, preparing for the session, leveraging effective communication and problem-solving techniques, and implementing agreed-upon solutions, organizations can drive efficiency, streamline operations, and achieve sustainable improvements. Despite the challenges that may arise, a proactive approach and a commitment to continuous improvement will pave the way for success.
CIPD Level 3 HR and L&D qualification : The CIPD Level 3 Certificate in people practice is ideal for anyone looking to start a career in either HR or Learning and Development. CIPD Level 5 HR qualification : The CIPD Level 5 Associate Diploma in People Management will help you build on your existing HR knowledge. CIPD Level 5 L&D qualification : The CIPD Level 5 Diploma in Organisational Learning and Development is the most comprehensive course available for L&D professionals, ideal for you if you want to formalise your existing experience, skills and knowledge. CIPD Level 7 HR qualification : The CIPD Level 7 Advanced Diploma is aimed at expanding learners’ autonomy so they can strategically direct organisations and their people.
If you aspire to become a digital marketing manager or explore the senior level of your career, have a look at the squared digital marketing programme .
Related Articles
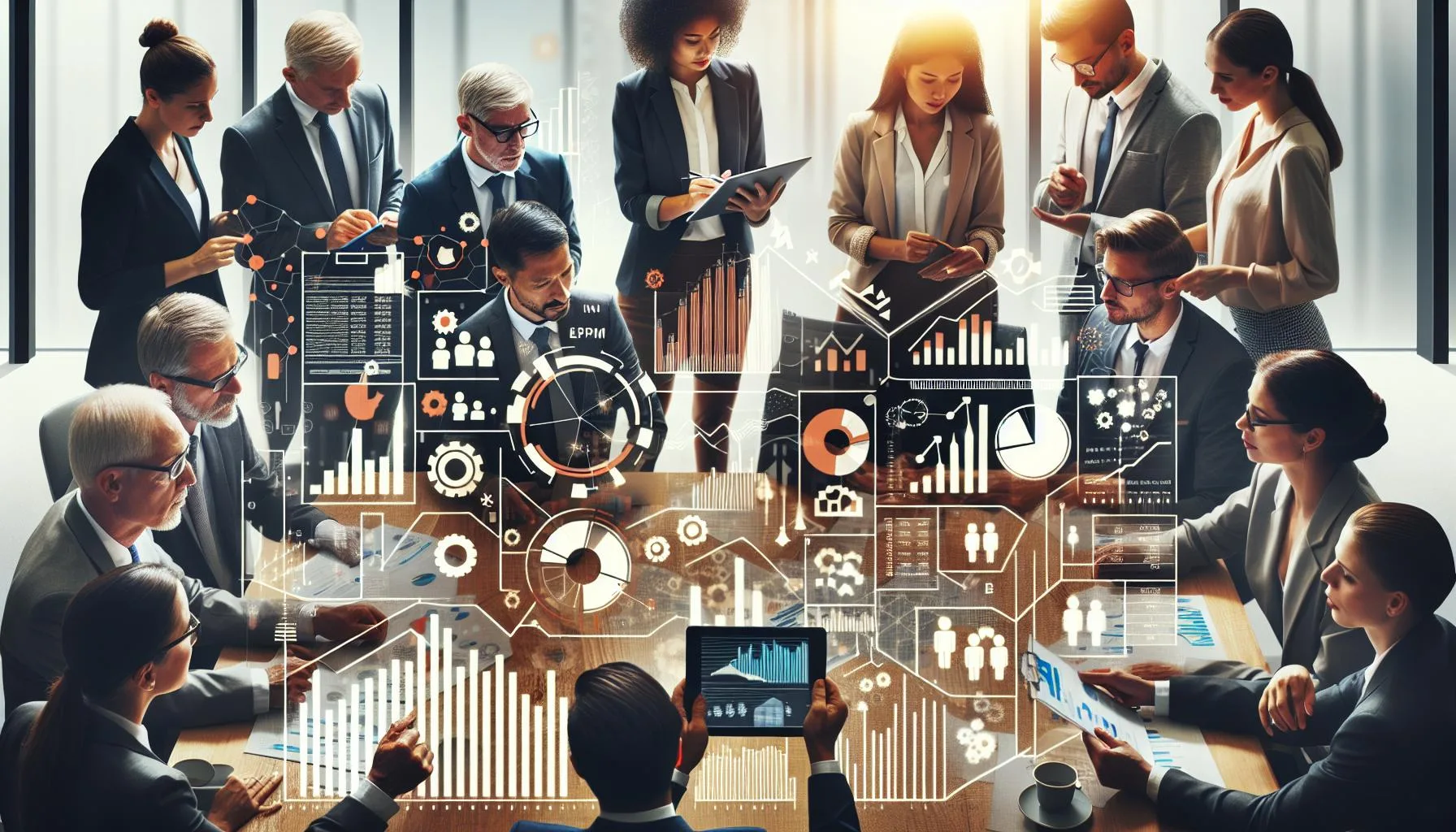
In today’s fast-paced world, we understand that financial well-being is a crucial aspect of overall employee satisfaction and productivity. It’s not just about earning a paycheck; it’s about feeling secure and having peace of mind when it comes to financial matters. That’s why we’re diving deep into the steps necessary to ensure employees’ financial well-being, […]
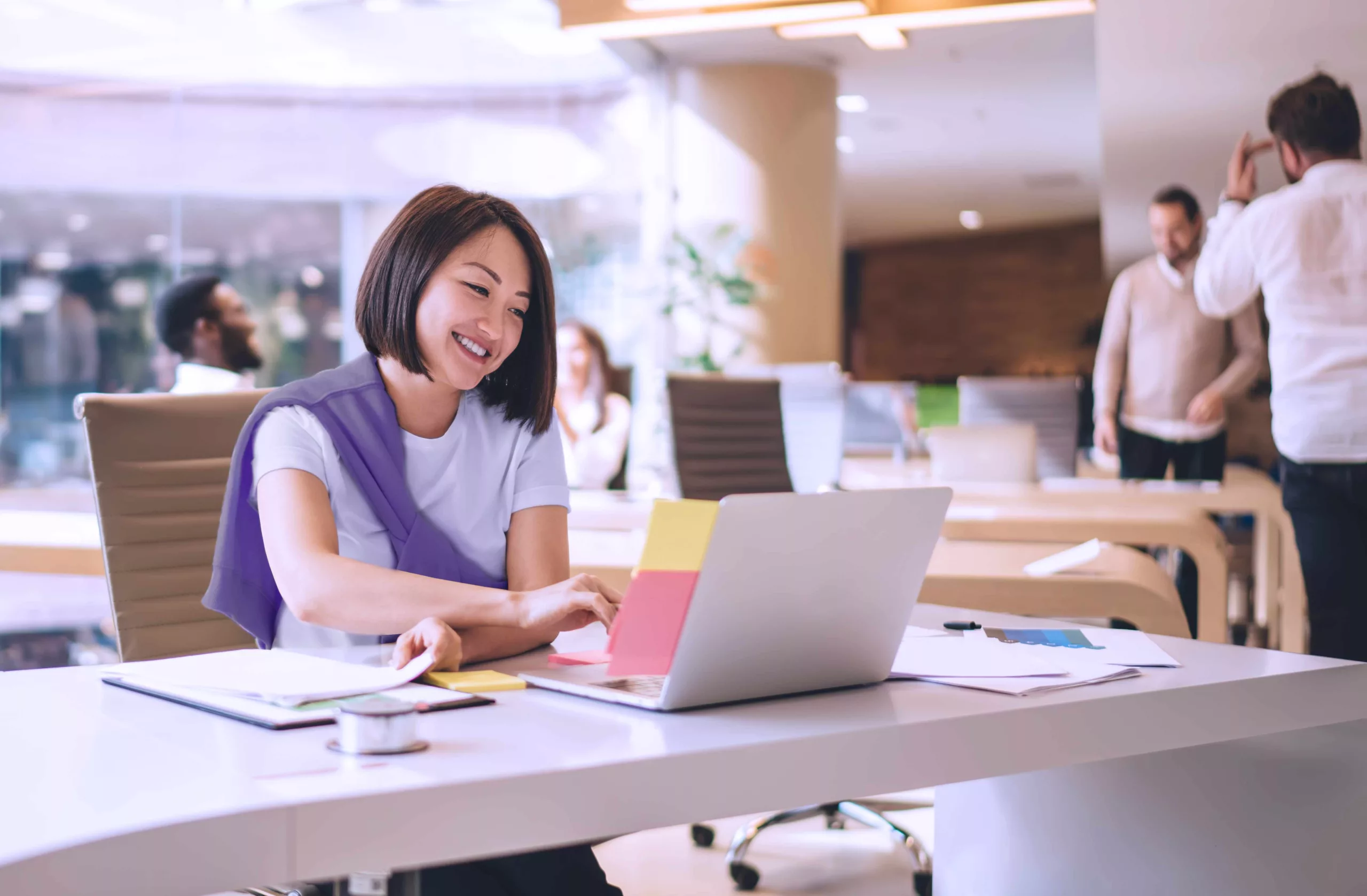
Embarking on a journey to understand employee wellness programs, I’ve come to realise they’re much more than just a corporate buzzword. They’re a pivotal aspect of modern workplaces, aimed at enhancing the well-being of employees both inside and outside the office. It’s about creating a supportive environment where everyone can thrive. At their core, employee […]
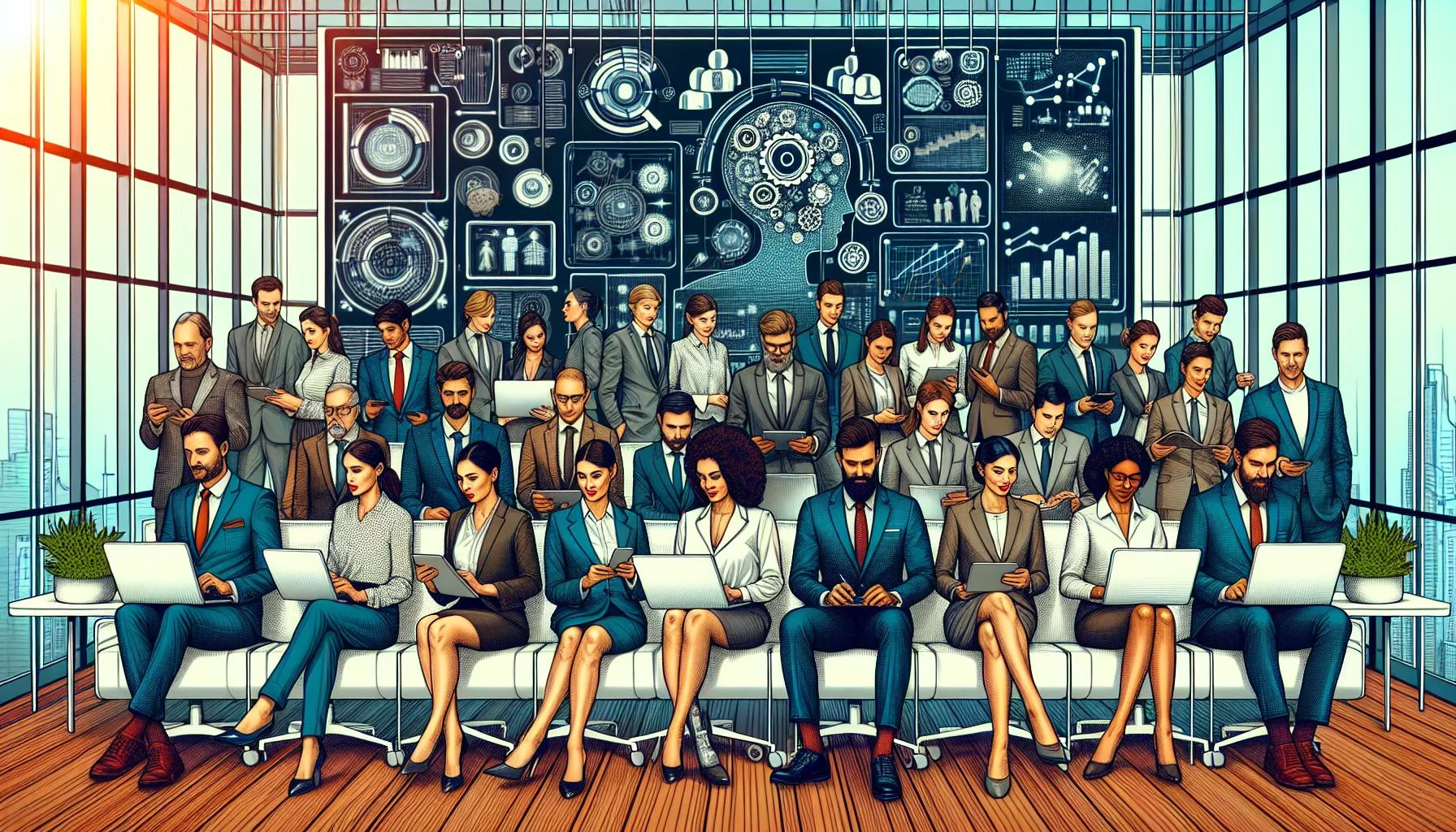
In today’s fast-paced business world, we understand it’s not always easy to keep up with the latest HR trends and regulations. That’s where HR consulting services come into play. With their expert knowledge and strategic insights, they can help streamline your HR processes, ensuring you’re always ahead of the curve. Whether it’s talent acquisition, workforce […]
- Vision and Values
- Member Case Studies
- Member Directory
- Membership Levels
- Meet the Team
- Delivery Partner
- In the Media
- Assess your knowledge level
- Training Events and Workshops
- E-Learning Modules
- E-learning Modules
- Documents and Presentations
- Case Studies
- Beginner-Level Resources
- Intermediate-Level Resources
- Advanced-Level Resources
- My Dashboard
- Learning Pathways
- On-Demand Learning
- Sustainable Development Goals
- Construction
- Facilities Management
- Finishes & Interiors
- Infrastructure
- Future Workforce
- Wales – Cymru
- Air Quality
- Biodiversity & Ecology
- Business Ethics
- Energy & Carbon
- Environmental Management
- Fairness, Inclusion & Respect
- Modern Slavery
- Performance Measurement and Management
- Social Value
- Sustainability Strategy
- Sustainable Procurement
- Waste & Resource Efficiency
- Business Case for Digital
- Cyber Security
- Digital Adoption
- Digital Leadership
- Digital Capability
- FIR Ambassadors
- FIR Case Studies
- FIR Growth Assessment
- FIR Toolkit
- Site Environment
- Supply Chain
- Working practices
- 5S Workplace Organisation
- Collaborative planning & production control
- Lean construction & waste
- Problem solving & continous improvement
- Standardised work
- Value stream mapping
- Visual management
- Change management
- Collaboration
- Marketing & business development
- Project management
- Quality management
- Supply chain management
- Design for Manufacture & Assembly
- In-use / Maintenance
- Offsite for everyone
- Offsite manufacture
- Employment conditions
- Human Rights
- People Matter Charter
- Right to work
- Training & skills
- Collaborative Construction Procurement
- Collaborative Construction Procurement Training Hub
- Procurement for Beginners
- Procurement for Professionals
- Supplier Relationship & Management
- Supply Chain Improvement Programmes
- Value Toolkit
- About our Partners
- Our Partners’ Approach
- Climate Action Group
- Construction Group
- Digital Group
- Facilities Management Group
- Fairness, Inclusion & Respect Group
- Finishes & Interiors Group
- Future Workforce Group
- Homes Group
- Infrastructure Group
- Modern Slavery Group
- Nature Recovery Group
- Offsite Group
- Operational Excellence Group
- Plant Group
- Procurement Group
- Retrofit Group
- Scotland Group
- Social Value Group
- Wales Group
- Waste and Resource Use Group
- Wellbeing Group
- Become a Partner
- Partner Login
- Partner Pack
- Partner Workshop Catalogue
- School in Australia
- Campus Hors-site (France)
Home » Topics » Operational Excellence » Problem Solving and Continuous Improvement
Operational Excellence through Lean Thinking
Problem Solving and Continuous Improvement
Lean techniques can be used to solve problems that happen on site
Search our catalogue of FREE Lean training resources
Problem solving & continuous improvement.
Lean techniques can be used to solve problems that happen on site, such as damaged materials, late deliveries, and not meeting schedule deadlines by investigating the root causes and involving everyone relevant and then putting fixes in place.
A Lean approach to problem solving normally involves the use of a specific method to get to the root cause of any particular issue.
This includes specific, proven techniques such as the “5 Whys” or developing a herringbone diagram (see the resource library to find out more) to understand all of the different factors which have contributed to any particular issue; the theory being that once you have broken a problem down into smaller chunks it becomes easier to solve.
Another fundamental concept in Lean problem solving is that problems to not arise as a result of individual mistakes by people but instead are caused by a failure of the system itself. Lean Problem solving then allows you to understand what the problems within the system are so they can be fixed.
Construction Productivity: The need and opportunity
This video highlights the need to improve construction productivity, breaking this down into the efficiency and effectiveness of current operations and identifying opportunities for improvement.
Practical Steps to Improve Productivity
This video explores the practical steps to improve construction productivity on any project or process, the team’s roles in implementing these changes, and the benefits of doing so.
Selected Lean learning resources
Have a look at our latest Lean Construction resources which we hope will help you on your Lean Construction journey.
E-learning Module
Introduction to Lean
Lean Tracker
Creating a problem-solving culture.
Document / Presentation
GEMBA is a Powerful Piece of your Lean Toolbox
Building blocks of lean construction.
There are key elements to Lean Construction and we have learning resources available to explain each to you and to help you start embedding lean in your organisation.
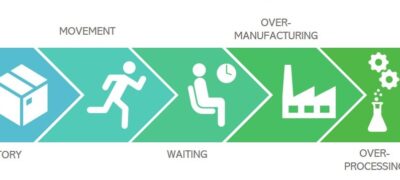
Lean construction takes the concept of waste beyond materials and…
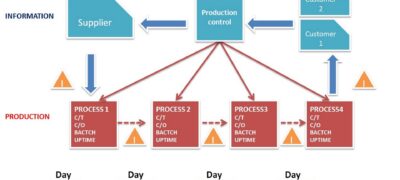
Value stream mapping is a technique used to sequence all…
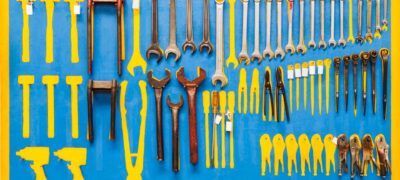
5S workplace organisation is a key tool in Lean construction...

Visual management is a method of managing the workplace using…
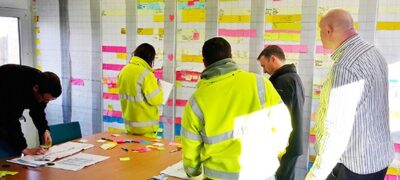
Collaborative planning and production control are methods used to ensure…
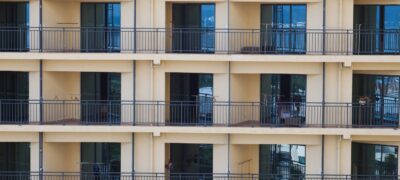
Standardisation is used in Lean to make processes better by…
Lets get started . . .
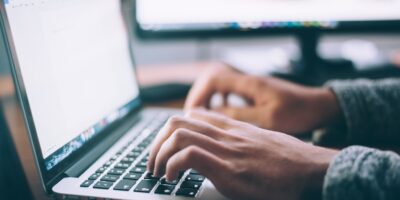
Six steps to successful supply chain collaboration
This article first appeared in the Q2 2012 issue of CSCMP's Supply Chain Quarterly ( www.supplychainquarterly.com )
SUPPLY CHAIN COLLABORATION is a hot topic today—and no wonder: companies that collaborate effectively across the supply chain have enjoyed dramatic reductions in inventories and costs, together with improvements in speed, service levels, and customer satisfaction.
Collaboration between companies—joint initiatives that go beyond their normal course of day-to-day business, with the aim of delivering significant improvement over the long term—is particularly attractive for the consumer packaged goods (CPG) sector. With pricing under pressure from recession-scarred consumers, the temptation for retailers is to transfer the pain upstream to their suppliers by passing on price reductions and forcing them to bear an increasing share of costs. On the supply side, however, there is less and less room for manufacturers to absorb additional costs as volatile input prices put the squeeze on margins and the marketing investment required to differentiate branded products from private-label competitors continues to rise.
CPG players are looking at collaboration initiatives as a way out of the damaging spiral of antagonistic relationships. That’s one reason why collaboration efforts between manufacturers and their retailer customers have dramatically grown in popularity in recent years. That was clearly evidenced in the 2008 annual Customer and Channel Management (CCM) Survey, conducted by McKinsey & Company, Nielsen, and the Grocery Manufacturers Association, when chief executive officers in the CPG industry identified collaboration with partners as their highest strategic priority 1 1. Unpublished result from 2008 Customer and Channel Management Survey—Doing More with Less: Winning Sales Strategies to Navigate a Challenging Market. Grocery Manufacturers Association (2008). . In the 2010 edition of the same survey, more than 80 percent of the companies surveyed said they were involved in at least one collaboration initiative, and some were involved in as many as 10 such arrangements 2 2. 2010 Customer and Channel Management Survey—Emerging from the Storm: How Leading Customer Organizations Reignite Growth. Grocery Manufacturers Association (2010). .
Supply chain collaboration has delivered some real value for participants, but overall, these initiatives are more likely to fail than to succeed. Indeed, participants in the 2010 CCM survey said that only two in 10 of their collaboration efforts delivered significant results. The remaining 80 percent represent more than just lost opportunities to add value. If companies can’t make collaborations work, they will not only fail to achieve the potential benefits that supply chain collaboration can provide, but they will also risk destroying the enthusiasm for further attempts, both inside their own organizations and with their trading partners.
The high rate of failure among today’s collaborations is not inevitable, however. There are several ways CPG manufacturers and retailers can avoid some of the common pitfalls and achieve the benefits they seek. This article will first consider some of the conditions and practices that prevent effective collaborations, and then outline six actions manufacturers and retailer partners can take to ensure success.
Why collaboration is hard
In our work helping retailers and CPG manufacturers manage their collaboration efforts, we have seen a handful of factors that make collaboration problematic. Some of these will be familiar to any organization that’s involved in a large-scale change process. Companies may, for example, lack the commitment they need from senior management to drive the collaborations, or the message that the collaboration is important may be “lost in translation” as it passes down through the organization, with the result that middle managers or front-line teams don’t show the same enthusiasm and commitment as their leadership does. Sometimes companies fail to provide sufficient resources to make collaborations work, or they spread limited resources too thinly over too many initiatives.
These issues are difficult enough to overcome, but they are compounded by the fact that collaboration initiatives must align two separate organizations. To make the collaborations work, the players involved must navigate differences in organizational design and culture. At the same time, a history of difficult relationships can make partners reluctant to share important information, leading them to work on their parts of the “collaboration” in separate silos—a recipe for suboptimal solutions.
Finally, the incentives of the different parties involved in the collaboration may be fundamentally misaligned, making it difficult even for enthusiastic, committed staff to make the collaboration work while still fulfilling their other targets. These misaligned incentives arise because different players in the supply chain may see the world in very different ways. A manufacturer, for instance, might want to grow its market share by improving its own offerings relative to competitors, whereas a retailer might be interested in increasing sales or margins across the category, not in changes to product mix.
This difference in outlook can mean that retailers and manufacturers want very different things from the collaboration. Growth-focused manufacturers may be enthusiastic about new promotional opportunities, while retailers operating on thin profit margins may be much more interested in taking cost out of product handling and storage. The relationship and power dynamics between collaborating partners can be dramatically different, too. Manufacturers typically will have relationships with a small number of key retailers, while those same retail partners will have relationships with hundreds of different suppliers.
The following case of a major food manufacturer and a retail chain provides an instructive example of how collaboration can go wrong when participants don’t trust each other enough. The two companies agreed to collaborate on a co-branded product line. The retailer hoped that the manufacturer’s brand name would boost both the credibility and the sales of its product, while the manufacturer saw the partnership as a way of increasing its own market share within the retailer’s network.
The collaborative effort failed to play to either company’s strengths, however. The retailer’s rich point-of-sale and consumer-preferences data provided the information needed to develop an accurate profile of its customers’ requirements, but concerns about sharing that information led the retailer to analyze the data and develop the product specification itself without the benefit of the manufacturer’s category expertise. The resulting product was expensive to make and missed the mark on package size, product specifications, and shelf appeal. Sales were disappointing, and within months the partners were forced to reassess their relationship.
Making the right choices
Consumer packaged goods companies can greatly improve their prospects for success by taking a thoughtful approach to the areas they select for collaboration, their choice of partners, and the way they implement their collaborations. Based on our experience, we have identified six essential steps summarized in Exhibit 1 that can make the difference between a productive collaboration and a frustrating one.
1. Collaborate in areas where you have a solid footing. Companies are often tempted to use collaboration as a way to fill gaps in their own capabilities. In practice, the most successful collaborations build on strengths rather than compensating for weaknesses. A manufacturer seeking to collaborate with a major retailer in order to improve its own forecasting performance, for example, will have little to gain from access to the retailer’s point-of-sale data unless it has the in-house analytical capability to make effective use of that data. Similarly, there is little point in entering collaborations to boost sales if any increase in demand is likely to run into manufacturing-capacity constraints.
Potential collaborators should also be sure they have the right supporting infrastructure in place in advance of any collaborative effort. Is the top management committed to the collaboration process and ready to offer support over the long term? Are inhouse information technology (IT) systems robust enough to facilitate real-time data sharing if required?
2. Turn win-lose situations into win-win opportunities with the right benefit-sharing model. Some collaborations promise equal benefits for both parties. If, for example, a manufacturer and a retailer collaborate to optimize product mix, both could expect to benefit from the resulting increase in sales. In other cases, however, the collaboration might create as much value overall but the benefit could fall more to one partner than to the other. Here’s one real-life example: a retailer and a manufacturer were able to reduce overall logistics costs between factory and store by cutting out the manufacturer’s distribution centers and treating the retailer’s distribution network as one integrated supply chain, from manufacturing plant to store shelf. However, the retailer’s supply chain executives struggled to gain acceptance for the idea from their leadership because it resulted in the retailer carrying a far larger fraction of the logistics cost.
Rather than shying away from such asymmetric collaborations, smart companies can make them work by agreeing on more sophisticated benefit-sharing models. These can come in the form of discounts or price increases to more fairly share increased margins or cost reductions, or they can involve compensation in other parts of the relationship. For example, when one retailer collaborated with a manufacturer on a cobranded product line, the manufacturer agreed to absorb the upfront product-development costs in return for an expanded share of the retailer’s product offerings across a wider set of categories.
Benefit sharing can help to overcome differences in strategic priorities, too. One growth-focused manufacturer was persuaded to join a supply chain waste reduction collaboration with a retailer by establishing an agreement to deposit part of the savings both companies achieved into a joint pool, which would then be invested in efforts to generate additional sales.
Similarly, in the product-flow improvement case described in the sidebar (page 6), the manufacturer provided the upfront investment in new retail-ready packaging, while its retail partner reaped most of the benefits in terms of increased availability and reduced labor costs. The two companies established a joint benefits pool and agreed to use a percentage of the savings to fund future cost-reduction efforts and a sales-improvement program.
3. Select partners based on capability, strategic goals, and value potential. The biggest potential partner might not be the best one. Many companies aim to collaborate with their largest suppliers or customers because they assume that the greatest value is to be found there. In many cases, however, this turns out not to be true. Collaboration may be of more interest to a smaller partner, which might invest more time and effort in the program than a very large one that is already juggling dozens of similar initiatives.
A better approach is one that assesses current customers or suppliers across three key dimensions. First, is there enough potential value in collaborating with this partner to merit the effort? Both partners in a prospective collaboration need to be sure that it will deliver a sufficient return to justify the upfront investment. Second, do both partners have sufficiently common strategic interests to support the collaboration? A retailer that has prioritized growth in a particular region or segment will have more to gain from collaborating with a manufacturer that has a strong offering in the same area. Third, does the partner have the right infrastructure and processes in place to provide a basis for the collaboration? Collaborating to improve forecasting and demand planning is likely to be frustrating if one partner’s existing planning processes, systems, or performance are inadequate.
4. Invest in the right infrastructure and people. Both manufacturers and retailers that participated in our research cited a lack of dedicated resources as one of the top three reasons for the failure of collaboration efforts. Companies frequently underestimate the resources required to make collaborations work, assuming that staff in various functions can do what’s required in addition to their other responsibilities.
In practice, even relatively simple collaborative tasks will be more difficult than equivalent activities conducted within the walls of the organization. That’s because staff must overcome differences in culture, organization, and terminology, not to mention the basic challenge of finding the right contact within the partner organization with whom to liaise.
Disconnects within one organization can create problems, too. A “grassroots” collaboration started between two supply chain managers can lead to rapid performance improvements, only to be snuffed out when those higher in the organization fail to understand the initiative’s potential. Alternatively, a collaboration agreement made between two board-level executives will fizzle out if the managers responsible for executing it think it is yet another short-lived senior management whim, if they can’t see how the collaboration will help them achieve their own objectives, or if they lack the incentive to put additional effort into the project on top of their existing day-to-day roles.
To prevent both of these problems, best-practice companies devote extra resources to their collaborations, particularly in the early stages of a new relationship. Appropriate infrastructure for a successful collaboration begins at the top of the organization, with a steering committee of senior leaders who can set the defining vision for the collaborative effort and allocate resources to support it. The detailed design of the collaboration program is then completed by a team comprising members of all relevant functions from both partners in the collaboration. The team for a demand-planning effort, for example, should include members from sales, finance, and supply chain for the manufacturer, and from purchasing, merchandising, and store operations for the retailer. This team will also be responsible for the day-to-day monitoring of the effort once it is up and running.
Execution of the collaboration should take place within the line organization and will ultimately form part of the everyday responsibility of the staff assigned to it. The best companies avoid forcing their front-line staff to “reinvent the wheel” by providing strong support when establishing each new collaboration. They may, for example, leverage experience gained in previous collaborations by setting up teams to support their colleagues during the initial phase of subsequent efforts.
5. Establish a joint performance-management system. An effective performance-management system helps a company to ensure that any long-term project is on track and delivering the results it should. In supply chain collaboration efforts, both participants should use the same performance-management system. By building common metrics and targets—and jointly monitoring progress—companies avoid the misaligned incentives that damage so many collaboration efforts.
Picking the right metrics can be challenging, however, and it will inevitably involve trade-offs. In a collaboration to reduce logistics costs, for example, the partners may have to choose between a pallet configuration that’s optimized to suit a retailer’s restocking processes, which will reduce in-store labor costs, and one that optimizes truck fill, which will reduce transportation costs from distribution center to retail store.
How to overcome these potential conflicts? The trick is to keep things simple by picking the smallest possible number of metrics required to give a picture of the collaboration’s overall performance, and then to manage those metrics closely, with regular joint reviews and problem-solving sessions to address trade-offs. The real power of any performance-management system comes from this frequent, robust dialogue between partners, yet this is also the element most commonly ignored or underemphasized by collaborating companies.
6. Collaborate for the long term. The final vital ingredient of a successful collaboration is stamina. It may take time and effort to overcome the initial hurdles and make a new collaboration work. Both parties need to recognize this and build an appropriate long-term perspective into their goals and expectations. This means including metrics that review performance beyond the first year, as well as conducting joint, long-term planning so both partners can understand each other’s longer-term objectives and identify initiatives they can work on together over time. Such planning helps companies to break out of the short-term project mentality that can limit the beneficial impact of collaboration. Nevertheless, partners must also ensure that they are doing everything they can to capture any available quick wins, so the collaboration starts delivering value as quickly as possible.
When companies take a long-term perspective, their collaborative efforts can become a virtuous circle: a greater understanding of each other’s capabilities, knowledge, and costs will often reveal new potential sources of value, while the experience of working closely together means that later initiatives will take less time and be easier to execute than early ones.
Potentially huge payback
It should be clear by now that successful supply chain collaboration is neither quick nor simple. But is it worthwhile? The answer has to be an emphatic “yes.” In our experience, successful CPG collaborations that involve two or three separate initiatives in a category deliver a return that’s equivalent to a profit uplift of 5 percent to 11 percent in the affected category, through a combination of increased sales and reduced costs.
What could that mean for the consumer packaged goods sector as a whole? Our models suggest that if a grocery retailer could collaborate in this way with the top three brands in each of its top 25 grocery categories, it would enjoy benefits equivalent to a 4-percentage point increase in its EBIT (earnings before net interest and tax) margin. For manufacturers, the same level of collaborative intensity with their top 10 retailers could boost margins by 5 percentage points. And for the North American CPG sector as a whole, that kind of impact could potentially be worth US $8–$12 billion— comparable to two years of industry growth.
Process technology in action: The tipping point of disposable technology
In McKinsey & Company’s work with consumer goods manufacturers and retailers, we have identified six broad areas where companies can collaborate for mutual gain:
- Category strategies
- Merchandising and in-store layout
- Joint innovation
- Demand planning and fulfillment
- Collaborative sourcing
- Joint flow efficiency
The final three of these have direct supply chain implications, and in each case, successful collaborations have delivered profound improvements in supply chain performance. The following are some examples we have seen:
A beverage manufacturer and a retailer collaborated to improve demand planning and fulfillment . Prior to the collaboration, the retailer’s ordering process did not match changes in consumer demand, with the result that shipments from the manufacturer fluctuated twice as much as did retail sales. To avoid stock-outs under this regime, both the manufacturer and the retailer were forced to keep high levels of inventory on hand.
Working together, the manufacturer and retailer agreed on a joint forecasting and demand-analysis system. They improved their information sharing, too: the retailer gave the manufacturer access to its on-shelf availability data, which allowed the two companies to modify product distribution to maximize availability in individual stores, while the manufacturer informed the retailer about supply constraints that might limit its ability to meet high levels of demand at short notice. The partners also agreed to stagger promotional activities among regions to reduce overall demand peaks. The introduction of the new system cut shipment volatility by onethird, allowing both the retailer and the manufacturer to achieve inventory reductions of more than 15 percent and increase profit margins by 3 percentage points.
Another area for fruitful collaboration is sourcing. One large U.S. retail chain has used collaborative sourcing to great effect across a broad range of categories and geographies. In an effort to combat rising raw-materials prices in key categories, the company established joint sourcing programs with manufacturers to purchase key commodities for both its own private-label products and the manufacturers’ brand-name items. Collaborations have included the sourcing of potatoes for chips manufactured in the United States and sugar for soft drinks manufactured in the United Kingdom, with the latter effort securing a 14-percent cost saving.
Finally, the case of a retailer and food manufacturer shows how collaboration can work to dramatically improve product flow efficiency . The manufacturer produced packaged foods in a large assortment of flavors, making it difficult for its retail partner to manage inventories across the category. This required time-consuming and labor-intensive efforts to keep the shelves stocked.
The two companies tackled these issues by developing retail-ready packaging that made it easier to keep the shelves stocked while also optimizing the way delivery trucks were loaded. The new packages were designed to fit into jointly developed in-store display units that held more products and made items easier to find than the conventional shelves they replaced. As a result, the average time it took consumers to select an item dropped from 58 seconds to just 8 seconds. The companies then changed the replenishment system to accommodate the new display units. They segmented various retail sites by volume, velocity, and volatility, and then optimized shipment sizes and replenishment frequency for each segment. For the highest-velocity stores, the partners introduced a rapid-replenishment program in which deliveries were timed to coincide with peak selling days.
Luis Benavides is an associate principal, Verda De Eskinazis is a consultant, and Daniel Swan is a principal, all at the global consulting firm McKinsey & Company.
Explore a career with us
Enhancing Problem-Solving Skills in Supply Chain Teams: Finding Innovative Solutions to Challenges
Explore the importance of enhancing problem-solving skills in supply chain teams and find innovative solutions for the complexities these teams continuously face!

In today’s fast-paced and dynamic business landscape, supply chain teams face a myriad of challenges that require agile and innovative problem-solving. From unforeseen disruptions to ever-evolving customer demands, the ability to effectively address and resolve issues is crucial for maintaining a competitive edge. In this article, we will explore the importance of enhancing problem-solving skills in supply chain teams and provide strategies for finding innovative solutions for the complexities faced in the modern supply chain.
The Significance of Effective Problem-Solving in the Supply Chain
Supply chains are complex networks that encompass various stakeholders, processes, and technologies. Despite meticulous planning, unexpected challenges can arise at any stage, impacting the entire chain. Efficient problem-solving is not just about fixing issues when they arise; it is also about proactive thinking to anticipate and prevent potential disruptions. Some key reasons why effective problem-solving is essential in the supply chain include:
- Mitigating Disruptions: Timely and efficient problem-solving minimizes the impact of disruptions, ensuring that the supply chain continues to operate smoothly.
- Cost Optimization: Problem-solving that addresses inefficiencies and bottlenecks helps optimize costs and resource allocation.
- Customer Satisfaction: Rapid resolution of supply chain issues ensures that customers receive their orders on time, fostering customer loyalty and satisfaction.
- Continuous Improvement: Emphasizing problem-solving fosters a culture of continuous improvement, encouraging teams to seek innovative solutions.
Strategies for Enhancing Problem-Solving Skills
- Foster a Collaborative Environment: Encourage open communication and collaboration among supply chain team members. Creating a safe space for sharing ideas and perspectives allows diverse insights to come together, leading to more robust problem-solving.
- Emphasize Root Cause Analysis: Train teams to identify the root causes of problems rather than merely addressing the symptoms. Root cause analysis enables teams to tackle issues at their source, preventing recurring problems.
- Promote Creative Thinking: Encourage out-of-the-box thinking and brainstorming sessions. Innovation often comes from unconventional ideas, and promoting creative thinking helps teams discover unique solutions to complex challenges.
- Implement Problem-Solving Frameworks: Introduce problem-solving frameworks such as the PDCA (Plan-Do-Check-Act) cycle or Six Sigma methodologies. These frameworks provide structured approaches to problem-solving, ensuring teams follow a systematic process.
- Utilize Data-Driven Decision Making: Leverage data analytics and technology to make informed decisions. Data-driven insights provide a deeper understanding of supply chain dynamics and support evidence-based problem-solving.
- Encourage Continuous Learning: Invest in training and development programs to equip supply chain teams with the latest problem-solving techniques and industry best practices. Continuous learning enhances the team’s capabilities and adaptability.
- Conduct Post-Problem Analysis: After resolving a problem, conduct a post-problem analysis to evaluate the effectiveness of the solution. This analysis helps identify areas for improvement and provides valuable lessons for future challenges.
- Seek External Perspectives: Engage external consultants or subject matter experts to bring fresh perspectives to complex supply chain issues. External viewpoints can shed light on blind spots and offer innovative insights.
- Embrace Technology and Automation: Integrate technology and automation into problem-solving processes. Advanced supply chain management systems, AI-driven analytics, and predictive modeling can streamline decision-making and identify potential issues beforehand.
- Reward and Recognize Problem-Solving Success: Acknowledge and celebrate successful problem-solving efforts within the supply chain team. Recognizing team members’ contributions motivates them to tackle future challenges with enthusiasm and dedication.
Enhancing problem-solving skills within supply chain teams is vital for driving success and maintaining a competitive advantage in today’s dynamic business landscape. By fostering a collaborative and innovative culture, promoting data-driven decision-making, and investing in continuous learning, supply chain leaders can equip their teams with the tools they need to tackle challenges head-on. Embracing problem-solving as a continuous process of improvement and learning empowers supply chain teams to find innovative solutions, optimize operations, and deliver exceptional value to customers and stakeholders. With a strong emphasis on problem-solving, supply chain teams can navigate complexities with confidence, ensuring the efficient flow of goods and services to meet the demands of the ever-changing market.
The Perfect Planner Team is here if you have any questions about Enhancing Problem Solving Skills in Supply Chain Teams, and we offer a free consultation service. If you would like to connect with us on this article or any other topic, please message us on LinkedIn, shoot us an email at [email protected], visit our website at www.perfectplanner.io, or give us a call at 423.458.2979.
Author: Thomas Beil
Publication Date: February 29, 2024
© Copyright 2024 Perfect Planner LLC. All rights reserved.
Navigating the Red Sea Shipping Crisis: Implications and Insights
Back to news
How to Solve Your Supply Chain Challenges
The Blume Global Team
February 14, 2019
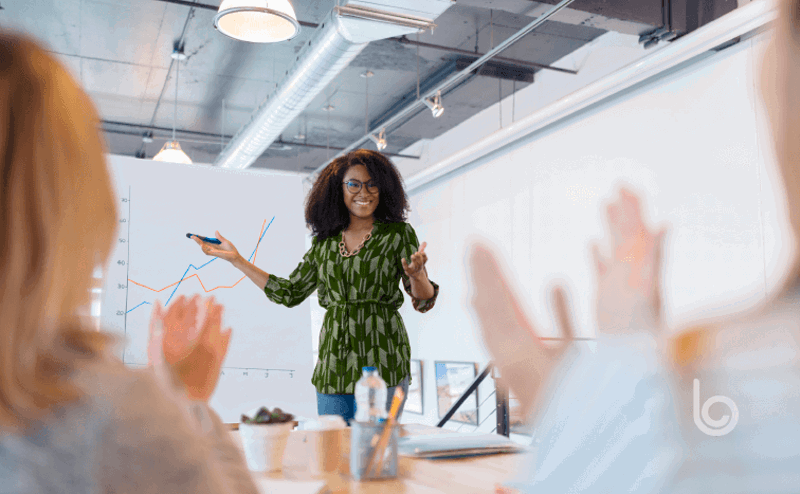
The increasing complexity of international supply chains means that supply chain managers must use a combination of tools, techniques and approaches to meet everyday and long-term challenges. We’ve explored some of the main pressures and demands on the supply chain and in this post, we present some ways to help you manage your supply chain more effectively.
Manage and Drive Down Costs in the Supply Chain
Rising fuel, commodity and labor costs can drive up charges for organizations throughout the supply chain that ultimately get passed on to the end business. Supply chain managers need to understand and control cost challenges.
Visibility of Costs Through Accurate Budget Control and Reporting
Good cost control relies on transparency. All organizations in the supply chain should report on their costs and overheads in a common and centralized way to allow for accurate cost tracking and reporting. This reporting can be linked to financial metrics and provide early sight of cost leakage and other financial issues.
Robust Cost Controls Built Into Contracts and Service Level Agreements
Supply chains work best when everything is clearly defined. Make sure that all contract documents, statements of work and service level agreements (SLAs) make specific mention of costs and cost controls. Build a cost review process into sourcing, manufacturing, logistics and other operations with proper accountability both within third-party organizations and the supply chain team.
Blume Finance enables transparency and granular visibility for freight audit and pay with a smart contract repository, rating management and validation, machine learning-driven invoicing, cost accrual auditing and blockchain-enabled payment and settlement.
Optimize Inventory and Supply Chain Demands Across Multiple Channels
The number of ways that businesses and individuals can acquire goods has increased dramatically. Supply chain managers need oversight across every route to market with accurate demand planning. This will help you to maintain appropriate inventory levels, so channels don’t run out of products.
View All Marketplace Channels in One Place
Managing demand through a supply chain is difficult enough when you only need to look at a couple of distribution routes. Add in third-party marketplaces, ecommerce, wholesale or dropshipping and things become much more complex. Supply chain managers need transparent reporting that shows supply and demand planning across all channels. This allows you to react to demand changes quickly, so you can raise orders and reroute inventory before stock levels become an issue.
Use Predictive and Prescriptive Analytics to Identify and Model Sales Trends
Product demand is influenced by past trends, marketing promotions, competition, new products hitting the market and more. Supply chain managers should model likely future demands using predictive and prescriptive analytics , feeding in historic data, marketing plans, competitor activity and any other relevant information. This will help you plan ahead and order products before there’s undue pressure on inventory levels.
Blume optimizes assets, logistics and supply chains with AI- and ML-driven matching for assets and transportation legs. For LSPs that need to minimize empty container moves and manufacturers that need to streamline supply chain operations, Blume Optimization helps minimize costs, maximize capacity and improve agility.
Improve Quality and Speed in the Supply Chain
Supply chains can always become more efficient. Good supply chain managers will introduce continual improvement initiatives to maximize quality and eliminate bottlenecks and delays.
Introduce Internal Checkpoints and Quality Control
You need visibility of the quality and condition of raw materials, parts and finished products as they move through the supply chain. A combination of independent auditors, quality checkpoints and monitoring devices helps make sure that products are sourced and manufactured to your exact standards. These standards should be clearly documented in contracts, SLAs and other documentation.
Track the Movement of Goods Through the Supply Chain
IoT devices will track goods wherever they are in the world using GPS. This allows supply chain managers to identify the location of goods at any time and can prepare downstream organizations like manufacturers to prepare for receipt and processing.
Build a Continual Improvement Process Into the Supply Chain
Analysis of supply chain data is an excellent starting point for improvement initiatives. Managers can collect data on quality, speed, price or any other key metrics to reduce waste or drive up efficiencies. As you make improvements to supply chain processes, you can continue analyzing data to understand the real-world impact of changes and drive future improvements.
Blume Visibility removes dark areas and provides clear visibility across every move, mode and mile by tracking events, predicting ETA, flagging exceptions and facilitating proactive resolution of disruptions. Unparalleled network visibility and intelligent execution help improve supply chain performance, resilience and responsiveness.
Manage and Mitigate Risks and Issues in the Supply Chain
Risk is a natural part of the supply chain ecosystem. Complex international supply chains can be impacted by issues including:
- Tariffs, fees and customs processing delays
- Failure to meet regulatory or compliance demands
- Port congestion and delays in storing or transporting products
- Economic, environmental and political risks impacting the free flow of goods
These problems are too big for a single organization to resolve, so it’s essential that supply chain managers have the right visibility, tools and approaches to plan around and mitigate these risks.
Get Early Sight of Potential Supply Chain Issues
Risk management is another area where supply chain transparency is essential. Create “one source of the truth,” a centralized information repository where you collect data from throughout the supply chain. Use this repository to run reports, set thresholds and track metrics closely and identify potential problems before they become a big issue. Use AI and machine learning to query data, set a baseline and spot unusual patterns that might turn into showstoppers down the road.
Create Excellent Relationship Management Disciplines
Supply chains rely on strong relationships with suppliers, manufacturers, logistics and other third parties. Although the governance of that relationship will be captured in contracts and service level agreements, excellent day-to-day relationship management will increase goodwill and help you resolve issues. Clarity and communication through the supply chain will help supply chain managers and other organizations to collaborate more closely.
Plan for Contingencies and Mitigating Actions
Creating backup plans and mitigating actions is essential to a healthy supply chain. Build contingencies into the supply chain like backup suppliers and manufacturers, alternative logistics provisions, overflow storage solutions and similar business continuity planning. Prioritize risks to the supply chain in terms of likelihood and impact and plan for worst-case scenarios. Build mitigating action plans with proper accountability so you can respond to supply chain emergencies quickly.
Blume Logistics creates a robust network for logistics tendering, tracking, event capture, POD verification and settlement initiation. By connecting a global ecosystem of multi-modal carriers to manage every move, Blume Logistics unites carriers—from ocean to rail to long haul—with first- and last-mile drayage for real-time event and cost tracking.
Use the Right Supply Chain Software Platform
If you want to manage supply chain challenges effectively, you need the right tools. A centralized supply chain software platform that integrates with organizations throughout the supply chain gives you the visibility and approaches you need to reduce costs, remove risks and maximize efficiencies.
Blume Digital Platform will help you to:
- Analyze your supply chain using customizable views, dashboards and KPIs
- Track contract performance and manage complex transactions
- Integrate with organizations throughout the supply chain for easier reporting and relationship management
- Optimize logistics through better asset allocation and opportunities to match loads by time, distance and cost savings
- Understand costs throughout the supply chain
- Get end-to-end visibility throughout the supply chain ecosystem
Learn how the Blume Digital Platform uses data to connect trading partners in a collaborative supply chain ecosystem to drive real value and growth for customers worldwide. Our cloud-based platform is open and neutral, and its extensible architecture enables continuous innovation to forge the future of the global supply chain.
Digitization
Supply Chain Basics
Supply Chain Management
Latest news
When will passenger flights alleviate the air cargo capacity crunch, air cargo looks to supply chain digitization during covid pandemic, the trucking industry has a covid-19 problem: technology can help.
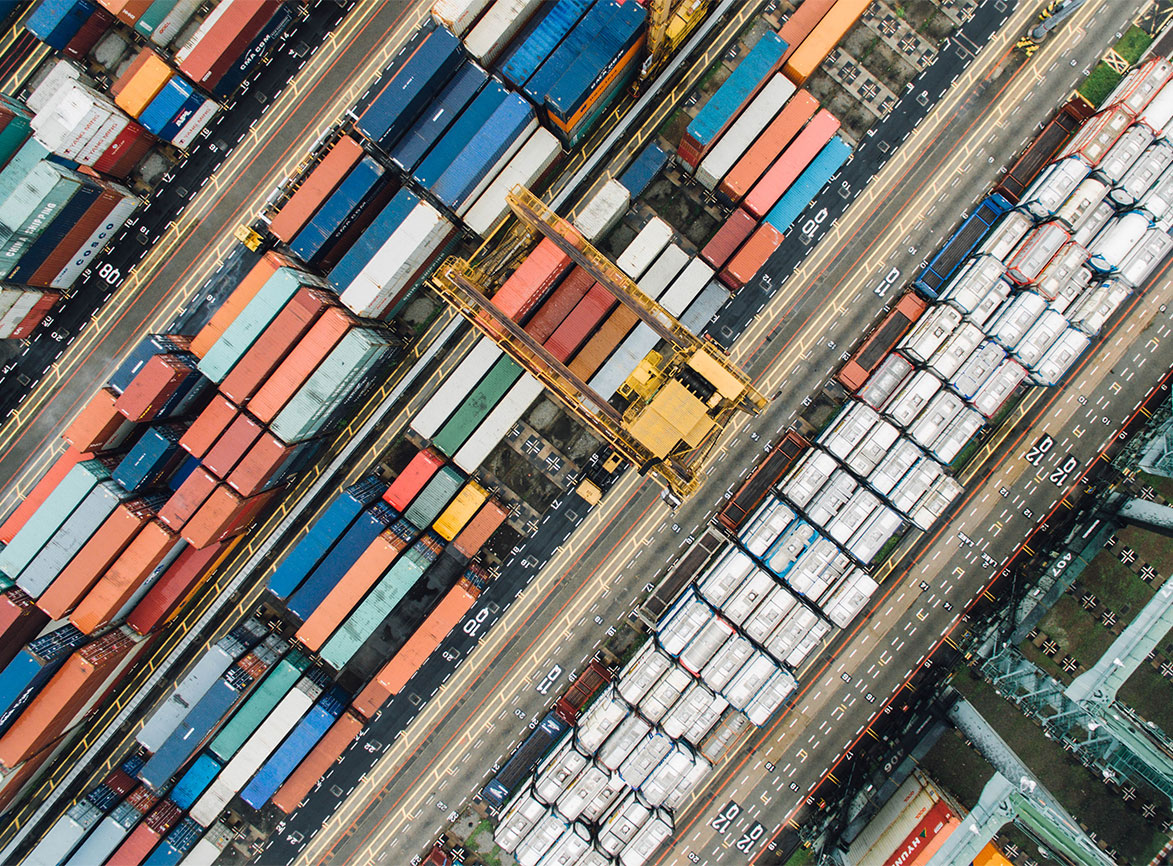
Smart. Open. Grounded. Inventive. Read our Ideas Made to Matter.
Which program is right for you?
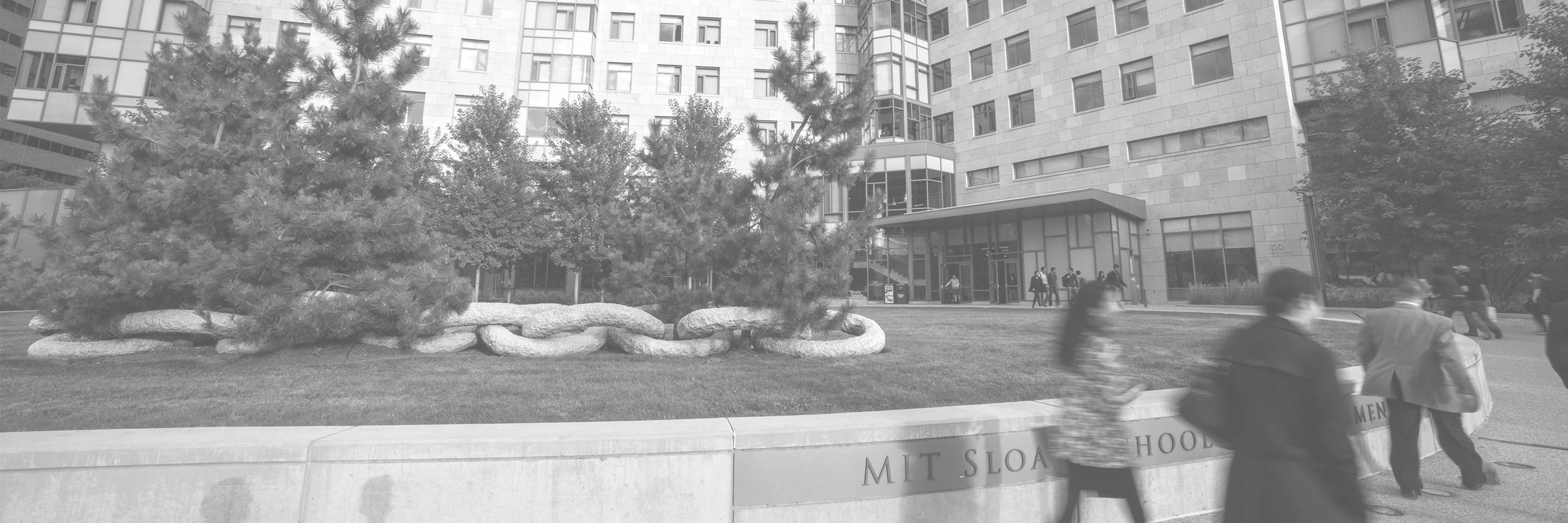
Through intellectual rigor and experiential learning, this full-time, two-year MBA program develops leaders who make a difference in the world.
A rigorous, hands-on program that prepares adaptive problem solvers for premier finance careers.
A 12-month program focused on applying the tools of modern data science, optimization and machine learning to solve real-world business problems.
Earn your MBA and SM in engineering with this transformative two-year program.
Combine an international MBA with a deep dive into management science. A special opportunity for partner and affiliate schools only.
A doctoral program that produces outstanding scholars who are leading in their fields of research.
Bring a business perspective to your technical and quantitative expertise with a bachelor’s degree in management, business analytics, or finance.
A joint program for mid-career professionals that integrates engineering and systems thinking. Earn your master’s degree in engineering and management.
An interdisciplinary program that combines engineering, management, and design, leading to a master’s degree in engineering and management.
Executive Programs
A full-time MBA program for mid-career leaders eager to dedicate one year of discovery for a lifetime of impact.
This 20-month MBA program equips experienced executives to enhance their impact on their organizations and the world.
Non-degree programs for senior executives and high-potential managers.
A non-degree, customizable program for mid-career professionals.
How, and why, to run a values-based business
Accelerated research about generative AI
Disciplined entrepreneurship: 6 questions for startup success
Credit: Shutterstock / Hachi888
Ideas Made to Matter
Supply Chain
6 steps to handle supply chain disruption
Mar 17, 2020
The rapid spread of the novel coronavirus is crippling supply chains around the world, with companies from Apple to Nintendo announcing shipping and manufacturing delays . Other unanticipated events have caused supply chain upheaval in the last few decades, including the Fukushima nuclear meltdown, 2011 floods in Thailand, SARS and MERS pandemics, and Hurricane Katrina.
But it is inaccurate to compare the coronavirus to these other events, said MIT professor Yossi Sheff i , director of the MIT Center for Transportation and Logistics , during a March 16 webinar. COVID-19 is affecting both supply and demand. And today China, where the pandemic started and factories have been affected for weeks, plays a much bigger part in the global economy than it did during past disasters. Businesses are also seeing a reduction in global demand because of fear and online distancing, he said, which could bring about a severe recession.
This is a so-called black swan event , Sheffi said: a rare, unpredictable disruption that causes lasting damage.
Global supply chain effects are spreading slowly but will affect U.S. factories within weeks, Sheffi said, as shipments from China fail to arrive. Supply chain disruptions often have a “bullwhip effect,” he said: They start with retailers and spiral out in greater magnitude to distributers, producers, and then suppliers in the first, second, and third tiers. Upstream suppliers are likely to be severely damaged.
“The second and third tier of the supply chain are usually small and cannot withstand the initial downdraft in orders,” he said. “This could be a death blow for small manufacturers.”
No two disruptions are the same, Sheffi said. But every company should take action to prepare for supply chain disruptions of any kind. Here are six ways to get started.
Establish an emergency management center
During times of crisis companies should centralize information and decision-making functions, Sheffi said. All information should come to one place so decision-makers can talk to each other and take action. In the case of the coronavirus, most of this will be done virtually, he added. While one team focuses on the business ecosystem, taking care of customers and suppliers, another team should focus on taking care of employee concerns — continuing operations, dealing with family matters, and other issues often handled by human resources.
Speak with one voice
Crisis communication is key during disruptions, Sheffi said, and companies should be prepared to communicate with all stakeholders: employees, customers, suppliers, media, shareholders, analysts, and the community.
The key is to speak with one voice, he said, and appoint one person who will share accurate information about the crisis and what the company is doing. “The one voice has to tell everybody exactly what is going on. Don’t try to spin it or blame other people,” he said.
Swim in your lane
Decisions should be made by the appropriate people in the company, Sheffi said, suggesting the mantra “swim in your lane.” During the height of the Fukushima earthquake and nuclear meltdown in 2011, he said, General Motors in Japan did not have access to modules needed to make heated car seats. A company vice president decided to build vehicles without heated seats, which resulted in several problems, including leather components stranded in the supply chain.
With the variety of parts and suppliers that can make up a supply chain, decisions like the one General Motors faced need to be made by people who know what they are doing. “If you are an engineer that deals with seats, you know what can and cannot be done,” Sheffi said. “One of the most important issues in this case is actually to keep the C-suite, the CEO and others, away from making decisions. They should talk to the media, be fully informed all the time, but they should not make the little decisions.”
Map your supply chain and keep an eye on products
Surviving a supply chain disruption means making sure you still have suppliers and a steady flow of parts and materials. Sheffi recommends finding out how your supply chain works through supplier mapping. This includes plant locations (the headquarters may be elsewhere), what each plant makes, and the criticality of different parts — can you build your product without it, or do you have other suppliers of this part elsewhere? Other things to know include each plant’s operational status and inventory level. All of this requires supply chain visibility .
As suppliers feel pressure, look out for quality degradation and late deliveries. Fakes are also a big problem when supplies are scarce, Sheffi said, as companies look for alternative suppliers. You should also know the financial health of suppliers you depend on, and be prepared to support them if needed. “Invest in them, extend their credit terms,” he said. “Make sure that critical suppliers don’t go out of business, because then you go out of business.”
Prepare to manage customer demand
Companies should plan ahead how they will handle customer demand during supply chain disruption. There are several options:
Allocation or product triage. If multiple products use the same part, which product gets the part? Considerations include financial contributions, customer importance, fairness, and need — which customers could go out of business, Sheffi said. Companies should decide on a plan ahead of time, he said, instead of during a crisis.
- Auction. Some companies have auctioned products to the highest bidder. While this seems like a fair method — whoever wants it most gets it — Sheffi said this can be seen as profiteering and drive away customers.
- Dilution. In an attempt to meet demand, some companies stretch supply by diluting products. Facing increased product demand in 2013, Maker’s Mark diluted its bourbon from 90 proof to 84 proof, resulting in customer revolt. The CEO later apologized.
- Substitution, or demand shaping. If a company has some products in short supply and sufficient stock of other similar products, they can raise the price of the scarcer product and lower the price of others to shape customer demand.
Plan for recovery
Companies should think beyond short-term disruption to the long-term company survival. Be sure to keep expertise in house, Sheffi said, through continuity of pay, taking care of families, and allowing for part time work.
Disruption is also an opportunity for tough business decisions, like a long-desired reorganization or cutting non-performing products and customers. “A crisis is a terrible thing to waste,” Sheffi said.
More supply chain coverage
Related Articles
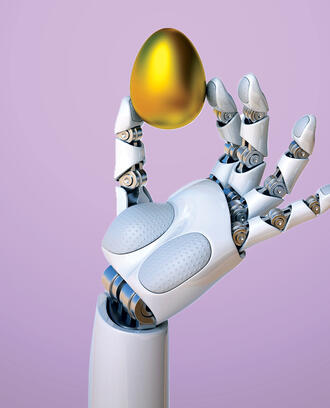
What's Planergy?
Modern Spend Management and Accounts Payable software.
Helping organizations spend smarter and more efficiently by automating purchasing and invoice processing.
We saved more than $1 million on our spend in the first year and just recently identified an opportunity to save about $10,000 every month on recurring expenses with Planergy.
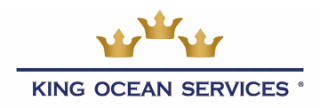
Cristian Maradiaga
Download a free copy of "indirect spend guide", to learn:.
- Where the best opportunities for savings are in indirect spend.
- How to gain visibility and control of your indirect spend.
- How to report and analyze indirect spend to identify savings opportunities.
- How strategic sourcing, cost management, and cost avoidance strategies can be applied to indirect spend.
Supply Chain Decisions: Skills and Best Practices
- Written by Lyle Del Vecchio
- 18 min read
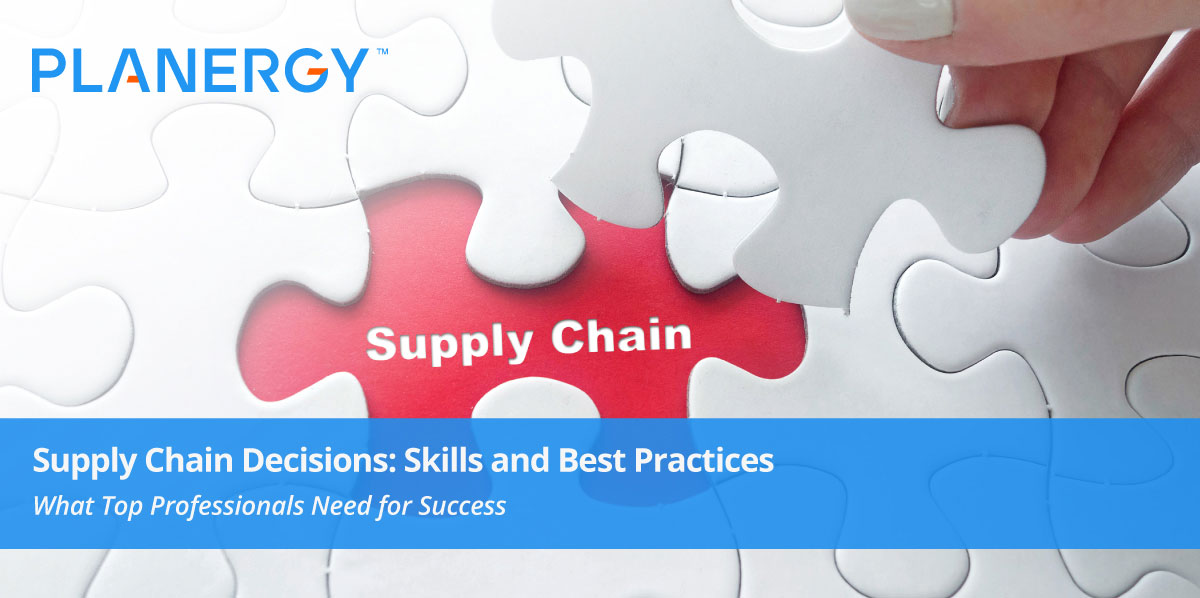
The supply management decision-making process is complex. It involves many people across multiple teams. As companies seek people to look over supply chain management (SCM), they look for people with effective decision-making skills. This is even more important when it comes to managing a global supply chain.
Decision-making is important at all levels of the supply chain, so we’ll look at what those levels are, the importance of strong and effective decision-making at the strategic level, the skills you need, and the methodology you can use to make critical decisions efficiently.
Levels of Supply Chain Management Decisions
When it comes to supply chain management, there are three levels of operation.
The strategic level is the top level of supply chain management. Here, they are responsible for the long-term decisions and laying the groundwork for the entire process. Example decisions made at this level include deciding the products or services that the company will offer. It involves things like keeping track of customer feedback and current market trends.
The tactical level of supply chain management involves the short-term and medium-term decisions throughout the supply chain. The strategic level addresses the big picture and general decisions. This level starts defining the specific supply chain processes. This is an area where manufacturing processes are designed to ensure that your company can maintain a high-quality product or service for the lowest possible cost.
Operational
At the operational level, most of the work takes place. It’s the day-to-day actions, decisions, and planning that keep the supply chain moving. Many times, organizations fail to consider the strategic and tactical levels when making decisions at the operational level.
The Importance of Strategic Supply Chain Decision Making
Supply chain managers have to make difficult decisions, often fast, using real-time information. As such, it’s critical to have problem-solving skills that you can apply whenever you run into issues with your supply chain. That small manufacturing issue can grow into a much bigger problem if your business doesn’t have effective procedures in place.
It’s not just efficient and effective decision-making that matters. Companies today need to focus efforts on ethical sourcing , not just saving money wherever possible. Today’s consumers want to know that companies are doing their part to protect the environment and the people in it. And since brand reputation influences where people spend their money , it can make or break your brand.
Solid decision-making skills in supply chain management aren’t just about challenges in logistics and manufacturing. Changes in consumer perception and customer demand can also create issues with operation. A single viral social media post could spur a spike in demand for a product. As a supply chain manager, you have to determine how you can shift production schedules and rearrange your supply chain to meet the new demand. The same can be said if a viral social media post has the opposite effect, causing a deep drop in demand.
Critical Skills for Supply Chain Professionals
There are several key decision-making skills that any sooner supply chain professional should have to be successful. We include a list of 13 to help guide you along the decision-making process as a key stakeholder.
Identify Problems
The most successful supply chain pros spot potential problems before they become an issue. Because it’s not always possible to see every problem ahead of time, you need to also be able to spot problems as they happen, so you can quickly find and implement fixes.

Develop and Communicate Solutions
In addition to being able to develop solutions for problems that come up, you need to be able to effectively communicate any changes in supply chain operations to everyone involved. That could be informing and educating your team members about changes to the process, or communicating with outside suppliers in transportation, manufacturing, or warehousing. An aptitude for clear communication is essential.
Identify Trends and Opportunities
go to the dynamic nature of supply chains, you must keep your decision-making process and your leadership dynamic as well. Instead of waiting for challenging situations to present themselves, monitor Trends in Supply chain management to keep yourself up-to-date with current best practices. If you can find Opportunities to improve operations while creating plans to take advantage of those opportunities, your team can behave proactively which is always better than responding reactively.
Leverage Data and Technology
Data is your best friend. When you base your decision-making process on solid data, you’ll obviously be better equipped to make better choices, which gives you a competitive advantage . Staying aware of the latest software Innovations helps improve job performance and ensures that your supply chain runs like a well-oiled machine is always a good thing.
Source and Generate Data
Of course, if you don’t have good data, to begin with, you won’t be able to leverage it to your advantage. That’s why having a strong data collection and analysis system in place is also important. Use automation to collect data from inventory management systems across multiple distributions centers. Collect customer order data, raw materials order volume, etc.
Having the most accurate and current information is absolutely necessary for the problem-solving process, as it helps with forecasting and process optimization. It also ensures that you are able to effectively allocate your team resources in ways that will help you accomplish your goals.
Incorporate Regulatory and Legal Considerations
Many factors outside your operation, and many outside of your control, will affect your supply chain. Part of your job as a top professional is to keep yourself aware of both potential and actual changes to the regulatory and legal framework within each function of your supply chain. Your long-term goal must account for any potential and actual changes in regulations and laws so that your operations can adapt to them accordingly.
Get Ideas from Team Members and Initiate Actions
When used correctly, your team is a vital asset to your decision-making process. Gathering ideas for your team and then taking those ideas and turning them into actionable plans goes a long way to getting all team members on board with any operational changes. This is a high-level skill that your colleagues will appreciate.
Facilitate Collaboration from Outside Elements
All your internal team members are valuable, they aren’t the only piece of the puzzle. Your effective communication skills should go beyond your internal team and extends to collaborating with the filament service providers, manufacturers, freight carriers, and any other external element in your supply chain. People at all stages of the supply chain can be resources to help you with solving your problems and implementing your decision. Take advantage of your experience with your third-party partners to create a stronger, more robust, supply chain for your business.
Recognize Relative Importance and Prioritize
Unfortunately, supply chain management isn’t an area where you can focus on solving one problem at a time. Often, you’ll have more problems than you have time to solve. That’s why it’s so essential for you to have experience end determining the relative importance of all of your priorities. To be effective and successful, you have to assign a relative value to various competing factors. That requires expertise to juggle everything and a complex supply chain.
Flexibility
The most successful supply chain managers are those who can think on their feet. Quick-thinking is essential when problems come up because it may be the only way to avoid interruptions that cost time and money. Unpredictability is part of what makes your job exciting and challenging. The better you are at making decisions at the spur of the moment, the better you can use your staff efforts while also reaching your organizational goals.
Use Past Experience to Guide Future Decisions
Taking time to really assess performance looking at both your failures and your successes, helps to ensure that you have better-informed decisions in the future. It is after all the key advantage of experience. The better you’re able to draw from your past experience, the better you will be able to serve your team.
To prevent similar issues from coming up again, track your problems at every level of the supply chain including those that you can fix at the moment. The more data you track, the more metrics you can measure and assess as you go.
Know When to Adjust Course
Discernment can make or break you. You should always be willing to stand by a decision when you feel it’s the right one, even when others disagree with you. But, you should also be willing to recognize when you’ve made the wrong choice and be willing to take action to change course if it becomes necessary.
Build Contingencies
Has anything in life ever come to you in the way you expected? We often view success as a straight line, when in reality, it’s full of curves, and even some setbacks. Disruption is a fact that we cannot avoid, so it’s essential to account for the unknown. Every decision you make needs to include a backup plan in case a change in circumstances renders your original plan useless.
Strategic decisions are crucial in procurement, but any decision may need to be changed as circumstances change.
Decision-Making Frameworks and Tools
as you practice the skills we’ve listed, you can also use decision-making strategies and tools to help you weigh the pros and cons of each situation that you may find yourself in. These tools are designed to help you create processes for effective decision-making that you can apply in any applicable situation.
Rational Decision-Making Model
This is a simple 7-step process:
- Identify the problem or opportunity
- Identity possible solutions
- Conduct a gap analysis
- Gather data and explore alternative solutions
- Analyze the possible outcomes
- Choose the best solution for the situation at hand
- Put your plan into action
This works best when dealing with advanced problems so that you can consider all options and ramifications.
Pareto Analysis
This is based on the Pareto principle which basically states that 20% of your clientele accounts for 80% of your profit. With a Pareto analysis , you apply the 80/20 rule to decision-making. This approach makes it easy for you to separate your important influences from the noise.
If you find that multiple factors have created a problem in the manufacturing sector of your supply chain, quantify the amount that each factor contributes to the issue. You’re most likely to find that 20% of the factors cause 80% of the problem. As a result, you can clarify your decision-making process so that you are focusing on the most important factors first.
SWOT Analysis
SWOT stands for strengths, weaknesses, opportunities, and threats. this analysis helps you to see where your strengths and weaknesses are, along with opportunities that may be worth pursuing, and threats you may come across along the way.
Create a chart with two columns and two rows. In the first square, list your company’s strengths. In the second, list weaknesses. On the bottom, list your opportunities and then the threats. Putting these factors down in a simple format allows you to quickly see pitfalls and opportunities that will help guide your problem-solving process.
Decision Tree
The decision tree is another visual mapping tool for decision-making. It can be helpful when it comes to predicting outcomes and weighing the pros and cons.
Right the situation on the top of a piece of paper. Draw branches to represent the factors that relate to the situation and the effects they caused. Each branch may lead to additional branches that represent other factors, decision points, or consequences. The results of your decision tree can help you see which path may be better to take.
PEST Analysis
In a PEST analysis, you’re looking at the political, economic, social, and technology factors that may influence your supply chain. This is a good visual tool to help you with decision-making because most Supply chains involve numerous external partners and cross multiple geopolitical borders. This tool is especially helpful when it comes to setting your long-term goals.
Experience is the world’s greatest resource, but the right tools can set you apart from the rest.
What’s your goal today?
1. use planergy to manage purchasing and accounts payable.
- Read our case studies, client success stories, and testimonials.
- Visit our “Solutions” page to see the areas of your business we can help improve to see if we’re a good fit for each other.
- Learn about us, and our long history of helping companies just like yours.
2. Download our guide “Indirect Spend Guide”
Download a free copy of our guide to better manage and make savings on your indirect spend. You’ll also be subscribed to our email newsletter and notified about new articles or if have something interesting to share.
3. Learn best practices for purchasing, finance, and more
Browse hundreds of articles , containing an amazing number of useful tools, techniques, and best practices. Many readers tell us they would have paid consultants for the advice in these articles.
Related Posts
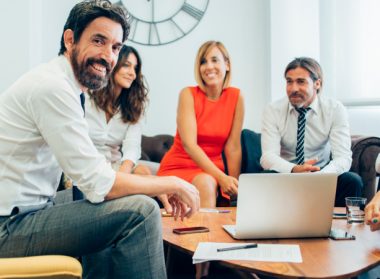
- Spend Management
Catalog Management in Procurement: What Is It, Types of Catalogs, Challenges and Best Practices To Manage Them
- 17 min read
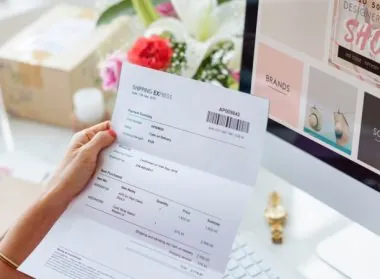
Discretionary Expenses: What Are They, Examples, and How To Control Them In Business
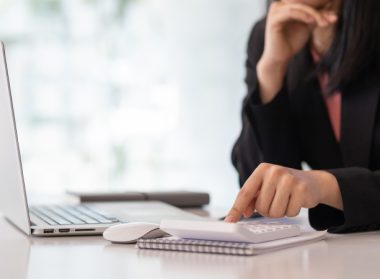
Procurement Methods: How To Source and Evaluate The Best Suppliers To Work With
- 16 min read
PROCUREMENT
- Purchasing Software
- Purchase Order Software
- Procurement Solutions
- Procure-to-Pay Software
- E-Procurement Software
- PO System For Small Business
- Spend Analysis Software
- Vendor Management Software
- Inventory Management Software
AP & FINANCE
- Accounts Payable Software
- AP Automation Software
- Compliance Management Software
- Business Budgeting Software
- Workflow Automation Software
- Integrations
- Reseller Partner Program
Business is Our Business
Stay up-to-date with news sent straight to your inbox
Sign up with your email to receive updates from our blog
This website uses cookies
We use cookies to personalise content and ads, to provide social media features and to analyse our traffic. We also share information about your use of our site with our social media, advertising and analytics partners who may combine it with other information that you’ve provided to them or that they’ve collected from your use of their services.
Read our privacy statement here .
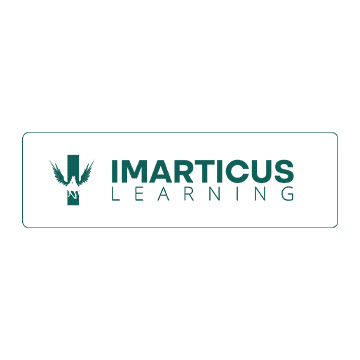
What Problems Do Strong and Efficient Supply Chains Solve?
- October 25, 2023
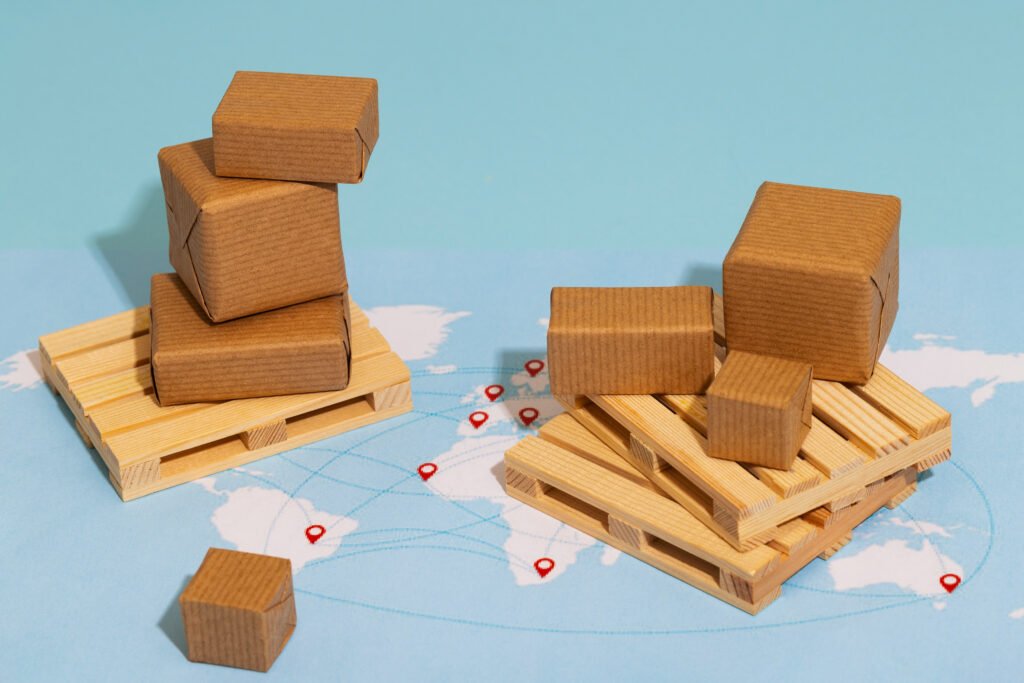
Share This Post
Supply chain management is the crux of today's globalised and interconnected commercial industry. It is the pillar behind the seamless availability of products and services.
Supply chains are not just mere logistics procedures; they tackle various problem-solving mechanisms. Supply chains are an indispensable tool for consumers and businesses alike.
In this blog, we will address the various problems supply chains face and how they are solved quickly and efficiently by a robust SCM system. If you want to establish a career in supply chain management , keep reading to learn how these logistics marvels navigate complex challenges and ensure stellar business operations.
What is Supply Chain Efficiency?
One should comprehensively understand supply chain efficiency to excel in supply chain management. Supply chain efficiency is not only known for its supremacy in cost efficiency or achieving customer satisfaction; it also helps gain a competitive edge in the global market.
The supply chain streamlines various procedures, enabling minimal delays, reducing excess inventory and eliminating bottlenecks. Adopting an accurate forecasting method alongside investment in advanced technology is essential for efficient supply chain management. To pursue excellence, businesses should consider that supply chain efficiency is not about cost-cutting and enhanced values. It involves continual improvements and a proactive approach to problem-solving.
To understand supply chain efficiency, a supply chain management course is ideal for upcoming professionals eyeing the role of supply chain managers.
Importance of Supply Chain Efficiency
Supply chain efficiency plays a vital role in the sustainability and success of organisations across various industries. The reasons for their importance in the global marketplace are listed below:
- Cost efficiency: Efficient supply chains minimise operational costs via streamlining through optimised transportation and reduced inventory holdings.
- Customer satisfaction: With supply chain efficiency, consistent customer satisfaction has become feasible because of consistent product availability
- Risk mitigation: Efficient supply chain management promotes resilience against any disaster, integral to risk mitigation.
- Global expansion: Supply chain efficiency promotes global expansion as it enters and adapts easily to different geographical and cultural landscapes.
Problems Solved by Supply Chains
An efficient supply chain is always up for solving any problem that might arise shortly or in the present. Here are some issues supply chains face and how they could be mitigated.
1. Material Shortage
In 2022, McKinsey and Company considered material shortage as one of the significant challenges of the global supply chain. It also specified how these have disrupted the overall supply chain efficiency and faced more disruptions than in 2020-2021.
Methods to Overcome the Problem: Supply and Demand Change Executive has specified that around 57% of the disruption would be solved if the manufacturing procedure is diversified. It should include strategies like supply chain automation, efficient supplier collaboration and focus on inventory management.
2. Lack of Supply Chain Visibility
Supply chain visibility is pinpointing and tracking logistics movement, be it raw materials or other counterparts. High visibility is the pinnacle of efficient company operations and seamless business. During the pandemic, supply chain visibility was in shambles, hampering the overall distribution procedure.
Methods to Overcome the Problem: To increase supply chain visibility, analyse the current pain points. Remedy these areas adhering to the company's goals and objectives. Eliminate any form of siloed technology and implement a robust supply chain management system.
3. Demand Forecasting Complexity
The capacity to effectively predict consumer demand and anticipate future requirements is crucial to effective supply chain management. Creating good customer relationship management and ensuring corporate profitability and growth is critical. Some approaches organisations use for demand forecasting include exponential smoothing, moving average forecasting, auto-regressive integrated moving averages, bottom-up forecasting, and multiple aggregation prediction algorithms.
Methods to Overcome the Problem: One of the integral methods to overcome these problems are:
- Providing clean and reliable data.
- Having an actionable input towards the affected stakeholders.
- Imposing robust analytics.
- Building strong collaborations with other supply chain partners.
4. Supply Chain Fragmentation
Fragmentation occurs when the supply chain is dispersed among various suppliers and manufacturers. While this may provide some pricing or quality advantages, controlling the supply chain may be difficult. The pandemic once again demonstrated how unstable the fractured supply chain can be when manufacturing is closed in one country or borders are blocked altogether, prohibiting the transportation of required parts.
Methods to Overcome the Problem: Improved data management is the most effective strategy to address the problems caused by supply chain fragmentation. Remove isolated systems that are unable to communicate with one another. Actively capture disruptions to the supply chain and assess their potential impact on the business.
Congestion at Critical Ports
Congestion at crucial ports can be induced by circumstances other than those seen during the pandemic. The reasons are:
- Outdated and insufficient equipment.
- Labour strikes.
- Insufficient transmodal capabilities.
Methods to Overcome the Problem: Increasing supply chain visibility and extending time leads would exponentially help overcome these problems. Investigation into proper ports can also help mitigate congestion.
Increased Freight Costs
Transport and freight costs are also affected by the epidemic, global social upheavals, and rising inflation. Fuel prices have soared, affecting all modes of transportation by land, sea, and air.
Methods to Overcome the Problem: Consolidating shipments on time alongside searching for suppliers within geographical proximity is one of the best mitigation procedures. Furthermore, imposing dual sourcing is another efficient way to decrease freight costs.
Digital Transformation and Integration
Improved digital technology is required to gather, analyse, and integrate high-quality, up-to-date data. This data can assist the automation and forecasting technologies required for today's supply chain management.
Methods to Overcome the Problem: Perform a supply chain audit. Evaluate present circumstances and prioritise requirements. Investigate potential technologies that satisfy the requirements. Request product demonstrations to witness the technology in action. Establish a team of implementation representatives from all affected parties.
Conclusion
Strong and effective supply chains are crucial in dealing with critical organisational concerns. They address issues like inventory management, fluctuating demand, and cost optimisation, eventually improving competitiveness and customer satisfaction.
If you are looking for an efficient supply chain course , check out Imarticus Learning's Professional Certification in Supply Chain Management and Analytics . This supply chain course has a campus immersion programme and helps you understand the new age of supply chain management.
To know more, check out the website right away!
Subscribe To Our Newsletter
Get updates and learn from the best, more to explore.
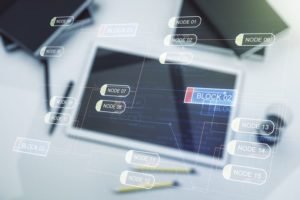
Your data analytics course might come with a Job Interview but does it offer these things?
Your data analyst training course is incomplete without these features, our programs.
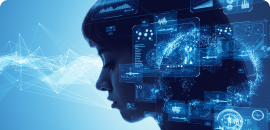
Postgraduate Program In Machine Learning And Artificial Intelligence
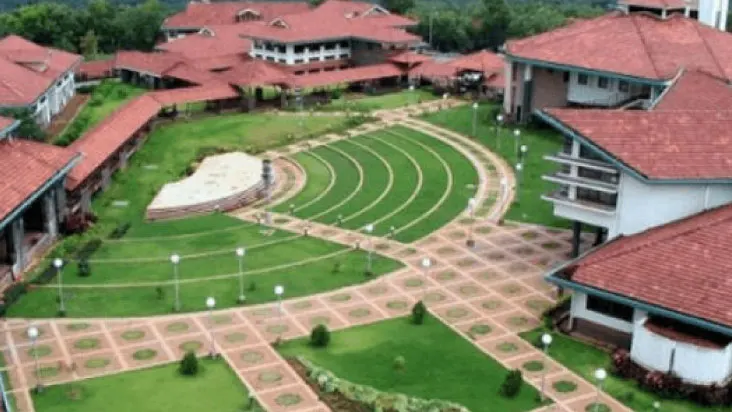
Keep In Touch
Advertisement
Editorial: Smart and sustainable supply chain and logistics - trends, challenges, methods and best practices
- Published: 07 April 2023
- Volume 324 , pages 1–11, ( 2023 )
Cite this article
- Paulina Golinska-Dawson 1 ,
- Beata Mrugalska 1 ,
- Kin Keung Lai 2 &
- Gerhard-Wilhelm Weber 1 , 3
2224 Accesses
Explore all metrics
Avoid common mistakes on your manuscript.
The COVID-19 pandemic has created a lot of disturbances in supply chains around the globe leading to disturbances in the availability of logistics infrastructure (e.g., ports closure, boarders’ control, etc.) and workforce absence. Companies have decided to digitalize their logistics processes and business operations in order to establish the resilience to changing market conditions and enable increased agility and higher performance. The increasing digitalization of the processes in logistics and the need for more integrated and seamless cooperation in logistics, supply chain, inventory and production management currently belong to the dominant trends in the business world. Moreover, the pressure for CO2 emissions reduction and more resource-efficient business and waste management models strongly influence the organization of logistics operations on both a local and global scale. The integration of physical and cyber systems is necessary in order to achieve more environmentally friendly, efficient, safe logistics, supply chain, inventory and production operations
The continuously expanding pools of managerial data and the sets of environmental and technical constraints have triggered the development of new mathematical models that ought to be the foundations of most advanced simulation and decision making techniques that are just what the business and economic areas of logistics, supply chain, inventory and production management urgently require. All of these emerging problems are facing the high obstacle of uncertainty that has become the striking characteristic of the many items included in the operations aforementioned, at every stage and every moment. Here, we also mention stochastic disruption and regime switching. All the smart processes of learning, improvement, optimization and control under uncertainty are core purposes of modern operations research, data mining, analytics, machine learning, and artificial intelligence (AI) that will be discussed, used and refined in this special issue.
This special issue covers a wide range of topics related to logistics, supply chain management and related areas where advanced operational research (OR) and management science (MS) methods, theories, and methods are used and further developed. The scope of the special issue study includes the following areas, methodologies and challenges: logistics, supply chain management (SCM), inventory management (IM), and production management (PM). We wish to provide a short overview of the contents of this special volume.
1 Sustainability in logistics and supply management (SiLSSM) studies included the following topics
Circular economy and closed-loop supply chain .
The Circular Economy (CE) concept encourages the redesign of industrial activities and social practices to decouple economic growth from negative environmental impacts. The emphasis is on creating more resource-efficient supply chain that enable reduction, reuse and recycling, thus supporting the transition to a zero-waste economy. Closing the loop for materials flows in a supply chain is challenging due to the high uncertainty, thus the new modelling and optimization approach contribute to more efficient decision making.
Ishizaka et al. in the article “Supplier selection in closed loop pharma supply chain: a novel BWM–GAIA framework” employ a three-stage research method to define a hierarchical structure of criteria for evaluating supplier performance using the best-best method (BWM). Additionally, they apply a geometric analysis plane for interactive assistance (GAIA) on the BWM results.
Bakhshi and Heydari in the paper “An optimal put option contract for a reverse supply chain: case of remanufacturing capacity uncertainty” propose a decentralized and centralized decision making model, which helps a remanufacturer to deal with uncertainty in two echelon supply chain.
Huang et al. in the article “Supplier – remanufacturing and manufacturer – remanufacturing in a closed-loop supply chain with remanufacturing cost disruption” apply Stackelberg game to compare supplier–remanufacturing and manufacturer–remanufacturing with respect to equilibrium strategies and profits, under different disruptions.
Zhang and Zhang in the paper “Optimal pricing and greening decisions in a supply chain when considering market segmentation” study the optimal pricing and the remanufactured product’s greening decisions in a supply chain with one manufacturer and one retailer. They apply Stackelberg games for three remanufacturing systems, (centralized, decentralized manufacturer, and decentralized retailer-remanufacturing) to demonstrate the conditions under which the manufacturer or retailer should engage in remanufacturing. They consider traditional and green consumers to find the optimal solution.
Ke et al. in their work “Pricing new and remanufactured products under patent protection and government intervention” consider a three-period closed-loop supply chain model framework. They investigate the basic model in which companies determine prices to maximize profit according to consumers’ strategic behavior and green preference. Furthermore, they extend the model and investigate the impact of patent protection and government intervention on company’s operational strategies, profitability, and consumer surplus.
Reverse logistics and waste management .
From the managerial perspective Reverse Logistics (RL) includes the planning, implementing, and controlling the flow of materials, and finished goods from the point of production, distribution, or use to the point of recovery or proper disposal. Designing and managing an appropriate reverse logistics network is challenging, as often the reverse flows are distributed and thus not cost-efficient.
Egri et al. in the work “Robust facility location in reverse logistics” study a facility location problem with the collection and transportation of wood to designated processing facilities. They develop mathematical models to achieve the economy of scale. A novel approach with bilevel optimization is used to compute the exact solutions of the robust problem in smaller instances. A local search and a tabu search method are used to solve problems of realistic size.
Tirkolaee et al. in the paper “A novel model for sustainable waste collection arc routing problem: Pareto-based algorithms” develop a novel mixed integer linear programming (MILP) model to formulate the sustainable periodic capacitated arc routing problem (PCARP) for municipal waste management (MSW). Their solution allows for simultaneously minimizing the total cost, workload deviation, and total environmental emission, They design a novel hybrid multi-objective optimization algorithm, with simulated annealing algorithm (MOSA) and multi-objective invasive weed optimization algorithm (MOIWOA).
Hosseini-Motlagh et al. in the paper “Reverse supply chain management with dual channel and collection disruptions: supply chain coordination and game theory approaches” study the effect of collection competition between the collector channel and the remanufacturer channel on the acquisition prices offered to consumers as incentive schemes for returning used products. They search for an equilibrium for the sales prices of remanufactured products, the acquisition prices, and the transfer price in the settings of decentralization, centralization, and coordination.
Carbon footprint management, low carbon supply chain design, and optimization .
In recent years, policies and regulations with focus to reduce carbon emissions worldwide (e.g., adoption of the Paris Agreements in 2015) have changed the gravity of the decision making in supply chain management. Carbon regulatory mechanisms can take different forms, such as: Carbon cap policy (CCP), Carbon tax policy (CTP), Carbon cap-and-trade, policy (CCTP), and Carbon offset policy (COP). The carbon footprint measures in a cumulative way the total amount of carbon dioxide emissions that are directly and indirectly created by operations and processes throughout the product’s life cycle. The need to include the aspect related to the carbon footprint in the design and management of logistics operations creates a demand for new methods and tools. The carbon footprint in a supply chain can be reduced by applying more sustainable modes of transportation transport, related routing decisions, but also by redefining the design of whole supply chains (low carbon design, low carbon routing, etc.).
Ali et al. in the article “Developing a hybrid evaluation approach for the low carbon performance on sustainable manufacturing environment” explore the enablers of green sustainable practices of procurement, logistics, product and process design, and regulatory frameworks for reducing the carbon footprint.
Das et al. in the paper “Multi-objective solid transportation-location problem with variable carbon emission in inventory management: a hybrid approach” propose a new heuristic with alternating locate-allocate heuristic and the intuitionistic fuzzy programming to get the Pareto-optimal solution.
He et al. in two papers “To pool or not to pool in carbon quotas: analyses of emission regulation and operations in supply chain supernetwork under cap-and-trade policy” and “Differential game theoretic analysis of the dynamic emission abatement in low-carbon supply chains” apply game models, and study the impact of different carbon regulatory mechanism on a supply chain performance and carbon dioxide reduction.
Homayouni et al. in the article “A robust-heuristic optimization approach to a green supply chain design with consideration of assorted vehicle types and carbon policies under uncertainty” apply the multi-choice goal programming model to study sustainability strategies for carbon regulations mechanisms. They propose a novel robust-heuristic optimization approach which support the supply chain managers in decision-making in selecting of carbon emission policies in supply chains with different vehicle types, demand and economic uncertainty in large scale-problems.
Li and Lai in the paper “The abatement contract for low-carbon demand in supply chain with single and multiple abatement mechanism under asymmetric information” propose a novel principal-agent model to reduce carbon emissions through improved manufacturer’s abatement efficiency through more accurate information about demand and customer’s preferences.
Sustainability assessment and its impact on sustainable supply design .
Sustainability practices in a supply chain are predominantly investigated through the triple bottom line (TBL) framework, which distinguishes three dimensions of sustainability, such as: economic, environmental, and social. To implement and monitor a more sustainable performance, companies need to define a set of performance measures, which provide decision-makers with a transparent, and a good understanding about what happens in a supply chain at present, and to direct them towards optimal future actions.
Ali et al. in the article “Evaluating sustainability initiatives in warehouse for measuring sustainability performance: an emerging economy perspective” model a case study from Saudi Arabia to rank the sustainable practices in the warehousing. This three-phase study applies the contingency theory and triple bottom line approach to investigate sustainable practices of warehousing with fuzzy Delphi and the Best Worst Method.
Fulzele and Shankar in their work on “Performance measurement of sustainable freight transportation: a consensus model and FERA approach” propose an integrated approach to develop a performance index that supports decision making in a supply chain. They innovatively combine the Consensus Model (CM) for assessing the degree of importance of Key Performance Indicators (KPIs) with the Fuzzy Evidential Reasoning Algorithm (FERA) for the aggregation of subjective judgments with crisp quantitative values.
Jauhari et al. in their paper on “Sustainable inventory management with hybrid production system and investment to reduce defects” analyze a vendor which performs a regular production and a green production. They propose a model for cost reduction, which allows them to find the optimal shipment quantity, production allocation, number of shipments, safety factor, defective rate, and production.
Moreno-Camacho et al. in their paper “Sustainable supply chain network design: a study of the Colombian dairy sector” propose mixed-objective linear programming model with four decisions and three sustainable criteria. The proposed model supports decision making in food sector by determining the optimal location and capacity of the processing and distribution facility and mode of transportation to comply with environmental and social rules without neglecting economic performance.
Tao et al. in their paper “Optimal channel structure for a green supply chain with consumer green-awareness demand” analyze four different settings: a manufacturer’s dual-channel supply chain, a retailer’s dual-channel supply chain, a manufacturer-online and retailer-offline (hybrid I) structure, and a manufacturer-offline and retailer-online (hybrid II) structure. They assess the of impact of consumers’ green awareness and shopping habits (online or offline) on the level of green technology, profits, and retail prices.
Koppiahraj et al. in the article “Optimal sustainability assessment method selection: a practitioner perspective” evaluate ten sustainability assessment (SA) methods, and 20 critical factors of sustainable manufacturing (SM). They apply a fuzzy MULTIMOORA (Multi-Objective Optimization on the basis of a Ratio Analysis plus the full multiplicative form) to rank SA methods with the weights of the critical factors of SM practice obtained using a fuzzy analytic hierarchy process (AHP).
Ciardiello et al . in the paper “A game-theoretic multi-stakeholder model for cost allocation in urban consolidation centres” design mechanisms that support the economic and financial sustainability of UCC systems. They consider the problems of responsibility and cost allocation among stakeholders of a sustainable urban freight network. Applying the Shapley Value concept, they study the economic viability under different scenarios, including the outsourcing of the last-mile deliveries.
Kwon et al. in their work on “Dynamic interplay of environmental sustainability and corporate reputation: a combined parametric and nonparametric approach” propose a novel PROCESS-Neural network to explore the holistic effect of environmental sustainability and corporate reputation on the performance of a company.
Green mobility and green routing .
Despite advancements in battery technology, the range anxiety of electric vehicles (EVs) remains a major obstacle to their adoption in logistics operations. The need to frequently recharge the battery adds complexity to the operational planning when dispatching last-mile vehicles. The energy consumption of electric vehicles may vary depending on various factors, for example ambient temperature, weight, speed, and road conditions.
Aghalari et al. in the work “ Electric vehicles fast charger location-routing problem under ambient temperature” propose two innovative heuristics with the two-phase Tabu Search-modified Clarke and Wright algorithm and the Sweep-based Iterative Greedy Adaptive Large Neighborhood algorithm. Their approach supports decision making on the design of DC fast charging stations for EVs in cities with high temperature fluctuations.
Rastani and Çatay in their paper “A large neighborhood search-based matheuristic for the load-dependent electric vehicle routing problem with time windows” take into account the role of the weight of a cargo in energy consumption and related routing decisions for a fleet of EVs. They propose a matheuristic approach that integrates an optimal repair procedure into the large neighborhood search method.
Tirkolaee et al. in their work on “A novel two-echelon hierarchical location-allocation-routing optimization for green energy-efficient logistics systems” aim to minimize the total cost (shipping, environmental pollution, travelling, vehicle usage, and fuel consumption) with Grey Wolf Optimization (GWO) and Particle Swarm Optimization (PSO) algorithms.
Sustainable humanitarian logistics operations .
Today, logistics is one of the most important instruments for disaster relief. Natural disasters cause devastating effects, and major problems with supplying commodities such as food, medicine, etc. Logistics planning is an essential component in addressing the initial needs immediately after any disaster. Planning and coordination of transportation and distribution of emergency supplies in a resource efficient way is a challenge. Research is needed on methods and tools for logistics operation planning, optimization of location of the key points in the logistics network for supply storage, and coordination mechanisms of the teams involved in the relief operations.
Eligüzel et al . in the paper “Location-allocation analysis of humanitarian distribution plans: a case of United Nations Humanitarian Response Depots” apply three different location-allocation models to analyze the current distribution plan in the UNHRD distribution network, including maximum coverage, P-median, and set covering. The focus is placed on the maximization of the number of covered people, and reductions in total distance travelled, time, and costs.
Ergün et al. in their article “A game theoretical approach to emergency logistics planning in natural disasters” analyze the case of Turkey, where a significant part of the population lives in the earthquake-prone areas. They apply a cooperative game theoretical model for emergency logistic planning with a flow problem to support decision making on the maximization of the transferred commodity.
2 Recent advances in operational research, data mining, analytics, machine learning, and AI in development of logistics network and strategies
Smart technologies .
The dynamic development of information technology has promoted the digital transformation of supply chains and logistics operations. Stakeholders can collect, store, and analyze data to enable achieving improved performance due to better coordination and reduction of uncertainties resulting from information asymmetry.
Ben-Daya et al. in the paper “Optimal pricing in the presence of IoT investment and quality-dependent demand” propose a model based on the Stackelberg game to analyze the impact of the Internet of Things (IoT) on the retailer and distributor performance. They use the model to justify the investment in IoT and to decide where to deploy IoT technologies in the supply chain.
Liu et al. in the article “The influence of leadership and smart level on the strategy choice of the smart logistics platform: a perspective of collaborative innovation participation” consider a two-tier supply chain with value-added service innovation. They apply a game model consisting of a smart logistics platform and a smart logistics provider. They study the strategic choice of the platform about whether to collaborate with the provider in order to co-innovate depending on the leadership and smart level.
Seddigh et al. in their work “Approaching towards sustainable supply chain under the spotlight of business intelligence” develop a theoretical model to explain how business intelligence capabilities influence the company’s supply chain sustainability. Through an empirical survey in the Iranian pharmaceutical industry, they investigate the relationships between business intelligence and sustainability dimensions in supply chains.
Wang et al. in the paper “Decision optimization in service supply chain: the impact of demand and supply-driven data value and altruistic behavior” develop five analytical models with two service providers (SPs) and one service integrator (SI). They discuss the paradox and effects which appear in data-driven supply chain under different settings and find an “optimal purchasing area” which allows us to obtain higher-level value-added service at a lower price.
Design of logistics network and supply chain coordination .
The modelling and optimization of the logistics network play crucial role in achieving cost-efficient and competitive supply chains. The uncertainty which is inherent in the economic environment make companies search for new methods and tools which allows them to establish the robustness and resilience in supply chains.
Amin-Tahmasbi et al. in the paper “A multi-objective integrated optimisation model for facility location and order allocation problem in a two-level supply chain network” design a mixed-integer multi-objective integrated mathematical model for a cost-efficient dynamic decision-making within a multi-period time horizon. They explore the concept of factoryless production to find the optimal replenishment number of production facilities by the multi-objective functions (minimisation of the total cost, rejected and late delivery units, and maximisation of the assessment score of suppliers). For solving large-scale instances, they apply the Multi-Objective Particle Swarm Optimisation (MOPSO) and Multi-Objective Vibration Damping Optimisation (MOVDO) heuristic.
Chatterjee in the paper “Multivariate supplier selection for asymmetric specification region: using price and quality” designs the multivariate process capability index (MPCI) based approach with the conventional phase wise hypothesis testing procedure. The multivariate capability-price comparison (MCPC) chart is used for graphical presentation. The proposed approach contribute to the theory by handling simultaneously quality and price constraints in decision making on the supplier selection.
Gerami et al. in the work on “A novel network DEA-R model for evaluating hospital services supply chain performance” propose the model to overcome the underestimation of efficiency and pseudo-inefficiency scores in logistics management. They extend the network data envelopment analysis (NDEA) model with the ratio data (NDEA-R) to evaluate the performance with the given internal structure of a supply chain, relationships among different divisions of an SC with two assumptions of free-links and fixed-links. The results are provided from the testing of the new model in a supply chain of 19 hospitals in Iran over six months.
Panchal et al. in the paper “Supply chain network redesign problem for major beverage organization in ASEAN region” analyze multi-echelon supply chains under future economic integration. The authors apply case-based modeling to design the network with minimum gross cost while considering the impacts of barriers to resource accessibility and external economic decisions on infrastructure. A developed mixed-integer linear programming model explores location and capacity selection for factories, warehouses, suppliers and transportation, to achieve the optimal flow of products in the network.
Pourmohammadi et al. in their work “Solving a hub location-routing problem with a queue system under social responsibility by a fuzzy meta-heuristic algorithm” aim to minimize the total transportation cost and to maximize the employment, regional development, and social responsibility. They apply the queuing system to estimate the waiting time at hub nodes and maximize the responsiveness, and a fuzzy queuing to model the uncertainties. For problem solving, they develop a new evolutionary meta-heuristic algorithm based on fuzzy invasive weed optimization, variable neighborhood search, and game theory.
Ribeiro and Barbosa-Póvoa in the paper “A responsiveness metric for the design and planning of resilient supply chains” develop an optimization model, to maximize economic and responsiveness objectives. They analyze a case study where supply chain managers in decision-making avoid adopting universal strategies and search for the best plan for their SC operations, including the impact on customers.
Hosseini-Motlagh et al. in their paper on “Recall management in pharmaceutical industry through supply chain coordination” provide a real life case study and investigate the impacts of production disruption, recall of defective products, and decentralization among the members on the performance of multi-echelon pharmaceutical SC. They propose an altered revenue sharing contract to support decision making on channels coordination in a supply chain in order to mitigate risks.
Kashav et al. in the paper “Ranking the strategies to overcome the barriers of the maritime supply chain (MSC) of containerized freight under fuzzy environment” provide an effective, and structured framework for policy making. Their framework applies the FAHP (Fuzzy Analytical Hierarchy Process) for evaluating weights and ranking the identified barriers, then the Fuzzy TOPSIS (Technique for Order of Preference by Similarity to Ideal Solution) technique is used to facilitate the ranking of the strategies to overcome these barriers.
Development of strategies for supply chain .
The growing competition on procurement and sales markets, the increasing complexity, and dynamics of business environment, combined with the rapid development of information and communications technology, and pressure for more cooperation in logistics networks lead companies to seek new methods and tools that support decision making at the strategic level in a supply chain.
Laguir et al. in the article “Performance effects of analytics capability, disruption orientation, and resilience in the supply chain under environmental uncertainty” based on a survey of 405 respondents, test hypotheses on the links between Analytics Capability of an Organization (ACO), Supply Chain Disruption Orientation (SCDO), and Supply Chain Resilience (SCR) to enable operational performance in case of environmental uncertainty.
Li et al. in the paper “The optimal advertising strategy with differentiated targeted effect consumers” develop four mutually exclusive models for two retailers, which advertise their goods to customers and engage in Nash game to carry out price competition and then in Stackelberg game to carry out advertising strategy competition under two different game sequences.
Özmen et al. in the article “Robust multivariate adaptive regression splines under cross-polytope uncertainty: an application in a natural gas market” investigate the parametric uncertainties in future scenarios. They expand the multivariate adaptive regression splines (MARS), through the usage of robust optimization techniques. To cope with complexity of the underlying model, they apply so-called weak robustification to exploit a geometrical and combinatorial approach by formulating Robust MARS (RMARS) under cross-polytope uncertainty.
Shakouhi et al. in their work “A competitive pharmaceutical supply chain under the marketing mix strategies and product life cycle with a fuzzy stochastic demand” investigate the Nash and Stackelberg games. They consider two supply chains with exclusive retailer and manufacturer under different levels of price, quality, access, and promotion (i.e., marketing mix) across different stages of product life cycles.
Waqas et al. in the paper “Influence of supply chain risk management and its mediating role on supply chain performance: perspectives from an agri-fresh produce” present the results of the survey among 430 fresh fruit and vegetable agropreneurs in Malaysia. They apply SmartPLS 3.0, which uses partial least squares structural equation modelling (PLS-SEM), to test the correlation between supply chain risks and supply chain performance, investigate the mediating effect of supply chain risk management on the correlation between supply chain risks and supply chain performance. Furthermore, they evaluate the moderating role that knowledge management plays between supply chain risks and supply chain risk management.
Yun et al. in their work “Contract design under asymmetric demand information for sustainable supply chain practices” apply a game-theoretic model with the most crucial factors in market entry stage, such as market uncertainty, competition, contract design, distribution channel, and sustainability. They investigate a supply chain consisting of one supplier and two retailers (an incumbent and an entrant). They analyze how the supplier optimally designs the contract for the retailers under asymmetric information to make the supply chain more efficient and sustainable. They consider the preference between a franchise contract (FC) and a two-part tariff contract (TTC), from the perspectives of the supplier, the incumbent retailer, and the whole supply chain.
Modelling, simulation, and optimization of production and logistics operations .
Before some reasonable decision making can be done in any field of broader logistics, including production, the available data have to be carefully arranged, processed, and analyzed. In fact, not seldom do new data have to be found or even made, with all the needed and, if possible, optimal statistical design. The resulting models, e.g., in terms of clustering, regression, or classification, have to be evaluated and compared based on their statistical performance criteria. Nowadays, more AI-based methods of ANNs and SVMs have joined the more classic methods, which are based on mathematics and leading to their corresponding models. Eventually, models become part of and reflected by optimization problems and their methods, not least as heuristics of various kinds. When decision making has been made, the quality of the results is tested, especially by fine sensitivity analyses and eventually simulations. During these efforts, the role of the data and of the modeling are never forgotten; rather sometimes the decision maker along with his or her team has to return to them with new measurements and further preparations to improve the overall results.
Ketkov et al. in the paper “Planning of life-depleting preventive maintenance activities with replacements” develop a general repair-replacement problem with an infinite time horizon. They search for an optimal number of periodic maintenance (PM) and the optimal time interval between them. They discuss global optimization techniques for problem solving under assumptions on the reward and lifetime depletion rates.
Dovramadjiev and Mrugalska in the paper “Real-time planning and monitoring of the steel pipes towards life cycle sustainability management” propose how to design products in a computer environment in accordance with sustainability concept. They show calculations of environmental impact of their models. The knowledge of such data as carbon footprint, energy consumption, air acidification, and water eutrophication allows the management of a life cycle of the exemplary products.
Pitakaso et al. in the article “A novel variable neighborhood strategy adaptive search for SALBP-2 problem with a limit on the number of machine’s types” propose a new method for assembly line balancing with a limitation of multi-skilled employees. By applying the artificial intelligence methods, they aim to minimize the cycle time while considering the limited number of types of machines in a particular workstation.
Shao et al. in their work “A multi-period inventory routing problem with procurement decisions: a case in China” propose a novel mixed linear programming model for MIRP-PD to minimize the total cost of procurement, inventory holding, and transportation. Furthermore. They propose a hybrid two-level heuristic (with tabu search and adaptive threshold acceptance) to solve problems with large-scale instances.
Acknowledgements
We hope that the selected topics well display a core selection of international research coping with the emerging and complex problems of Smart and Sustainable Supply Chain and Logistics-Trends, Challenges, Methods and Best Practices by the results and methods of Operational Research. We thank the Annals of Operations Research ( ANOR ) and the publishing house of Springer for the honor of hosting this special volume. In particular we would like to express our gratitude to Editor-in-Chief of ANOR, Prof. Dr. Endre Boros , for his interest, confidence and support spent on our special volume from the very first moment of the project, to Publications Manager, Ms. Ann Pulido , for her guidance and support.
We thank all the authors and reviewers, for their efforts and willingness to share their expertise with the research community. We hope that the papers presented in this special volume will stimulate further research and cooperation in industry and academia.
Author information
Authors and affiliations.
Faculty of Engineering Management, Poznan University of Technology, 2 J. Rychlewskiego str, Poznan, 60-965, Poland
Paulina Golinska-Dawson, Beata Mrugalska & Gerhard-Wilhelm Weber
Department of Industrial and Manufacturing Systems Engineering, Hong Kong University, Pok Fu Lam, Hong Kong
Kin Keung Lai
IAM, METU, Ankara, Turkey
Gerhard-Wilhelm Weber
You can also search for this author in PubMed Google Scholar
Corresponding author
Correspondence to Beata Mrugalska .
Additional information
Publisher’s note.
Springer Nature remains neutral with regard to jurisdictional claims in published maps and institutional affiliations.
Rights and permissions
Reprints and permissions
About this article
Golinska-Dawson, P., Mrugalska, B., Lai, K.K. et al. Editorial: Smart and sustainable supply chain and logistics - trends, challenges, methods and best practices. Ann Oper Res 324 , 1–11 (2023). https://doi.org/10.1007/s10479-023-05304-7
Download citation
Published : 07 April 2023
Issue Date : May 2023
DOI : https://doi.org/10.1007/s10479-023-05304-7
Share this article
Anyone you share the following link with will be able to read this content:
Sorry, a shareable link is not currently available for this article.
Provided by the Springer Nature SharedIt content-sharing initiative
- Find a journal
- Publish with us
- Track your research

IMAGES
VIDEO
COMMENTS
The narrower meaning of supply chain optimization focuses on a mathematical problem-solving method. Also called supply chain network optimization , this is a quantitative approach for finding the best combination of facilities, warehouses, the flows between them, production resource allocation, and other elements under specific constraints.
In conclusion, conducting a problem-solving session is a vital component of effective supply chain management. By understanding the importance of problem-solving, preparing for the session, leveraging effective communication and problem-solving techniques, and implementing agreed-upon solutions, organizations can drive efficiency, streamline ...
A structured problem-solving method helps manage this complexity. You can't fix what you don't understand, but if you know the causes and how those causes relate to one another, you'll be better able to solve the problem and hedge against future risks - no matter where they present in the chain. Procurement Software.
In this chapter we describe some common elements shared by all scheduling problems, introduce some basic concepts related to computational tractability of a problem, and summarize several commonly used solution methods for solving supply chain scheduling problems. These solution methods include dynamic programming, branch-and-bound, integer ...
1 Define the problem. The first step in problem-solving is to define the problem clearly and accurately. This means you need to understand the nature, scope, and impact of the problem, as well as ...
This article describes three frameworks for problem solving that can help supply chain professionals to think more creatively and solve problems more effectively: maneuver warfare, design thinking, and. the Theory of Inventive Problem Solving (TRIZ). Each of these frameworks enable supply chain professionals to approach a challenge from ...
When tackling an SCM problem, there are many problem solving methods available depending on the nature, scope, and complexity of the issue. For instance, the 5 Whys is a simple technique that ...
Problem Solving & Continuous Improvement. Lean techniques can be used to solve problems that happen on site, such as damaged materials, late deliveries, and not meeting schedule deadlines by investigating the root causes and involving everyone relevant and then putting fixes in place. A Lean approach to problem solving normally involves the use ...
SUPPLY CHAIN COLLABORATION is a hot topic today—and no wonder: ... with regular joint reviews and problem-solving sessions to address trade-offs. The real power of any performance-management system comes from this frequent, robust dialogue between partners, yet this is also the element most commonly ignored or underemphasized by collaborating ...
Despite meticulous planning, unexpected challenges can arise at any stage, impacting the entire chain. Efficient problem-solving is not just about fixing issues when they arise; it is also about proactive thinking to anticipate and prevent potential disruptions. Some key reasons why effective problem-solving is essential in the supply chain ...
3 The Lean Process Thinker If it is all about process, we should know what a process is. So what is a process? It could be: >> A sequence of activities. >> A series of steps to reach a desired outcome. >> The means of getting something done. >> The method for getting from point A to point B. >> A series of defined steps to arrive at a desired outcome. A process is a systematic series of ...
Manage and Drive Down Costs in the Supply Chain. Rising fuel, commodity and labor costs can drive up charges for organizations throughout the supply chain that ultimately get passed on to the end business. Supply chain managers need to understand and control cost challenges. Visibility of Costs Through Accurate Budget Control and Reporting.
Problem identification techniques are methods or tools that help SCM practitioners to diagnose and define problems in their supply chains. Some of the most effective problem identification ...
The rational decision-making model. In 2007, researchers at the University of Lund in Sweden applied a modified version of the rational decision-making process to a supply chain management case study. The steps of the rational decision-making model are: Identify the problem or opportunity. Identify potential solutions.
Essential problem-solving techniques for supply chain leaders include root cause analysis, the 5 Whys technique, brainstorming and mind mapping, and SWOT analysis. Additionally, leveraging data analytics, supply chain management software, and artificial intelligence and machine learning can improve decision-making abilities.
Previously, supply chain managers may have been able to take a functional or silo-oriented approach to managing the confines of the supply chain function. With the advent of longer supply chains and hypercompetitive markets, a firm's managers must now utilize higher levels of problem solving ability when making supply chain management decisions.
Other things to know include each plant's operational status and inventory level. All of this requires supply chain visibility. As suppliers feel pressure, look out for quality degradation and late deliveries. Fakes are also a big problem when supplies are scarce, Sheffi said, as companies look for alternative suppliers.
In this, Part 1 of our white paper series on the building blocks of supply planning solutions, we've examined the role of the solvers. Solvers, the underlying method that translates business objectives into calculated outcomes, fall into two categories: mathematical optimisation and heuristics. Whether you choose one or the other or a hybrid ...
The Importance of Strategic Supply Chain Decision Making. Supply chain managers have to make difficult decisions, often fast, using real-time information. As such, it's critical to have problem-solving skills that you can apply whenever you run into issues with your supply chain.
Start with three basics: Get your methods - the systems and processes that help drive your company - modernized and managed. Keep team morale top of mind, and if you're not already, start engaging your teams for collaborative problem solving on supply chain or any other issues impacting the company. Keep your message on point.
It involves continual improvements and a proactive approach to problem-solving. To understand supply chain efficiency, ... Methods to Overcome the Problem: Supply and Demand Change Executive has specified that around 57% of the disruption would be solved if the manufacturing procedure is diversified. It should include strategies like supply ...
The continuously expanding pools of managerial data and the sets of environmental and technical constraints have triggered the development of new mathematical models that ought to be the foundations of most advanced simulation and decision making techniques that are just what the business and economic areas of logistics, supply chain, inventory and production management urgently require.
The Cause and Effect Diagram is a versatile tool that can be used in various problem-solving and improvement initiatives, including quality management, process improvement, root cause analysis, and project management. It encourages collaboration, brainstorming, and structured analysis, enabling teams to gain deeper insights into complex ...