The Business of Fashion
Agenda-setting intelligence, analysis and advice for the global fashion community.

News & Analysis
- Professional Exclusives
- The News in Brief
- Sustainability
- Direct-to-Consumer
- Global Markets
- Fashion Week
- Workplace & Talent
- Entrepreneurship
- Financial Markets
- Newsletters
- Case Studies
- Masterclasses
- Special Editions
- The State of Fashion
- Read Careers Advice
- BoF Professional
- BoF Careers
- BoF Insights
- Our Journalism
- Work With Us
- Read daily fashion news
- Download special reports
- Sign up for essential email briefings
- Follow topics of interest
- Receive event invitations
- Create job alerts
Case Study | Inside Nike’s Radical Direct-to-Consumer Strategy

- Chantal Fernandez
In October 2020, in the middle of a global pandemic that had infected 188 countries, causing record sales damage across the retail sector, Nike’s share price hit an all-time high.
Like other retailers, Nike had been forced to close most of its network of more than 900 stores across the world, as had its key wholesale partners like Nordstrom and Foot Locker.
But the American sportswear giant’s performance during the pandemic, when its online sales spiked, signalled to many that Nike had the competency to prosper long term, in a future that will be increasingly defined by e-commerce and digital brand connections.
It was a validation of a strategy that Nike prioritised three years ago, dubbing it “Consumer Direct Offense,” but the seeds of the approach go back almost a decade.
ADVERTISEMENT
Above all, Nike is a marketing company. It doesn’t just sell sneakers; it sells the brand aspiration that imbues those sneakers with meaning. But to achieve the reach required to scale its business, Nike’s distribution strategy had long-relied on third-party retailers to sell its products, even if the consumer experience offered by those partners diluted its brand.
But in a future increasingly defined by e-commerce, fast-moving trends and, above all, the rising power of branding to drive consumer preference when competitors are just a click away, Nike realised that in order to thrive, it needed to take control of its distribution to better manage its brand and deepen its connection with consumers.
It was definitely architecting a new retail, and a bold, retail vision for Nike.
Such an evolution is easier said than done, especially for a business as large as Nike in a category as competitive as sportswear. But by radically cutting back on its wholesale distribution and raising the bar for brand experience with the third-party partners that remained; expanding its focus on content, community and customisation to keep customers close; investing in its data analytics and logistics capabilities; and rethinking the role of the store as a brand stage, Nike drove a veritable direct-to-consumer revolution.
When the pandemic hit, these shifts went into overdrive.
“It was definitely architecting a new retail, and a bold, retail vision for Nike,” said Heidi O’Neill, Nike’s president of consumer and marketplace, and one of the most prominent executives leading the brand’s new strategy in recent years. “But it started with our consumer, and we knew that consumers wanted a more direct relationship with us today.”
In this case study, BoF breaks down Nike’s pioneering direct-to consumer strategy and how it has worked to the brand’s advantage, propelling its share price to new heights during the global crisis of 2020.
Click below to read the case study now.
- Mark Parker
- John Donahoe
- direct to consumer
- athletic apparel
© 2024 The Business of Fashion. All rights reserved. For more information read our Terms & Conditions

Shein Steps Up London IPO Preparations Amid US Hurdles to Listing
The online fashion retailer plans to update China’s securities regulator on the change of the initial public offering venue and file with the London Stock Exchange as soon as this month, a person with knowledge of the matter said.

Op-Ed | How Macy’s Can Repel the Barbarians at Its Gate
The company, under siege from Arkhouse Management Co. and Brigade Capital Management, doesn’t need the activists when it can be its own, writes Andrea Felsted.
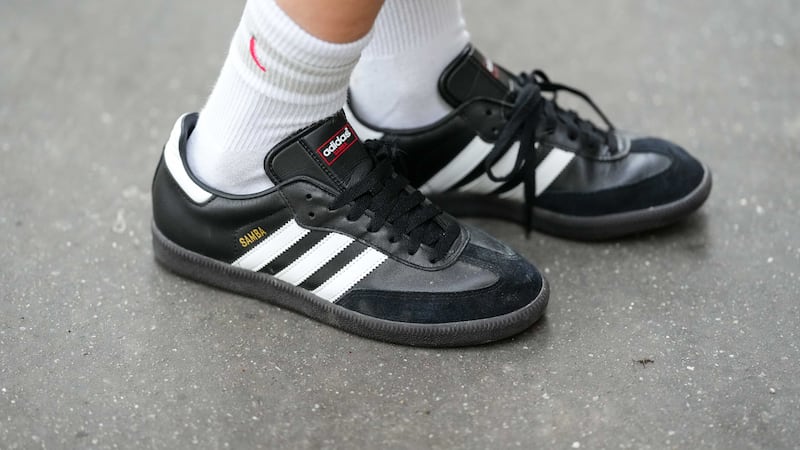
Adidas Prepares for Samba Slump
As the German sportswear giant taps surging demand for its Samba and Gazelle sneakers, it’s also taking steps to spread its bets ahead of peak interest.
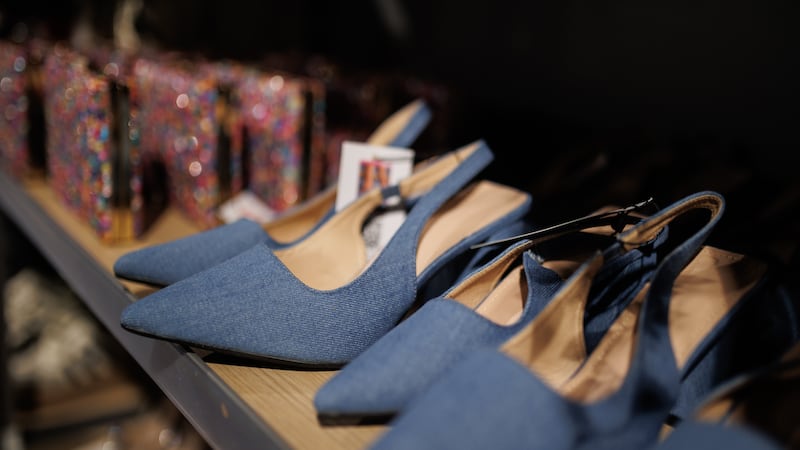
Op-Ed | The Rise of the Unwasteful Brand
A profitable, multi-trillion dollar fashion industry populated with brands that generate minimal economic and environmental waste is within our reach, argues Lawrence Lenihan.
Subscribe to the BoF Daily Digest
The essential daily round-up of fashion news, analysis, and breaking news alerts.
Our newsletters may include 3rd-party advertising, by subscribing you agree to the Terms and Conditions & Privacy Policy .
Our Products
- BoF Insights Opens in new window
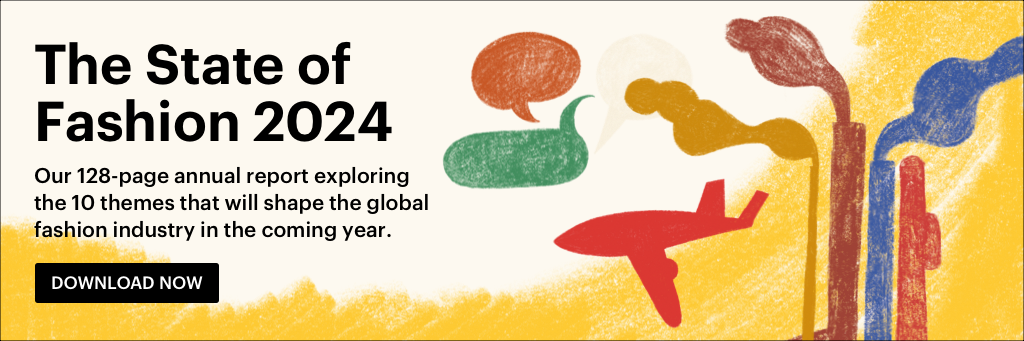
Brought to you by:

By: Frank T. Rothaermel
The case is set in January 2020 and the case protagonist is John Donahoe, Nike's new CEO. Nike is the largest company worldwide in the athletic footwear, apparel, and equipment business. The case…
- Length: 16 page(s)
- Publication Date: Oct 26, 2019
- Discipline: Strategy
- Product #: MH0060-PDF-ENG
What's included:
- Teaching Note
- Educator Copy
$4.95 per student
degree granting course
$8.95 per student
non-degree granting course
Get access to this material, plus much more with a free Educator Account:
- Access to world-famous HBS cases
- Up to 60% off materials for your students
- Resources for teaching online
- Tips and reviews from other Educators
Already registered? Sign in
- Student Registration
- Non-Academic Registration
- Included Materials
The case is set in January 2020 and the case protagonist is John Donahoe, Nike's new CEO. Nike is the largest company worldwide in the athletic footwear, apparel, and equipment business. The case focuses on the challenges Donahoe faces as he attempts to drive Nike to the goal of $50 billion in annual revenues by 2021. The case focuses on Nike's competition, the convergence of technology with apparel and footwear, as well as the company's corporate social responsibility issues. Donahoe has to address internal as well as external challenges. Donahoe was appointed CEO at a time when the Oregon sports and apparel company faces a number of controversies, including when Nike-sponsored athletes were caught up in scandals; the ban of Alberto Salazar, Nike's top running coach amid doping allegations; as well as continued concerns about Nike's workplace culture after an internal employee survey leaked describing the company as run by a boys club that is hostile towards women. Nike faces tough competition in all of its market, as well as along the value chain. Rapid advances in mobile technology and the development of the Internet of Things (IoT) could fundamentally change the industry. Nike is also moving further into ecommerce to offset the "Amazon effect." The fast-growing Chinese market, moreover, may provide an avenue for needed future growth.
Oct 26, 2019
Discipline:
McGraw-Hill Education
MH0060-PDF-ENG
We use cookies to understand how you use our site and to improve your experience, including personalizing content. Learn More . By continuing to use our site, you accept our use of cookies and revised Privacy Policy .

Nike Marketing Strategy: The Case Study (Just Do It)
Nike is a popular and leading shoe brand serving its customers for around more than 3 decades has an amazing story from the past. Here in this article, we will discuss the marketing strategy and a detailed case study of the popular shoe brand Nike.
Table of Contents
Nike Just do it: a hymn to daily challenges
More than forty years have passed since the first shoes with the famous mustache appeared on the market, but Nike’s success does not stop. The Oregon company continues to lead its competitors with annual sales of close to $30 billion and growth of 10% over the past five years. The brand is unstoppable, just as customers want it to be unstoppable by wearing their shoes during sports. ‘ Just do it: Nike’s motto has been the same for almost three decades, and it will remain so for a long time to come.
It perfectly represents not only Nike’s consumer community but also the company itself, simply and quickly. By the way, recently it turned out that this slogan was proposed by advertiser Dan Wieden , who was struck by the last words of a death row inmate in Utah. “Let’s do it,”
In a somewhat grotesque sense, the man had accepted his latest challenge. It was a short step from here to the famous ‘Just do it: The goal of Nike’s marketing strategy is, in fact, to make its products real allies in their consumers’ daily fitness struggles .
The principal was running and waffle
The way they came to market strongly and positively influenced Nike’s subsequent marketing strategy. The landmark, odd to say, was a waffle maker.
It all started when University of Oregon coach Bill Bowerman founded Blue Ribbon Sports with his athlete (Philip Knight). In addition to training some of the best American athletes and trading sneakers, Bill also developed an interest in running, a practice that was unpopular at the time.
He examines, he observes, he proposes: in 1966, together with a cardiologist, he publishes the book Jogging, which is today seen as the launch pad of the running craze that swept the United States in the 1970s.
The importance of creativity (and storytelling)
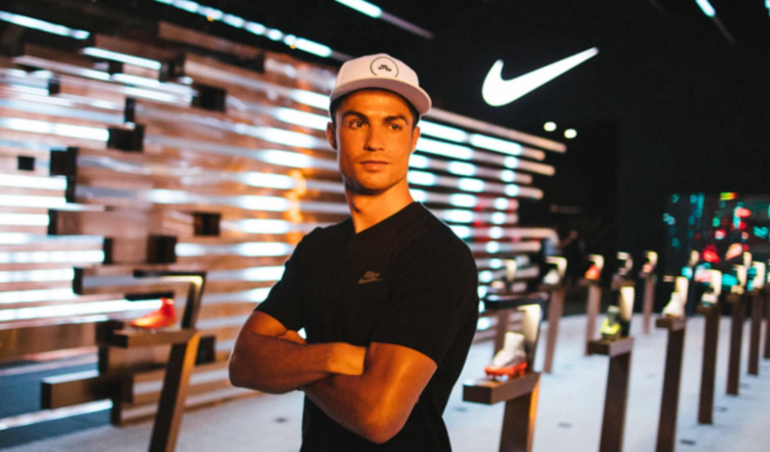
Meanwhile, relations with Onitsuka, the manufacturer of the Tigers, begin to deteriorate: Bill is convinced that thanks to his running knowledge, he can do better and design and manufacture better, lighter running shoes. to guarantee athletes the highest performance. And at this point, in the early seventies, Blue Ribbon Sports changed its name to Nike ( referring to the mythological winged personification of victory ): The company, previously a simple sneaker distributor, has thus become a manufacturing company.
History tells us that the first soles designed by Bill were made through his wife’s waffle maker: Nike’s marketing strategy does not fail to evoke this humble yet brilliant origin at times. They didn’t eat waffles at Bill’s house anymore for several months, but that little sacrifice was definitely worth the candle.
Today, his company is actually worth $71 billion
$19.7 billion brand.
Nike Moon Shoes , the first product released under the umbrella of Nike , were developed from a handmade model printed with a waffle maker . Compared to current offerings, the simplicity of these shoes disarms: however, what will be the spirit of the company is already in this first running product, for which the famous ‘mustache’ was also created. we know today.
The creator of the symbol was a design student with a salary of $35 . It’s interesting and shocking to note that today this brand is worth $10.7 billion , and without it and under another name, the company’s value would drop from its current $71 billion to $52 billion . long on the value of a good designer in the birth of a business.
Nike’s marketing strategy before marketing

Nike running shoes hit the market at the very beginning of the running era, which Bill Bowerman’s book initiated and caused, at least in part. Was it a coincidence or was it the first bold move in Nike’s successful marketing strategy? Neither, or rather a bit of both.
What we need to understand is that Bowerman did not publish this book, among other things, to sell his product, which was conceived and brought to market only years later.
No: He wrote that brochure because he really wanted to promote running and its health benefits. Of course, this wasn’t a very witty snippet of Nike’s hypothetical, newborn, or even early marketing strategy, but it could have been, nonetheless, especially given the results it brought.
By Michael Jordan and the Beatles
However, from then on, each Nike marketing strategy was deliberately and rationally designed: as early as 1973, for example, the company signed its first sponsorship contract with a tennis star, Ilie Nastase . Since then, the faces of athletes that Nike has incorporated into its products are innumerable.
First of all, we all know Michael Jordan: In 1984 the most famous basketball player became the brand’s flagship man, sponsored by ‘ Air Jordan ‘, a line of apparel and footwear for basketball that he still bills to the company. with $2 billion every year.
Air Jordan’s first promotional release

Nike even managed to use a Beatles song for a television commercial on the occasion of the 1987 Air Max release to give more power to its marketing campaign : no one from Liverpool had ever managed to brag about a song by the band. commercial. The impact of this ad was enormous: imagine the Air Max line still being produced. To date, there are more than 40 models.
Focus on customers also through social media
Jordan, Ronaldo, Ibrahimovic, McIlroy: Over the years there have been many prestige faces to Nike’s marketing strategies, as mentioned, but the core message has never changed. Even better: from the seventies to the present, the brand’s voice and identity have remained true to themselves, always putting consumers’ needs before their products.
The aesthetics of communication have changed, and the media to convey their message to has multiplied, but the brand has never betrayed itself or its customers: take a look at the official Nike pages on the social network to understand this. The way the company interfaces with Facebook or Instagram shows that its presence on those platforms isn’t driven by new and shiny business goals: no, Nike is on Instagram because their customers are there too.
And communication on these pages is not limited to an aseptic commercia l offer, it is far from it: each post is designed and created to convey something of value to the user-consumer. So, in the spirit of the company, Nike’s social updates are mostly motivational messages for their athletes – yes, Nike’s philosophy is that anyone with a body can be an athlete too. That’s why the focus of corporate branding remains on helping clients do what they love to do best, whether it’s running, playing basketball, soccer, or tennis, anytime and in any situation.
Beyond shoes: technology to be closer to the consumer
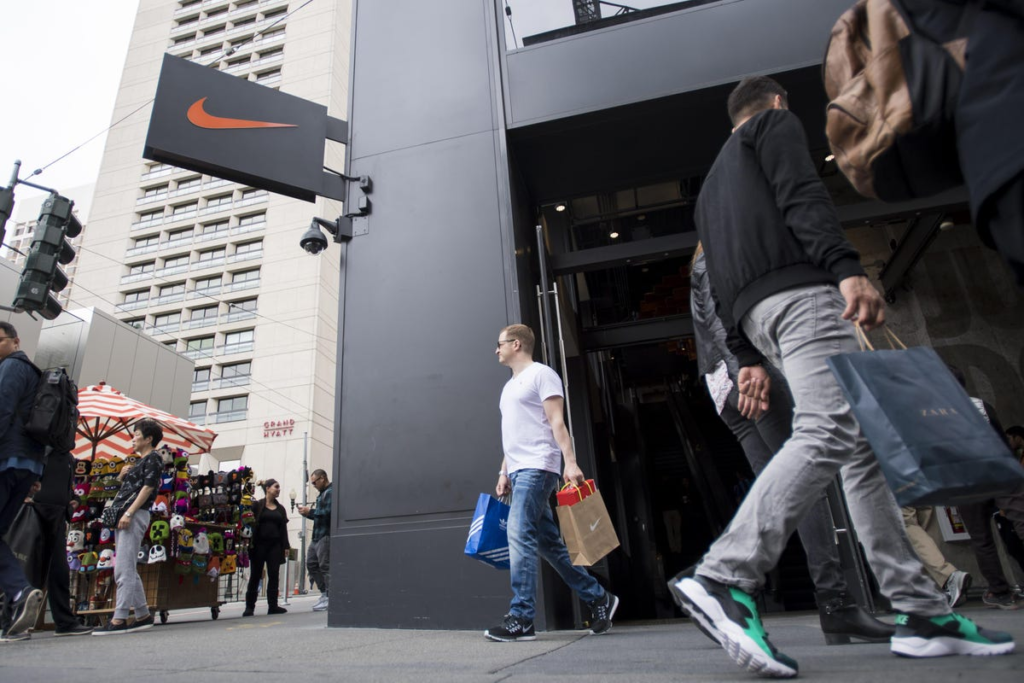
Athletes first, shoes second: this is the mantra of Nike’s marketing strategies , and it was this thinking that prompted the company to launch Nike, the first mass-produced high-tech product , in 2006. + iPod Sports Kit. It was a risky move designed to set the company firmly apart from its competitors: Once again, and more than ever in digital devices, the focus was on athletes rather than shoes. The kit allowed to measure the distance and speed of the race.
Oddly enough , yes, the product was Nike in every way, but everything was actually made by the iPod. Nike, on the other hand, was content to sell a chip to have ideas and put them in shoes, and a device for wireless connectivity.
In short, in this case, the partnership with Apple can be considered the best possible partnership. Over time, Nike+ devices have improved upgrade after upgrade, giving up first the iPod and then the chip: in 2010, everything was replaced by an iPhone ap p, and more than 6 million people are connected to a virtual community where they can analyze and share their sports. achievements.
In this way, as a complement, Nike had the opportunity to get closer to its customers, examine them closely, and communicate with them frequently. This technological lea p, which established a permanent relationship with the consumer, also made it possible to reduce advertising costs by 40% without compromising sales figures.
Nike’s goal
The final piece of Nike’s marketing strategy for a phased approach to the customer is the FuelBand bracelet , which calculates energy, and therefore – approximately – calories burned throughout the day. To make the data collected by the bracelet more reliable, Nike has created an online platform where customers can compare their energy consumption. Therefore, the athlete is in the center, the product is on the side, and the brand is always ready to motivate its consumers/athletes more.
This long-term strategy is explained above all by looking at the origins of the brand: it was born for running, not for team sports. That’s why Nike’s goal is the lone and even somewhat unruly runner who at times runs aggressively to overcome their physical and psychological limitations. The effectivenes s of this message was so effective that it persisted even as these lone athletes entered a community fueled by Nike through social media , which continues to differentiate the brand from its competitors.
Conclusion: selling shoes without selling shoes
That’s why the history of Nike’s marketing strategy teaches that in order to properly launch a product, it is necessary first and foremost to understan d what consumers need.
Once their desires are understood, a marketing campaign can be created through their products that can provide all possible solutions. For example, Nike realized that people needed a new way to stay fit, not shoes, so they offered to help them achieve this by selling shoes.
In addition, Nike’s marketing strategies teach that every consumer communication act of a company must create value, especially over the web: if you’re not solving problems, not providing real answers if you’re not helping your business. to improve the daily lives of viewers, then you inevitably have the wrong approach.
Marketing isn’t just about selling your product, or at least on the surface: Bill Bowerman didn’t start an empire by selling shoes, but by selling the art of running to customers who responded by purchasing billions of Nike Moon Shoes and by Air Max .
Other Related reads:
Electronics Giant Apple (Think different) Marketing Strategy
Puma Marketing Strategy Between Competition & Sponsorship
Red Bull Marketing Strategy: The Case Study
A go through into the marketing strategy of Starbucks
- Trackback: McDonald's marketing strategy: A benchmark in the fast food industry - Mix With Marketing
- Trackback: Adidas Marketing Strategy The Case Study (Impossible is Nothing) - Mix With Marketing
I don’t even understand how I ended up right here, however I believed this post was great. I do not realize who you’re however definitely you are going to a famous blogger if you aren’t already. Cheers!
Hey there! I’ve been reading your site for a long time now and finally got the courage to go ahead and give you a shout out from Lubbock Texas! Just wanted to tell you keep up the great work!
Leave a comment Cancel reply
Save my name, email, and website in this browser for the next time I comment.
You May Also Like
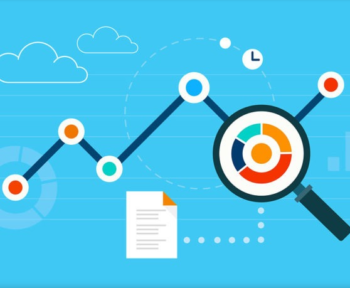
5 Examples Of Digital Marketing Strategy
What Is Marketing Automation And How Does It Work?

All You need to know about Google Analytics
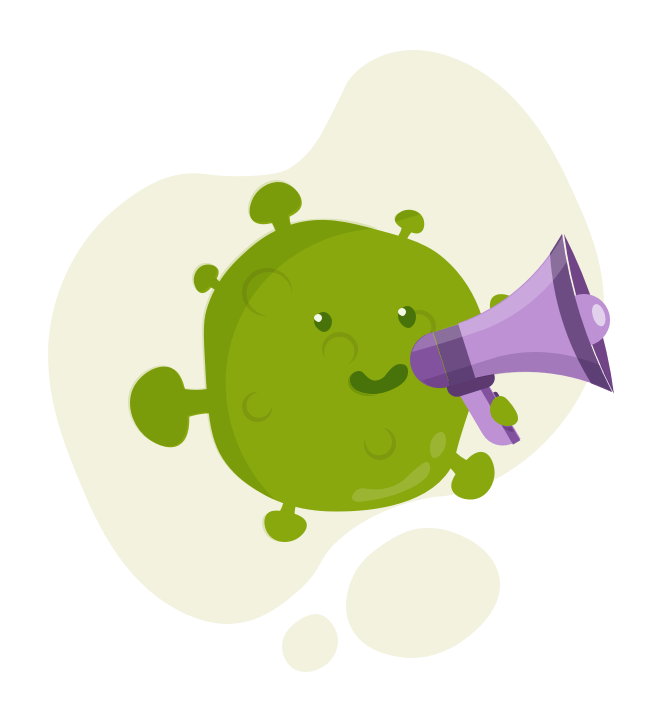
Don't miss out on this amazing opportunity - subscribe now and start enjoying all the benefits!!!
No thanks, I’m not interested!
Newsletter Subscribe
Get the Latest Posts & Articles in Your Email
We Promise Not to Send Spam:)
To read this content please select one of the options below:
Please note you do not have access to teaching notes, co‐creating value through customers' experiences: the nike case.
Strategy & Leadership
ISSN : 1087-8572
Article publication date: 5 September 2008
This case aims to demonstrate how leading firms are learning how to sustain competitive advantage by co‐creating experiences of value with customers.
Design/methodology/approach
The shoe company Nike provides a glimpse of the next “best practices” of value co‐creation with customers. By engaging with informed, connected, and networked customers around the globe, Nike has found their shared experiences to be a new source of value.
The paper finds that customers are now informed, connected, networked, and empowered on a scale as never before, thanks to search engines, engagement platforms, the growth of internet‐based interest groups, and widespread high‐bandwidth communication and social interaction technologies. Customers have learned how to use these new tools to make their opinions and ideas heard.
Practical implications
A few leading companies like Nike are involving customers in the value creation process by offering Internet sites where they can share their interactions and experiences. These range from customers' ideas about how to improve or customize products to their feelings when they use products.). For Nike, the learning from these interactions creates new strategic capital. The company can now learn directly from customers' direct input on their preferences. Nike can build relationships and trust with the Nike+ community and experiment with new offerings, all the while enhancing its brand.
Originality/value
The strategic opportunity for Nike is to build and promote the use of Internet engagement platforms through which the firm can build customer relationships on a scale and scope as never before. Effectively managing these new initiatives initially posed a new challenge for Nike, a traditionally product‐centric organization. Now their viewpoint is reversed. “In the past the product was the end point of the consumer experience. Now it is the starting point.”
- Value added
- Customer information
- Social interaction
- Consumer marketing
- Customization
Ramaswamy, V. (2008), "Co‐creating value through customers' experiences: the Nike case", Strategy & Leadership , Vol. 36 No. 5, pp. 9-14. https://doi.org/10.1108/10878570810902068
Emerald Group Publishing Limited
Copyright © 2008, Emerald Group Publishing Limited
Related articles
We’re listening — tell us what you think, something didn’t work….
Report bugs here
All feedback is valuable
Please share your general feedback
Join us on our journey
Platform update page.
Visit emeraldpublishing.com/platformupdate to discover the latest news and updates
Questions & More Information
Answers to the most commonly asked questions here
Nike: An Innovation Journey
- First Online: 29 November 2017

Cite this chapter
- Michelle Childs 5 &
- Byoungho Jin 6
Part of the book series: Palgrave Studies in Practice: Global Fashion Brand Management ((PSP:GFBM))
8285 Accesses
3 Citations
Nike is an American multinational company that has evolved to become a global leader in athletic wear with annual sales exceeding $21 billion in 2016, more than half of which is attributed to international markets. Since its inception in 1964, Nike has been an innovation leader in product development, marketing and consumer experience. Due to a dedication to continuous innovation, Nike has been able to sustain a competitive advantage within the athletic apparel and footwear marketplace. This case highlights key points in Nike’s journey of innovation and examines how Nike has successfully emerged as a global champion within the athletic wear industry. Based on these analyzed strategies, this case provides implications that are relevant for practitioners and academics.
This is a preview of subscription content, log in via an institution to check access.
Access this chapter
- Available as EPUB and PDF
- Read on any device
- Instant download
- Own it forever
- Durable hardcover edition
- Dispatched in 3 to 5 business days
- Free shipping worldwide - see info
Tax calculation will be finalised at checkout
Purchases are for personal use only
Institutional subscriptions
In 1928 in Chicago, IL, Cole Haan was established by two founders—Trafton Cole and Eddie Haan. The company focused exclusively on men’s footwear before expanding into women’s footwear in 1979 (Shoemetro, 2016 ).
Bauer was founded out of Kitchener, Ontario, Canada in 1927 and was the first company to make hockey skates that had a permanent blade attached to the boot, an innovation that changed the industry (Ozanian, 2012 ).
The Jordan brand was launched in 1984 when basketball star Michael Jordan signed a contract with Nike. An outcome of this five-year, $2.5 million deal was a brand new line of shoes called Air Jordan (Footlocker, 2017 ).
With roots in beach culture, Hurley was established in Southern California in 1999 by Bob Hurley. Initially, it was known for surf-related products but eventually became a youth lifestyle brand (Transworld Survey, 2002 ).
Converse began in 1908 near Boston, MA as a rubber shoe company that specialized in galoshes. The brand expanded to sneakers and basketball shoes starting in 1920 (Converse, 2017 ).
Founded in New Haven, CT by David Beckerman in 1971, Starter first manufactured team uniforms for high schools and eventually entered into licensing agreements with professional sports teams (Reference for Business, 1995 ).
Originally founded in Wilmslow, Manchester, UK in 1920 as Humphrey Brothers Clothing, the company was later renamed Umbro in 1924. The company was one of the earliest to provide professional clubs with soccer gear (Hunt, 2009 ).
Apple. (2006). Nike and Apple team up to launch Nike+ ipod. Apple. Retrieved from https://www.apple.com/pr/library/2006/05/23Nike-and-Apple-Team-Up-to-Launch-Nike-iPod.html
Athleisure. (n.d.). In Merriam-Webster Online . Retrieved from https://www.merriam-webster.com/dictionary/athleisure
Brettman, A. (2015, May 17). US made Nike footwear a slam dunk—some day—with or without trade deal. The Oregonian . Retrieved from http://www.oregonlive.com/playbooks-profits/index.ssf/2015/05/nikes_us_footwear_ambitions_ap.html
Burns, M. J. (2016, September 9). How Under Armour and Nike have tackled wearable technology. Sports Illustrated. Retrieved from https://www.si.com/tech-media/2016/09/09/how-under-armour-and-nike-have-differed-their-approach-tech
Chung, W., & Yeaple, S. (2008). International knowledge sourcing: Evidence from US firms expanding abroad. Strategic Management Journal, 29 (11), 1207–1224.
Article Google Scholar
Click, C. (2013, July 8). 20 Sneakers that changed performance footwear forever. Complex. Retrieved from http://www.complex.com/sneakers/2013/07/sneakers-that-changed-performance-footwear-forever
Converse. (2017). Our story. Retrieved from http://www.converse.com/uk/en/our-story/about-us.html
Diercksmeier, B. (2011). Nike Golf celebrates 20 years of NikeFIT. NGN . Retrieved from http://ngnation.com/2011/02/23/nike-golf-celebrates-20-years-nikefit/
Euromonitor. (2016, March 18). Sportswear in the US. Passport by Euromonitor. Retrieved from http://www.portal.euromonitor.com
Footlocker. (2017). The History of Air Jordan. Retrieved from http://www.footlocker.com/_-_/keyword-history+of+air+jordan
Garfield, L. (2016, June 28). Under Armour’s new innovation lab features robots that make sneakers—take an inside look. Business Insider . Retrieved from http://www.businessinsider.com/under-armours-new-innovation-lab-features-robots-that-make-sneakers-and-we-went-inside-2016-6
Germano, S. (2014, August 20). Yoga poseurs: Athletic gear soars, outpacing sport itself. Retrieved from http://www.wsj.com/articles/yoga-poseurs-athletic-apparel-moves-out-of-the-gym-to-every-day-1408561182
Gianoatasio, D. (2013). Nike’s ‘just do it’, the last great advertising slogan, turns 25. Adweek . Retrieved from http://www.adweek.com/creativity/happy-25th-birthday-nikes-just-do-it-last-great-advertising-slogan-150947/
Grill-Goodman, J. (2015, October 13). Innovation at Nike goes beyond product. Retail Info Systems . Retrieved from https://risnews.com/innovation-nike-goes-beyond-product
Hennessy, K. (2012). Fashion: The definitive history of costume and style . New York: Dorling Kindersley.
Google Scholar
Hunt, C. (2009). The Umbro story. Editorial. Retrieved from http://www.chrishunt.biz/features47.html
Interbrand. (2016). Best global brands 2016 rankings. Retrieved from http://interbrand.com/best-brands/best-global-brands/2016/ranking/
Johannessen, J.-A., Olsen, B., & Olaisen, J. (1999). Aspects of innovation theory based on knowledge-management. International Journal of Information Management, 19 (2), 121–139.
Jones, R. (2013, August 19). Know your tech: Nike Shox. Complex. Retrieved from http://www.complex.com/sneakers/2013/08/know-your-tech-nike-shox
Kell, J. (2014, December 25). Athletic apparel: Outperforming the competition in 2014. Retrieved from http://fortune.com/2014/12/25/athletic-apparel-top-performer/
Kell, J. (2016, March 19). Why Nike, Adidas are turning to celebrities in 2016. Fortune . Retrieved from http://fortune.com/2016/03/19/nike-adidas-kevin-hart-kanye/
Kim, S. (2016, April 18). Nike shoes among most counterfeit goods in the world. ABC News. Retrieved from http://abcnews.go.com/Business/nike-shoes-counterfeited-goods-world/story?id=38485256
Kish, M. (2016, June 6). Nike joins Fortune 100, 2 other Oregon companies make Fortune 500. Portland Business Journal. Retrieved from http://www.bizjournals.com/portland/blog/threads_and_laces/2016/06/nike-joins-fortune-100-2-other-oregon-companies.html
Kissane, B. (2016, January 12). New apparel and footwear research category overview: Sportswear maintains momentum. Passport by Euromonitor. Retrieved from http://www.portal.euromonitor.com
Knitting Industry. (2012, July 31). Nike Flyknit: Ready, steady, go! Retrieved from http://www.knittingindustry.com/nike-flyknit-ready-steady-go/
Kogut, B., & Zander, U. (1992). Knowledge of the firm, combinative capabilities, and the replication of technology. Organization Science, 3 (3), 383–397.
Kunde, A. (2012, October 17). Two reasons why H&M’s designer collaborations are here to stay. Passport by Euromonitor. Retrieved from http://www.portal.euromonitor.com
Longman, J. (2017, March 8). Do Nike’s new shoes give runners an unfair advantage? The New York Times. Retrieved from https://www.nytimes.com/2017/03/08/sports/nikes-vivid-shoes-and-the-gray-area-of-performance-enhancement.html?_r=0
Low, E. (2016, May 13). Why Nike has more patents than Lockheed, Ford, and Pfizer. Investors. Retrieved from http://www.investors.com/news/a-nike-apple-watch-an-under-armour-baseball-line-patents-hold-secrets/
MarketLine. (2016, August 18). Nike, Inc.: Company profile. Retrieved from MarketLine Advantage database.
McGill, D. C. (1989, July 11). Nike US bounding past Reebok. The New York Times . Retrieved from http://www.nytimes.com/1989/07/11/business/nike-is-bounding-past-reebok.html
Moore, C. M., Doherty, A. M., & Doyle, S. A. (2010). Flagship stores as a market entry method: The perspective of luxury fashion retailing. European Journal of Marketing, 44 (1/2), 139–161.
Nazario, M., & Roach, D. (2015, October 4). Nike’s incredible road to becoming the world’s dominant sneaker retailer. Business Insider. Retrieved from http://www.businessinsider.com/nike-history-timeline-2015-10
Nike. (2007, July 26). Nikeplus.com becomes world’s largest online running destination. Nike . Retrieved from http://news.nike.com/news/nikepluscom-becomes-the-world%E2%80%99s-largest-online-running-destination
Nike. (2010, November 7). Niketown London reopens. Nike . Retrieved from http://news.nike.com/news/niketown-london-reopens-as-worlds-largest-nike-store
Nike. (2012, June 21). Nike+ basketball #gameonworld. Nike. Retrieved from http://news.nike.com/news/game-on-world
Nike. (2015, March 12). The evolution of visible air. Retrieved from http://news.nike.com/news/the-evolution-of-visible-air
Nike. (2016a). Introducing the new Nike+ app. Retrieved from http://www.nike.com/us/en_us/c/nike-plus/nike-app
Nike Inc. (2016b). Nike Inc. 2016 Annual Report. Retrieved from http://investors.nike.com/investors/news-events-and-reports/?toggle=earnings
Nike. (2017a). A revolution in motion. Retrieved from http://www.nike.com/us/en_us/c/innovation/free
Nike. (2017b). About Nike: Nike explore team sport research lab. Retrieved from http://about.nike.com/pages/nike-explore-team-sport-research-lab
Nike. (2017c). Become a member and unlock more. Retrieved from http://www.nike.com/us/en_us/c/nike-plus
Nike. (2017d). Fresh air from Oregon. Retrieved from http://news.nike.com/news/nike-air-manufacturing-innovation-facility
Nike. (2017e). What is Nike Dri-FIT? Retrieved from http://help-en-us.nike.com/app/answer/a_id/204/~/what-is-nike-dri-fit
Nike Manufacturing Map. (2017). Where Nike products are made. Retrieved from http://manufacturingmap.nikeinc.com/
Nike Retail Services, Inc. (2017). About Nike Retail Services, Inc. Retrieved from http://www.vault.com/company-profiles/retail/nike-retail-services,-inc/company-overview.aspx
Ozanian, M. (2012, May 10). Bauer investors score with top hockey equipment maker. Forbes . Retrieved from https://www.forbes.com/sites/mikeozanian/2012/05/10/bauer-investors-score-with-top-hockey-equipment-maker/#321e611d437c
Piskorski, M. J., & Johnson, R. (2014). Social strategy at Nike . Brighten: Harvard Business Publishing.
Book Google Scholar
Reda, S. (2017, March 15). Nike’s SoHo flagship leads transformational charge into the future of sports retail. NRF Magazine . Retrieved from http://stores.org/2017/03/15/stay-and-play-2/?utm_source=NRFStat&utm_medium=03-21&utm_content=STORES_Nike-Flagship&utm_campaign=SmartBrief
Reference for Business. (1995). Starter Corp. company profile, information, business description, history, background information. Retrieved from http://www.referenceforbusiness.com/history2/62/Starter-Corp.html
Reference for Business. (2003). Nike, Inc. company profile, information, business description, history, background information. Retrieved from http://www.referenceforbusiness.com/history2/99/NIKE-Inc.html
Rikert, D. C., & Christensen, C. R. (1984). Nike (A) . Brighten: Harvard Business Publishing.
Roberson, G. (2016, March 10). 10 Best Nike Ads. Beloved Brands. Retrieved from http://beloved-brands.com/tag/10-best-nike-ads/
Rodionova, Z. (2016, April 19). Rolex, Rayban, Nike and Louis Vuitton among brands hit by counterfeit track worth 270bn a year. Independent . Retrieved from http://www.independent.co.uk/news/business/news/rolex-rayban-nike-and-louis-vuitton-among-brands-hit-by-counterfeit-tradeworth-270bn-a-year-a6991191.html
Salfino, C. (2017, January 23). Quest for speed and customization forces re-imagined supply chains. Vamp Footwear. Retrieved from http://vampfootwear.com/quest-speed-customization-forces-re-imagined-supply-chains/
Sharma, A. (2013, May 17). Swoosh and sustainability: Nike’s emergence as a global sustainable brand. Sustainable Brands. Retrieved from http://www.sustainablebrands.com/news_and_views/supply_chain/swoosh-and-sustainability-nikes-emergence-global-sustainable-brand
Shen, B. (2014). Sustainable fashion supply chain: Lessons from H&M. Sustainability, 6 (9), 6236–6249.
Shoemetro. (2016). A history of Cole Haan. Retrieved from http://www.shoemetro.com/t-history-of-cole-haan.aspx
Strasser, J. B., & Becklund, L. (1993). Swoosh: The unauthorized story of Nike and the men who played there . New York: Harper Collins Publisher.
Supply Chain Digest. (2016, August 23). Nike partners with private equity firm to develop new age, outsourced manufacturing and supply chain in the Americas. Retrieved from http://www.scdigest.com/ontarget/16-08-23-2.php?cid=11145
Swallow, E. (2011, September 22). How Nike outruns the social media competition. Mashable. Retrieved from http://mashable.com/2011/09/22/nike-social-media/#sa3BGLstN5q6
Townsend, M. (2012, March 15). Is Nike’s Flyknit the swoosh of the future? Bloomberg. Retrieved from https://www.bloomberg.com/news/articles/2012-03-15/is-nikes-flyknit-the-swoosh-of-the-future
Transworld Survey. (2002, Feburary 22). Bob Hurley explains why he sold his brand to Nike. Retrieved from http://www.grindtv.com/transworld-business/products/bob-hurley-explains-why-he-sold-his-brand-to-nike/#slT2f63zLEYaPHxs.97
Venkatraman, P. (2016). Fibres of sportswear. In S. G. Hayes & P. Venkatraman (Eds.), Materials and technology for sportswear and performance apparel (pp. 23–52). Boca Raton: Taylor & Francis Group, LLC.
Wasserman & Anderson. (2012). Knighting the king: The founding of Nike . Brighten: Harvard Business Publishing.
Download references
Author information
Authors and affiliations.
Department of Retail, Hospitality, and Tourism Management, The University of Tennessee, Knoxville, TN, USA
Michelle Childs
Department of Consumer, Apparel, and Retail Studies, The University of North Carolina at Greensboro, Greensboro, NC, USA
Byoungho Jin
You can also search for this author in PubMed Google Scholar
Editor information
Editors and affiliations.
University of North Carolina at Greensboro, Greensboro, North Carolina, USA
Department of Economics and Law, University of Macerata, Macerata, Italy
Elena Cedrola
Copyright information
© 2018 The Author(s)
About this chapter
Childs, M., Jin, B. (2018). Nike: An Innovation Journey. In: Jin, B., Cedrola, E. (eds) Product Innovation in the Global Fashion Industry. Palgrave Studies in Practice: Global Fashion Brand Management . Palgrave Pivot, New York. https://doi.org/10.1057/978-1-137-52349-5_4
Download citation
DOI : https://doi.org/10.1057/978-1-137-52349-5_4
Published : 29 November 2017
Publisher Name : Palgrave Pivot, New York
Print ISBN : 978-1-137-52348-8
Online ISBN : 978-1-137-52349-5
eBook Packages : Business and Management Business and Management (R0)
Share this chapter
Anyone you share the following link with will be able to read this content:
Sorry, a shareable link is not currently available for this article.
Provided by the Springer Nature SharedIt content-sharing initiative
- Publish with us
Policies and ethics
- Find a journal
- Track your research
- Artificial Intelligence
- Generative AI
- Business Operations
- Cloud Computing
- Data Center
- Data Management
- Emerging Technology
- Enterprise Applications
- IT Leadership
- Digital Transformation
- IT Strategy
- IT Management
- Diversity and Inclusion
- IT Operations
- Project Management
- Software Development
- Vendors and Providers
- Enterprise Buyer’s Guides
- United States
- Middle East
- España (Spain)
- Italia (Italy)
- Netherlands
- United Kingdom
- New Zealand
- Data Analytics & AI
- Newsletters
- Foundry Careers
- Terms of Service
- Privacy Policy
- Cookie Policy
- Copyright Notice
- Member Preferences
- About AdChoices
- Your California Privacy Rights
Our Network
- Computerworld
- Network World
Nike rebounds: How Nike recovered from its supply chain disaster

“I thought we weren’t going to talk about i2,” growls Roland Wolfram, Nike’s vice president of global operations and technology, his eyes flashing at his PR manager with ill-concealed ire.
Wolfram, who was promoted in April to vice president and general manager of the Asia-Pacific division, is all Nike. His complexion is ruddy, his lips cracked from working out or working hard, or both. He’s casually dressed, but with a typical Nike sharpness to his turtleneck and slacks, a sharpness reflected also in his urgent, aggressive defense of his company—a Nike pride that would seem arrogant were not the company so dominant in its industry.
Wolfram calls the i2 problem—a software glitch that cost Nike more than $100 million in lost sales, depressed its stock price by 20 percent, triggered a flurry of class-action lawsuits, and caused its chairman, president and CEO, Phil Knight, to lament famously, “This is what you get for $400 million, huh?”—a “speed bump.” Some speed bump. In the athletic footwear business, only Nike, with a 32 percent worldwide market share (almost double Adidas, its nearest rival) and a $20 billion market cap that’s more than the rest of the manufacturers and retailers in the industry combined, could afford to talk about $100 million like that.
It drives Wolfram crazy that while the rest of the world knows his company for its swooshbuckling marketing and its association with the world’s most famous athletes, the IT world thinks of Nike as the company that screwed up its supply chain—specifically, the i2 demand-planning engine that, in 2000, spat out orders for thousands more Air Garnett sneakers than the market had appetite for and called for thousands fewer Air Jordans than were needed.
“For the people who follow this sort of thing, we became a poster child [for failed implementations],” Wolfram says.
But there was a lesson too for people who do, in fact, follow “this sort of thing,” specifically CIOs. The lesson of Nike’s failure and subsequent rebound lies in the fact that it had a business plan that was widely understood and accepted at every level of the company. Given that, and the resiliency it afforded the company, in the end the i2 failure turned out to be, indeed, just a “speed bump.”
The i2 Failure: Tactical or Strategic?
Nike’s June 2000 problems with its i2 system reflect the double whammy typical of high-profile enterprise computing failures. First, there’s a software problem closely tied to a core business process—in this case, factory orders. Then the glitch sends a ripple through product delivery that grows into a wave crashing on the balance sheet. The wave is big enough that the company must reveal the losses at a quarterly conference call with analysts or risk the wrath of the Securities and Exchange Commission, shareholders or both. And that’s when it hits the pages of The Wall Street Journal, inspiring articles and white papers on the general subject of IT’s hubris, limitations, value and cost.
The idea that something so mundane as a computer glitch could affect the performance of a huge company is still so novel that it makes headlines. But what doesn’t usually enter the analysis is whether the problem was tactical (and fixable) or strategic (meaning the company should never have bought the software in the first place and most likely won’t ever get any value from it). The latter is a goof worthy of a poster; the former is a speed bump.
Nike claims that the problems with its i2 demand-planning software were tactical and therefore fixable. It was too slow, didn’t integrate well, had some bugs, and Nike’s planners were inadequately trained in how to use the system before it went live. Nike says all these problems were fixed by fall 2000. And the company asserts that its business wasn’t affected after that quarter. Indeed, at press time, Nike had just announced that its third-quarter 2003 profit margins were its highest ever.
If there was a strategic failure in Nike’s supply chain project, it was that Nike had bought in to software designed to crystal ball demand. Throwing a bunch of historical sales numbers into a program and waiting for a magic number to emerge from the algorithm—the basic concept behind demand-planning software—doesn’t work well anywhere, and in this case didn’t even support Nike’s business model. Nike depends upon tightly controlling the athletic footwear supply chain and getting retailers to commit to orders far in advance. There’s not much room for a crystal ball in that scenario.
Indeed, Nike confirms that it stopped using i2’s demand planner for its short- and medium-range sneaker planning (it’s still used for Nike’s small but growing apparel business) in the spring of 2001, moving those functions into its SAP ERP system, which is grounded more in orders and invoices than in predictive algorithms. “This allows us to simplify some of our integration requirements,” says Nike CIO Gordon Steele.
Wolfram says Nike’s demand-planning strategy was and continues to be a mixture of art and technology. Nike sells too many products (120,000) in too many cycles (four per year) to do things by intuition alone. “We’ve tuned our system so we do our runs against [historical models], and then people look at it to make sure it makes sense,” he says. The computer models are trusted more when the product is a reliable seller (that is, just about anything with Michael Jordan’s name on it) and the planners’ intuition plays a bigger role in new or more volatile products. In this case, says Wolfram, talking with retailers does more good than consulting the system.
“There’s been a change in the technology for demand planning,” says AMR Research Vice President Bill Swanton, who declined to address the Nike case specifically. “In the late ’90s, companies said all we need is the data and we can plan everything perfectly. Today, companies are trying to do consensus planning rather than demand planning.” That means moving away from the crystal ball and toward sharing information up and down the supply chain with customers, retailers, distributors and manufacturers. “If you can share information faster and more accurately among a lot of people, you will see trends a lot sooner, and that’s where the true value of supply chain projects are,” Swanton says.
If You Have a Game Plan, You Can Snag the Rebound
Another thing that makes Wolfram angry (his already ruddy complexion going completely red) is the widespread assumption that Nike was betting on algorithms and changed course when that didn’t work out. Wolfram says that, on the contrary, i2’s demand-planning software was never intended to be the hero of Nike’s supply chain project—one of the most ambitious ever attempted by a company its size. It was (and still is), he claims, part of a wider strategy to integrate ERP, supply chain planning and CRM software onto a single platform shared by Nike operations in North America, as well as Europe, the Middle East and Africa (EMEA). “Frankly,” he asserts, “we pretty much stayed the course.”
Nike made a bold early bet on the risky and difficult strategy of creating a single, giant, integrated database within its SAP ERP system for every employee in North America and EMEA. (Nike’s Asia-Pacific division will be on a separate instance of the software.) This meant getting everyone to agree on business practices and common data definitions before the software went in—a rarity in ERP project management.
The difficulty of integrating information across a distributed company has brought down many ERP projects, such as drugstore chain FoxMeyer’s SAP ERP system in the late ’90s and Tri-Valley Growers’ 1997 choice of Oracle’s ill-fated ERP package for the consumer packaged-good industry. Neither company ever got its systems working properly and that contributed to both eventually shutting their doors. Other companies gave up on the vision of total information integration and installed many different versions of their ERP systems—as many as 400 different versions, or instances, of a single vendor’s ERP system at some really large companies, according to AMR.
But Nike claims it has never wavered from its single-instance strategy, even when problems with the first piece of that strategy, the i2 system, hit the news on Feb. 26, 2001. The same project leaders who were in place at the time of the i2 problems (CIO Steele and the business lead, Shelley Dewey, Nike’s vice president of supply chain) are still running the project today. The reason Steele and Dewey survived was because when their system failed, they had a lifeline to hang onto: a clear business case for the overall supply chain project. If achieved, they claim it will save the company a lot more than Knight’s $400 million and the $100 million in wayward sneakers.
Nike’s supply chain project is supposed to drive the manufacturing cycle for a sneaker down from nine months to six. Cutting out that three months would match Nike’s manufacturing cycle to its retailers’ ordering schedule—they order 90 percent of their sneakers six months in advance of delivery. This means Nike could begin manufacturing its sneakers to order rather than three months in advance and then hoping they can sell them. Converting the supply chain from make-to-sell to make-to-order is the dream of any company desirous of gaining competitive advantage through its supply chain. Dell has done it, famously, with PCs; Nike wants to do it just as famously with sneakers.
Nike hasn’t gotten there yet. And its business case relies on a nearly 30-year-old model that some analysts and retailers grumble is out of touch with the reality of today’s market. But it’s a business case Nike’s leaders believe in. This is how CIOs keep their jobs when a project goes off track and it’s how they keep getting funding to keep it going.
Like many truths, this one is simple yet profound: Projects that survive breakdowns do so because everyone in the business, not just IT, understands what the system is supposed to do for the company—and sees value in it. Indeed, after his infamous conference call outburst in 2001, Knight added that, “I think it will, in the long run, be a competitive advantage.”
“We wish to God Phil [Knight] hadn’t said what he said,” says Steele with a laugh. “But his belief in this project has never wavered. [When the i2 problems emerged], we sat down and talked about what the issues were and he said, OK, I understand, carry on.” (Knight declined to be interviewed by CIO.)
How Nike Built a Robust Business Case
Knight, not normally known for self-control, has shown extraordinary patience with Nike’s supply chain project. And he’s needed it. “Once we got into this, we quickly realized that what we originally thought was going to be a two-to-three-year effort would be more like five to seven,” says Wolfram.
It’s been six years now and counting, with the final stage of the project due to be finished sometime in 2006 at a total cost that has gone from a projected $400 million to $500 million, according to Wolfram.
The theme of Nike’s sneaker supply chain is centralization. All product design, factory contracting and delivery is planned and coordinated from Beaverton, Ore. The supply chain is built around a six-month order cycle, called the “Futures” program, that was developed in 1975 in response to the then-chaotic market for running shoes. In those days, the Far East sneaker supply chain was in its infancy, deliveries were spotty, inflation was high, and runners bought whatever shoes they could find regardless of brand. Nike won that market by guaranteeing delivery and an inflation-proof discount in return for getting its orders six months in advance. Retailers went along happily because runners didn’t much care about style or looks—they wanted technically advanced shoes that fit and were in steady supply. Retailers knew their Nike shoes would sell no matter how far in advance they ordered them.
But as Nike became increasingly global, its supply chain began to fragment. By 1998, Nike had 27 order management systems around the globe, all highly customized and poorly linked to Beaverton. To gain control over its nine-month manufacturing cycle, Nike decided that it needed systems as centralized as its planning processes. ERP software, specifically SAP’s R/3 software, would be the bedrock of Nike’s strategy, with i2 supply, demand and collaboration planner software applications and Siebel’s CRM software also knitted into the overall system using middleware from STC (now SeeBeyond).
Nike’s patience was a virtue here too. It skipped AFS (Apparel and Footwear Solution), the initial version of SAP’s R/3 software developed specifically for the apparel and footwear industry. Archrival Reebok, which partnered with VF (makers of Wrangler Jeans and Vanity Fair bras, among other things) on the beta effort to develop AFS beginning in 1996, struggled for years to implement the buggy, unstable AFS software. (Reebok declined to be interviewed for this story.) And although Nike purchased AFS in 1998, it didn’t attempt to install it until SAP began working on the second, more stable version of the software. “Most of the early adopters were busy installing AFS in 1999,” says Steele with a satisfied smile. “That’s when we began spending a lot of time with SAP, sending our people over to Germany to tell them what we’d like to see in the second version.”
Why I2 Went Wrong
Unfortunately, Nike didn’t apply that same patience to the implementation of the first part of its supply chain strategy: i2’s demand and supply planner software applications. Rather than wait to deploy i2 as part of its SAP ERP project, Nike decided to install i2 beginning in 1999, while it was still using its legacy systems.
According to court documents filed by Nike and i2 shareholders in class-action suits, little went right before June 2000. i2’s predictive demand application and its supply chain planner (which maps out the manufacturing of specific products) used different business rules and stored data in different formats, making it difficult to integrate the two applications. The i2 software needed to be so heavily customized to operate with Nike’s legacy systems that it took as much as a minute for a single entry to be recorded by the software. And, overwhelmed by the tens of millions of product numbers Nike used, the system frequently crashed.
But these problems would have remained only glitches had they not spilled over into factory orders. The system ignored some orders and duplicated others. The demand planner also deleted ordering data six to eight weeks after it was entered, making it impossible for planners to recall what they had asked each factory to produce. Soon, way too many orders for Air Garnetts were going over the wires to Asian factories while calls for Air Jordans were lost or deleted.
When the problems were discovered, Nike had to develop workarounds. Data from i2’s demand predictor had to be downloaded and manually reloaded into the supply chain planner by occupying programmers, quality assurance personnel and businesspeople whenever the applications were required to share data—which was as often as weekly. Consultants were brought in to build databases to bypass portions of the i2 applications, and custom bridges were constructed to enable the i2 demand and supply planner applications to share.
Nike claims the kinks were ironed out by November 2000, but the damage was done, affecting sales and inventory deep into Nike’s next quarter. When the company’s SAP system arrived, short- and medium-range planning moved out of i2 altogether and into SAP. Nike says the $10 million i2 system was a small part of the $500 million overall project cost, although some observers assert that the i2 cost was higher.
Why did things go so wrong? Wolfram says Nike lulled itself into a false sense of security about the i2 installation because, by comparison with the SAP plan, it was a much smaller project. (Nike has about 200 planners who use the demand and supply planning systems.) “This felt like something we could do a little easier since it wasn’t changing everything else [in the business],” he says. “But it turned out it was very complicated.”
“Could we have taken more time with the rollout?” asks Steele. “Probably. Could we have done a better job with software quality? Sure. Could the planners have been better prepared to use the system before it went live? You can never train enough.”
Nike Learns Patience
Nike learned from its mistakes. There would be no rushing the SAP installation. And even though Nike executives occasionally questioned the project’s complexity and expense, Steele never considered abandoning the single-instance strategy. “We said single instance is a decision, not a discussion,” says Steele.
Nike wanted to do a staged, geographically based rollout of SAP, but it also wanted to avoid making each rollout so specific to a region that it would require specialized support. That meant building a design for the U.S. rollout that accommodated some of the peculiarities of the EMEA rollout—such as multiple currency support and different legal restrictions—even though those things were not required for doing business in the United States. This necessitated creating a global template for SAP processes, with all the regions agreeing on the minutiae of doing business. Naturally, this made each rollout longer and more complex.
Canada, a relatively small (roughly $300 million) piece of Nike’s $11 billion business, went first, on Thanksgiving weekend 2000 (the pre-spring rush quiet time), with SAP’s AFS ERP, a bundle of i2 applications and Siebel’s CRM system. Steele and regional Nike executives, dressed in smocks, served Thanksgiving dinner to project employees working around the clock. Other regions—the United States and EMEA—followed on successive Thanksgivings, putting 6,350 users worldwide on the system by the end of 2002. (The last two regions, Asia-Pacific and Latin America, are scheduled for rollout before the end of 2006, according to Nike.) Steele claims he’s never had to serve humble pie along with the turkey, saying to date there have been no disruptions to Nike’s business from the three rollouts.
This may be because of Nike’s newfound respect for training, another weakness of the i2 implementation. Nike’s U.S. customer service representatives received 140 to 180 hours of training from highly trained fellow Nike “super users,” says Andy Russell, Nike’s global transition director. Employees are locked out of the system until they complete the full training course, he says.
What Phil Knight ULTIMATELY Got for His Money
So what have six years and $500 million done for Nike’s business? Wolfram claims that better collaboration with Far East factories has reduced the amount of “pre-building” of shoes from 30 percent of Nike’s total manufacturing units to around 3 percent. The lead time for shoes, he asserts, has gone from nine months to six (in some periods of high demand, seven). But John Shanley, managing director with Wells Fargo, says, “Retailers are saying it’s still closer to nine months than six.” Gross margins have increased slightly since 2001 but not significantly.
Inventory levels have been reduced, says Supply Chain Vice President Dewey, by cutting Nike’s factory order interval time from one month to a week in some cases. But here, too, the effects may not be trickling down to the balance sheet as fast as Nike would like. Inventory levels are still at the mercy of Nike’s fickle audience of teens. Nike’s inventory turns were 4.34 per year in 2003, according to Footwear News, an industry trade magazine, slightly less than the industry average of 4.39 and behind rivals Reebok (5.07) and K-Swiss (4.47).
Nike also is behind its rivals in direct point-of-sale (POS) integration with retailers, says Shanley. Supply chain experts agree that actual data from stores, rather than software algorithms, are the best predictors of demand. But Nike’s SAP system cannot yet accept POS data, though the company says it’s working on it.
So far, the most direct benefits of the system have been typical for ERP: improved financial visibility, cash flow management, revenue forecasting, and an ability to juggle Nike’s cash stockpile in different currencies to take advantage of shifting exchange rates—benefits that are enhanced by the single database that holds all the data.
But Steele maintains that the best is yet to come. “We haven’t changed our processes too much yet,” he says, “because we didn’t want to complicate the rollouts.” Eventually, he believes Nike will get that six-month lead time down to three. But, he cautions, that that would require “significant changes on the part of our retail and supplier partners as well as Nike processes.”
He’d better hurry. Shanley says the sneaker market has changed a lot since Nike created its Futures program in the ’70s. Retailers don’t like having to order products six months in advance when fashions can change in a flash. Rivals are allowing retailers much more leeway in ordering practices, eroding Nike’s market lead in select areas.
But because Nike developed a plan in 1998, and stuck with it, the company claims it can make a coordinated global effort to cut that lead time. The system to make that happen is in place—which, given all that has transpired in the past seven years, is rather remarkable.
More on supply chain:
- What is supply chain management? Mastering logistics end to end
- How data can move the needle on supply chain
- How CIOs can help reduce supply chain anxieties
- Supply chain woes? Analytics may be the answer
Related content
Boomi burnishes api management capabilities, tiaa modernizes the customer journey with ai, 10 it skills where expertise pays the most, what is erp enterprise resource planning systems explained, from our editors straight to your inbox, show me more, colorado ai legislation further complicates compliance equation.

UK government’s Pensions Dashboards Programme delayed

Raj Polanki’s five steps by which CIOs can lead holistically

CIO Leadership Live with Sri Adusumilli, Chief Information Officer, TruckPro LLC

CIO Leadership Live NZ with Tim Partington, Director Digital & Technology, Skills Consulting Group

CIO Leadership Live UK with Charlene Hunter, MBE, CEO & Founder, Coding Black Females

A Fundamental Question: Open or Closed Source?

Sponsored Links
- Everybody's ready for AI except your data. Unlock the power of AI with Informatica
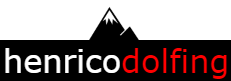
Sunday, October 16, 2022
- Labels: Case Studies , Project Failure , Project Success
Case Study 16: Nike’s 100 Million Dollar Supply Chain "Speed bump"

“This is what you get for 400 million, huh?”
Nike President and CEO Phil Knight famously raised the question in a conference call days before announcing the company would miss its third-quarter earnings by at least 28% due to a glitch in the new supply chain management software. The announcement would then send Nike’s stock down 19.8%. In addition, Dallas-based supply-chain vendor i2 Technologies, which Nike assigned blame, would suffer a 22.4% drop in stock price.
The relationship would ultimately cost Nike an estimated $100 million. Each company blamed the other for the failure, but the damage could have been dramatically reduced if realistic expectations had been set early on and a proper software implementation plan had been put in place. Most companies wouldn’t overcome such a disastrous supply chain glitch or “speed bump,” as Knight would call it, but Nike would recover due to its dominant position in the retail footwear and apparel market.
In 1999, two years before Knight’s famous outburst, Nike paid i2 $10 million to centralize its supply, demand, and collaboration planning system with a total estimated implementation cost of $40 million. Initially, i2 was the first phase of The Nike Supply Chain (NSC) project. The plan was to implement i2 to replace the existing system and introduce enterprise resource planning (ERP) software from SAP and customer relationship management (CRM) software from Siebel Systems.
The goal of the NSC project was to improve Nike’s existing 9-month product cycle and fractured supply chain. As the brand experienced rapid growth and market dominance in the 1990s, it accumulated 27 separate order management systems around the globe. Each is entirely different from the next and poorly linked to Nike’s headquarters in Beaverton, Oregon.
At the time, there wasn’t a model to follow at the scale Nike required. Competitors like Reebok struggled to find a functional supply chain solution specific to the retail footwear and apparel industry. In an effort to solidify its position as the leader in sportswear, Nike decided to move forward quickly with i2’s predictive demand application and its supply chain planner software.
"Once we got into this, we quickly realized that what we originally thought was going to be a two-to-three-year effort would be more like five to seven," - Roland Wolfram, Nike’s vice president of global operations and technology.
The NCS project would be a success, and Nike would eventually accomplish all its supply chain goals. However, the process took much longer than expected, cost the company an additional $100 million, and could have been avoided had the operators or both companies taken a different approach to implementation.
"I think it will, in the long run, be a competitive advantage." – Phil Knight
In the end, Knight was right, but there are many valuable lessons to learn from the Nike i2 failure.
If you want to make sure your business critical project is off to a great start instead of on its way on my list with project failures? Then a New Project Audit is what you are looking for. If you want to know where you are standing with that large, multi-year, strategic project? Or you think one of your key projects is in trouble? Then a Project Review is what you are looking for. If you just want to read more project failure case studies? Then have a look at the overview of all case studies I have written here .
So, before we get into the case study, let’s look at precisely what happened...
Timeline of Events
1996 - 1999
Nike experienced incredible growth during this period but was at a crossroads. Strategic endorsement deals and groundbreaking marketing campaigns gave the company a clear edge over Adidas and Reebok, its two most substantial competitors in the 80s and 90s. However, as Nike became a world-renowned athletics brand, its supply chain became more complex and challenging to manage.
Part of Nike’s strategy that separated itself from competitors was the centralized approach. Product design, factory contracting, and order fulfillment were coordinated from headquarters in Oregon. The process resulted in some of the most iconic designs and athlete partnerships in sports history. However, manufacturing was much more disoriented.
During the 1970s and 80s, Nike battled to develop and control the emerging Asian sneaker supply chain. Eventually, the brand won the market but struggled to expand because of the nine-month manufacturing cycle.
At the time, there wasn’t an established method to outsource manufacturing from Asia, making the ordering process disorganized and inefficient across the industry. In addition, Nike’s fractured order management system contained tens of millions of product numbers with different business rules and data formats. The brand needed a new way to measure consumer demand and manage purchasing orders, but the state of the legacy system would make implementing new software difficult.
At the beginning of 1999, Nike decided to implement the first stage of its NSC project with the existing system. i2 cost the company $10 million but estimated the entire project would cost upwards of $400 million. The project would be one of the most ambitious supply chain overhauls by a company of Nike’s size.
i2 Technologies is a Dallas, Texas-based software company specializing in designing solutions that simplify supply and demand chain management while maximizing efficiency and minimizing cost. Before the Nike relationship, i2 was an emerging player in logistics software with year-over-year growth. Involvement in the Nike project would position the company as the leading name in supply chain management software.
Nike’s vision for the i2 phase of NSC was “achieving greater flexibility in planning execution and delivery processes…looking for better forecasting and more profitable order fulfillment." When successfully implemented, the manufacturing cycle would be reduced from nine months the six. This would convert the supply chain to make-to-order rather than make-to-sell, an accomplishment not yet achieved in the footwear and apparel industry.
Predicting demand required inputting historical sales numbers into i2’s software. “Crystal balling” the market had substantial support at the time among SCM companies. While the belief that entering numbers into an algorithm and spitting out a magical prediction didn’t age well, the methodology required reliable, uniform data sets to function.
Nike decided to implement the “Big Bang” ERP approach when switching to i2 for the supply chain management. The method consists of going live where the business completely changes without phasing out the old system. Nike also opted for a single instance strategy for implementation. The CIO at the time, Gordon Steele, is quoted saying, “single instance is a decision, not a discussion.” Typically, global corporations choose a multi-instance ERP solution, using separate instances in various regions or for different product categories.
By June of 2000, various problems with the new system had already become apparent. According to documents filed by Nike and i2 shareholders in class-action suits, the system used different business rules and stored data in various formats, making integration difficult. In addition, the software needed customization beyond the 10-15% limit recommended by i2. Heavy customization slowed down the software. For example, entries were reportedly taking over a minute to be recorded. In addition, the SCM system frequently crashed as it struggled to handle Nike’s tens of millions of product numbers.
The issues persisted but were fixable. Unfortunately, the software was linked to core business processes, specifically factory orders, that sent a ripple effect that would result in over and under-purchasing critical products. The demand planner would also delete ordering data six to eight weeks after it was entered. As a result, planners couldn’t access purchasing orders that had been sent to factories.
Problems in the system caused far too many factory orders for the less popular shoes like the Air Garnett IIIs and not enough popular shoes like the Air Jordan to meet the market's demand. Foot Locker was forced to reduce prices for the Air Garnett to $90 instead of the projected retail price of $140 to move the product. Many shoes were also delivered late due to late production. As a result, Nike had to ship the shoes by plane at $4-$8 a pair compared to sending them across the Pacific by boat for $0.75.
November 2000
According to Nike, all the problems with i2’s supply chain management system were resolved by the fall. Once the issues were identified, Nike built manual workarounds. For example, programmers had to download data from i2’s demand predictor and reload it into the supply chain planner on a weekly basis. While the software glitches were fixed and orders weren’t being duplicated or disappearing, the damage was done. Sales for the following quarter were dramatically affected by the purchasing order errors resulting in a loss of over $100 million in sales.
Nike made the problem public on February 27, 2001. The company was forced to report quarterly earnings to stakeholders to avoid repercussions from the SEC. As a result, the stock price dove 20%, numerous class-action lawsuits were filed, and Phil Knight famously voiced his opinion on the implementation, "This is what you get for $400 million, huh?"
In the meeting, Nike told shareholders they expected profits from the quarter to decline from around $0.50 a share to about $0.35. In addition, the inventory problems would persist for the next six to nine months as the overproduced products were sold off.
As for the future of NSC, the company, including its CEO and President, expressed optimism. Knight said, "We believe that we have addressed the issues around this implementation and that over the long term, we will achieve significant financial and organizational benefit from our global supply-chain initiative."
A spokeswoman from Nike also assured stakeholders that the problems would be resolved; she said that they were working closely with i2 to solve the problems by creating “some technical and operational workarounds” and that the supply chain software was now stable.
While Nike was positive about the implementation process moving forward, they placed full blame on the SCM software and i2 Technologies.
Nike stopped using i2’s demand-planning software for short-and-medium range sneaker planning; however, it still used the application for short range and its emerging apparel business. By the Spring of 2001, Nike integrated i2 into its more extensive SAP ERP system, focusing more on orders and invoices rather than predictive modeling.
What Went Wrong?
While the failures damaged each company’s reputation in the IT industry, both companies would go on to recover from the poorly executed software implementation. Each side has assigned blame outward, but after reviewing all the events, it's safe to say each had a role in the breakdown of the supply chain management system.
Underestimating Complexity
Implementing software at this scale always has risks. Tom Harwick, Gigi Information Group’s research director for supply chain management, said, “Implementing a supply-chain management solution is like crossing a street, high risk if you don't look both ways, but if you do it right, low risk.”
One of Nike's most significant mistakes was underestimating the complexity of implementing software at such a large scale. According to Roland Wolfram, Nike’s operators had a false sense of security regarding the i2 installation because it was small compared to the larger NSC project. "This felt like something we could do a little easier since it wasn’t changing everything else [in the business]," he says. "But it turned out it was very complicated."
Part of the reason why the project was so complicated was because of Nike’s fractured legacy supply chain system and disoriented data sets. i2’s software wasn’t designed for the footwear and apparel industry, let alone Nike’s unique position in the market.
Data Quality
Execution by both parties was also to blame. i2 Technologies is on record recommending customization not to exceed 10-15%. Nike and i2 should have recognized early on that this range would be impossible to accommodate the existing SCM system.
Choosing a Big Bang implementation strategy didn’t make sense in this scenario. Nike’s legacy system data was too disorganized to be integrated into the i2 without making dramatic changes before a full-on launch.
Poor Communication
Communication between Nike and i2 from 1999 to the summer of 2000 was poor. i2 claimed not to be aware of problems until Knight issued blame publicly. Greg Brady, the President of i2 Technologies who was directly involved with the project, reacted to the finger-pointing by saying, "If our deployment was creating a business problem for them, why were we never informed?" Brady also claimed, "There is no way that software is responsible for Nike's earnings problem." i2 blamed Nike’s failure to follow the customization limitations, which was caused by the link to Nike’s bake-end.
Rush to Market
At the time, Nike was on the verge of solidifying its position as the leader in footwear and sports apparel for decades to come. Building a solid supply chain that could adapt to market trends and reduce the manufacturing cycle was the last step toward complete market dominance. In addition, the existing supply chain solutions built for the footwear and apparel industry weren’t ready to deploy on a large scale. This gave Nike the opportunity to develop its own SCM system putting the company years ahead of competitors. Implementing functional demand-planning software would be highly valuable for Nike and its retail clients.
i2 also was experiencing market pressure to deploy a major project. Had the implementation gone smoothly, i2 would have a massive competitive advantage. The desire to please Nike likely played a factor in i2’s missteps. Failing to provide clear expectations and communication throughout the process may not have happened with a less prominent client.
Failure to Train
After the problems became apparent in the summer of 2000, Nike had to hire consultants to create workarounds to make the SCM system operational. This clearly indicates that Nike’s internal team wasn’t trained adequately to handle the complexity of the new ERP software.
Nike’s CIO at the time reflected on the situation. "Could we have taken more time with the rollout?" he asked. "Probably. Could we have done a better job with software quality? Sure. Could the planners have been better prepared to use the system before it went live? You can never train enough."
How Nike Could Have Done Things Differently
While Nike and i2 attempted to implement software that had never been successfully deployed in the global footwear and apparel industry, many problems could have been avoided. We can learn from the mistakes and how Nike overcame their challenges with i2 to build a functioning ERP system.
Understanding and Managing Complexity
Nike’s failure to assess the complexity of the problem is at the root of the situation. Regardless if the i2 implementation was just the beginning of a larger project, it featured a significant transition from the legacy system. Nike’s leadership should have realized the scale of the project and the importance of starting NSC off on the right foot.
i2 also is to blame for not providing its client with realistic expectations. As a software vendor, i2 is responsible for providing its client with clear limitations and the potential risks of failing to deploy successfully.
See " Understanding and Managing Your Project’s Complexity " for more insights on this topic.
Collaborate with i2 Technologies
Both companies should have realized that Nike required more than 10-15% customization. Working together during the implementation process could have prevented the ordering issues that were the reason for the lost revenue.
Collaboration before deployment and at the early stages of implementation is critical when integrating a new system with fractured data. Nike and i2 should have coordinated throughout the process to ensure a smooth rollout; instead, both parties executed poor project management resulting in significant financial and reputational blows.
See " Solving Your Between Problems " for more insights on this topic.
Hire a 3rd Party Integration Company
Nike’s lack of understanding of the complexity of SCM implementation is difficult to understand. If i2 had been truthful in that they did not know about problems with their software, Nike could have made a coordinated decision not to involve the software company during the process.
Assuming that is the case, Nike should have hired a 3rd party to help with the integration process. Unfortunately, Nike’s internal team was not ready for the project. Outside integrators could have prevented the problems before the damage was done.
Not seeking outside help may be the most significant aspect of Nike’s failure to implement a new SCM system.
See " Be a Responsible Buyer of Technology " for more insights on this topic.
Deploy in Stages
A “Big Bang” implementation strategy was a massive mistake by Nike. While i2 should have made it clear this was not the logical path considering the capabilities of their software and Nike’s legacy system, this was Nike’s decision.
Ego, rush to market, or failure to understand the complexities of the project could all have been a factor in the decision. Lee Geishecker, a Gartner analyst, stated that Nike chose to go live a little over a year after starting the project, while projects of this scale should take two years before deployment. In addition, the system should be rolled out in stages, not all at once.
Brent Thrill, an analyst at Credit Suisse First Boston, is on record saying he would have kept the old system running for three years while testing i2’s software. In another analysis, Larry Lapide commented on the i2 project by saying, "Whenever you put software in, you don't go big bang, and you don't go into production right away. Usually, you get these bugs worked out . . . before it goes live across the whole business."
At the time, Nike’s planners weren’t prepared for the project. While we will never know what would have happened if the team had been adequately trained, proper preparation would have put Nike in a much better position to handle the glitches and required customizations.
See " User Enablement is Critical for Project Success " for more insights on this topic.
Practice Patience in Software Implementation
At the time, a software glitch causing a ripple effect that would impact the entire supply chain was a novel idea. Nike likely made their decisions to risk the “Big Bang” strategy, deploy in a year without phases and proper testing, and not seek outside help because they assumed the repercussions of a glitch wouldn’t be as catastrophic.
Impatience resulted in avoidable errors. A more conservative implementation strategy with adequate testing would have likely caught the mistakes.
See " Going Live Too Early Can Be Worse as Going Late " for more insights on this topic.
Closing Thoughts
One of the most incredible aspects of Nike’s implementation failure is how quickly the company bounced back. While Nike undoubtedly made numerous mistakes during the process, NSC was 80% operational in 2004.
Nike turned the project around by making adjustments and learning patience. Few companies can suffer a $100 million “speed bump” without filing bankruptcy, but Nike is in that position because of its resilience. The SAP installation wasn’t rushed and resumed many aspects of its original strategy. In addition, a training culture was established due to the i2 failures. Customer service representatives receive 140 to 180 hours of training from highly skilled “super users,” All employees are locked out of the system until they complete their required training courses.
Aside from the $100 million loss, the NSC project was successful. Lead times were reduced from nine months to six (the initial goal), and Nike’s factory inventory levels were reduced from a month to a week in some cases. Implementing a new SCM system also created an integration between departments, better visibility of customer orders, and increased gross margins.
While Nike could have executed far more efficiently, Phil Knight’s early assessment of the i2 failure turned out to be true. In the long run, the process gave Nike a competitive advantage and was instrumental in building an effective SCM system.
In a nutshell: A failure to demonstrate patience, seek outside help, and rush software implementation can have drastic consequences.
> Nike says i2 hurt its profits
> I2 Technologies, Inc.
> How Not to Spend $400 Million
> i2-Nike fallout a cautionary tale
> Nike rebounds: How Nike recovered from its supply chain disaster
> Scm and Erp Software Implementation at Nike – from Failure to Success
> I2 Says: "You Too, Nike"
Nike's LeBron sneakers a case study in guerrilla marketing
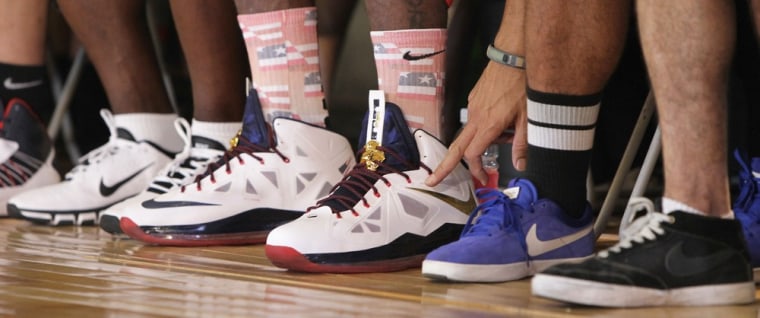
Nike kicked up a media storm last month with news that its new LeBron X+ shoe would be the company's priciest sneakers yet, at an astonishing $315 a pair.
The story, first reported by The Wall Street Journal , spread rapidly on news websites and cable television, gaining added momentum when the National Urban League took to the airwaves to chastise Nike for what officials called an “empty status symbol."
What received far less notice: Nike's quiet statement, emailed to some reporters more than 12 hours after the story broke, stating the reported price was inaccurate -- by as much as $135.
It was a classic case of Nike having its cake while eating it too, appearing to manage the news cycle so deftly that one expert told Advertising Age the marketing giant "won't do any advertising for this shoe. They don't need to."
The origin of the story of the $315 shoes is unclear. The Wall Street Journal story mentioned no source for the $315 figure, and if members of Nike’s vast marketing team were involved in development of the story, they left no fingerprints.
In the initial hours after the story was published and made its rounds, Nike officials steadfastly refused to comment on the story, saying they would not confirm the sneaker price, but not denying it either.
Suspicion immediately landed on a network of “sneakerhead” bloggers, enthusiasts who closely follow news of new shoe styles and don’t necessarily follow traditional journalistic protocols. Some product bloggers, for example, have been known to accept money or free products in exchange for favorable commentary, a practice that has attracted the attention of the Federal Trade Commission, which regulates advertising.
Late in the day the story broke -- well after 9 p.m. ET -- Nike emailed a brief statement to NBC News after declining to comment for hours.
“The reported price of the new LEBRON X is inaccurate,” said the statement sent by spokesman Brian Strong. “The LEBRON X will be launched in the Fall at a suggested retail price (SRP) of $180.”
A separate version with “Nike+ technology embedded in the shoes” would be marketed for a higher, as-yet undetermined price, the statement continued, adding helpfully: “Nike continues to offer shoes at various price points for consumers. …”
“Yeah we saw that statement, too. We then thought it was all just part of their strategy,” said Dan Lobring, head of public relations at Chicago-based rEvolution, a sports marketing and media services agency. NBC News had earlier that day asked rEvolution to comment on what appeared to be a record-priced, new shoe line.
“What do I think now?" Lobring asked. "I think they killed it on LeBron."
The story of the $315 shoes might not raise eyebrows except that Nike has a long history of successful guerrilla marketing – taking advantage of unconventional channels to reach its core customers, who might be hard to reach through traditional media.
Nike, in fact, is credited with inventing the concept of guerrilla marketing at the 1996 European Soccer Championships. For that tournament held in London, British sport-clothier Umbro bought the rights to be the official sportswear supplier. Nike, however, gobbled up all the outdoor advertising facades and poster frames near Wembley Park, the venue of the tournament, effectively shutting out the official sponsor.
“No one can control what Nike is leveraging so well -- exploiting the social media channels of the world,” said Raymond Bednar, president of Hyperion Marketing Returns in New York. “They let the free media ‘buzz’ wing their message to the masses at a fraction of the traditional spenders -- who stand in horror and disbelief that they in effect so overpaid for the asset.”
At the London Olympics, Nike freshened the script. While not an official Olympic sponsor, the Beaverton, Ore.-based company outflanked its archrival Adidas (which reportedly paid $155 million to sponsor the Games) by outfitting more than 400 athletes in its neon-yellow Volt shoes.
Nike’s Strong said the color of those kicks was scientifically selected because the human eye is most sensitive to the yellow-green mix, and our vision has a low sensitivity to red, the color of the London track. The shoes became one of the Olympics' true conversation pieces as some 41 athletes medaled while wearing the Volts.
Meanwhile, Nike's Olympic-esque TV ads, including one spot featuring everyday athletes competing in other Londons around the world, danced dangerously close to an International Olympic Committee charter that bars non-sponsors from running Olympic-specific ads. London Games organizers mulled legal action against Nike but ditched the plan, according to The Associated Press. Legal action likely would have played into Nike’s hands, one of the advantages of guerrilla marketing.
Nike has, however, been forced to apologize for some of its more provocative moves. Last March, around St. Patrick's Day, the company unveiled its new SB "Black and Tan" sneakers -- nicknamed so by consumers who noticed the shoes' resemblance to a favorite Irish beer drink in which stout and ale are combined to form black and brown layers.
Nike formally calls the shoe "the SB Dunk Low" and said it never intended the other colorful moniker to take over as it did. Nike executives made that clear after learning that the term "Black and Tan" is offensive to some Irish people because it was the name of a ruthless British paramilitary unit dispatched 90 years ago to crush Irish revolutionaries. Said Nike's Strong after the company learned of the misstep: "No offense was intended."
In another possible misstep, Nike sold women's shirts at the 2012 Games that carried the glittering words "GOLD DIGGING" to celebrate the achievements of American women who snared 29 of Team USA's 46 gold medals in London. When some women called the shirts sexist, Nike responded: "The T-shirt uses a phrase in an ironic way that is relevant given it was released just as the world focused on the success of female athletes."
Whether committing honest social blunders or creating calculated controversies, Nike seems to grab more attention to its products with each incident.
Better yet for Nike: The attention usually comes free of charge.
Nike’s success at cutting through the clutter with its unconventional marketing has to raise questions for its more conventional rivals, experts say.
"The core of the question is: What exactly is the value of paying (for) a property like the IOC or the USOC for category sponsorship rights? What do you really get? And based upon what you get, what should you really pay?" asked Bednar, of Hyperion Marketing Returns.
The value of a sports brand -- or of an Olympic sponsorship -- is essentially arbitrary, he said.
"Thus, most sponsors fall back to the comfort of ‘Well, that's what X paid, and they are a huge multinational company, so it must be right.’ All you have to do is lure one stupid -- and I don't use that the term 'stupid' lightly here; I just don't have a more accurate adjective -- major corporation into the paying game, and the rest will follow like the lemmings over the cliff," Bednar said.
“Insanity. Nike is brilliant in avoiding this scam."
Your Cookie Settings
Nike asks you to accept cookies for performance, social media and advertising purposes. Social media and advertising cookies of third parties are used to offer you social media functionalities and personalised ads. To get more information or amend your preferences, click the ‘More Information’ button or visit 'Cookie Settings' at the bottom of the website. To get more information about these cookies and the processing of your personal data, check our Privacy & Cookie Policy . Do you accept these cookies and the processing of personal data involved?
These cookies are required for basic site functionality and are therefore always enabled. These include cookies that allow you to be remembered as you explore the site within a single session or, if you request, from session to session. They help to make the bag and checkout process possible as well as assisting in security issues and conforming to regulations.
These cookies allow us to improve the site’s functionality by tracking usage on the website. In some cases these cookies can improve the speed with which we can process your request as they allow us to remember site preferences that you’ve selected. De-selecting these cookies may result in poorly tailored recommendations and slow site performance.
Social media cookies offer the possibility for you to connect to your social networks and share content from our website through social media. Advertising cookies (from third parties) collect information to help better tailor advertising to your interests, both within and beyond Nike websites. In some cases, these cookies involve the processing of your personal data. For more information about this processing of personal data, check our Privacy & Cookie Policy . De-selecting these cookies may result in you seeing advertising that is not as relevant to you, not being able to link effectively to Facebook, Twitter or other social networks, and/or not being allowed to share content on social media.
- Order Status
- Dispatch and Delivery
- Privacy Policy
- Terms of Sale
- Terms of Use
- Send Us Feedback
Popular Search Terms
Air Force 1
Top Suggestions
Nike Style By
NIKE CORTEZ
An unmistakable icon back with new colours and materials.
Latest & Greatest
Mother's day gifts, haaland x air max dn, racing gear, fitness gear, shop our icons, shop by sport, explore more, nike membership.
Member Product
Your Exclusive Access
Member Rewards
How We Say Thank You
Nike By You
Your Customisation Service
Be at your best, more of membership.
- Winter Trainers
- GORE-TEX trainers
- Walking Trainers
- White Air Max 90s
- Weightlifting Shoes
- Sandals & Slides
- Black Running Shoes
- White Running Shoes
- Trail Running Shoes
- Running Shoes Sale
- All Clothing
- Yoga Trousers
- Tech Fleece Joggers
- Tech Fleece Pants
- Tech Fleece Hoodie
- Football Tracksuits
- Tech Fleece
- Kids' Sliders
- Kids' Tracksuit Sale
- Kids' Puffer Jacket
- Football Club Teams
- Nike Run Club
- Nike Training Club
- Factory Store
- Black Trainers
- White Football Boots
- Blue Football Boots
- Gifts for Kids
- Football Gifts

IMAGES
VIDEO
COMMENTS
Abstract. Nike has gone 35% digital and is planning to reach 50% by 2025. It has shown immense growth and is expected to close year 2022 with over 50-billion-dollar revenue. Strategically Nike is ...
The firm started its operations by importing running shoes from Japan before becoming the world's largest sportswear company in 1980 (Statista 2018). ... Nike's case study is dedicated to ...
Closely after, in 2016, Nike also launched a self-lacing, everyday lifestyle shoe: the Nike HyperAdapt 1.0. These shoes were priced at US$720, the highest retail price for generally released Nike footwear ever. 4 Three years later, in January 2019, Nike unveiled the first high-performance sports footwear featuring self-lacing technology, the Nike Adapt BB, for professional basketball players ...
The American sportswear giant's success is rooted in a radical direct-to-consumer strategy built around content, community and customisation, and conceived for a post-internet world where brand connections are everything. Loading... In October 2020, in the middle of a global pandemic that had infected 188 countries, causing record sales ...
You can order this case online at http:www.wristore.com, or by call-ing 1-800-537-5487. For further in-formation or reprint permission, write Permission Department, 10 G Street, NE Suite 800, Washington D.C. 20002, fax (202) 729-7707, or email [email protected]. This case is printed on 100% un-bleached recycled paper.
Monday, October 29, 2018. 2. I. Introduction. The case study of Nike, Inc is critical to understand the serious and major transformation. a corporation underwent to sustainability and a circular ...
an analysis of both successes and missteps throughout Nike's history. We begin this case study by providing an overview of important events in Nike's historical trajectory, and of the athletic wear industry in the United ... The first Nike shoes were sold in 1971 and distributed by four Blue Ribbon Sports specialty shoe outlets in Portland ...
A case study in how innovative design can connect generations, empower communities, and help make sport more inclusive. Innovation. ... Rescue Mission: How Reverse Logistics Can Save Millions of Shoes. Nike's refurbishment program gives new life to once-discarded sneakers. Innovation. Special Delivery: How One Box Cuts Packaging in Half ...
The case is set in January 2020 and the case protagonist is John Donahoe, Nike's new CEO. Nike is the largest company worldwide in the athletic footwear, apparel, and equipment business. The case focuses on the challenges Donahoe faces as he attempts to drive Nike to the goal of $50 billion in annual revenues by 2021. The case focuses on Nike's competition, the convergence of technology with ...
Street Journal, Nike's flagship digital revenue increased 84% at the end of the 2022 fiscal year's second quarter. This increase in sales gains and profits was due to " strong sales from ...
Case Study: Analyzing Nike's Sneaky Transition From Sportswear to Lifestyle Brand. ... For example, if we put another company in Nike's shoes (no pun intended) and examined it under the same microscope, it wouldn't result in the same outcome. Since it's Nike, many people have just gone with the flow without questioning why the Apple ...
Nike Just do it: a hymn to daily challenges. More than forty years have passed since the first shoes with the famous mustache appeared on the market, but Nike's success does not stop. The Oregon company continues to lead its competitors with annual sales of close to $30 billion and growth of 10% over the past five years.
Sustainability and Innovation Case Study Nike Flyknit The Challenge Reaching over $30 billion in revenues for FY15, Nike, Inc. is the world's largest supplier of athletic footwear and apparel.1 Since its founding, Nike's business model has focused on innovation and pushing the boundaries of design and performance.
The first Nike House of Innovation 001 opened in Shanghai, followed promptly by the New York flagship 000, and with a third on its way in Paris. Across each location, Nike presents cross-category ...
A few leading companies like Nike are involving customers in the value creation process by offering Internet sites where they can share their interactions and experiences. These range from customers' ideas about how to improve or customize products to their feelings when they use products.). For Nike, the learning from these interactions ...
Nike is the leading brand of athletics shoes, apparel, sports equipment, and sports-related services. It has a market share of $39.1 billion making it the largest sports brand in the world. ... With this, our case study on Nike's business model has come to an end. So let's conclude this case study.
Nike was founded by Phil Knight and Bill Bowerman in 1964 as Blue Ribbon Sports (MarketLine, 2016; Strasser & Becklund, 1993).The company, which was renamed Nike in 1971 (MarketLine, 2016), has evolved to become the world's largest athletic brand offering innovative athletic apparel and footwear, and related sportswear and technology.The sportswear giant has been listed among the Fortune 500 ...
Through a case study of Nike, Inc. - a company that has come to symbolize both the. benefits and the risks inherent in globalization - this paper examines the various. difficulties and complexities companies face as they seek to balance both company. performance and good corporate citizenship in today's global world.
Nike's U.S. customer service representatives received 140 to 180 hours of training from highly trained fellow Nike "super users," says Andy Russell, Nike's global transition director.
Abstract. This research has focused on Nike and its strategies that are helping the organization to influence buying behavior of its consumers. For this purpose, this research has collected data from two credible websites. After collecting data from these two websites, it was found that Nike's activities to influence buying behavior of its ...
The announcement would then send Nike's stock down 19.8%. In addition, Dallas-based supply-chain vendor i2 Technologies, which Nike assigned blame, would suffer a 22.4% drop in stock price. The relationship would ultimately cost Nike an estimated $100 million.
Nike's LeBron sneakers a case study in guerrilla marketing. Sept. 6, 2012, 11:27 AM UTC. By Bill Briggs and Bill Briggs. Lebron James wore a pair of Nike's Lebron X shoes, center, to a event in ...
Nike has been accused of using child labor in the production of its soccer balls in Pakistan. This case study will examine the claims and describe the industry and its impact on laborers and their working conditions. While Pakistan has laws against child labor and slavery, the government has taken very little action to combat it. Only a boycott by the United States and other nations will have ...
Inspiring the world's athletes, Nike delivers innovative products, experiences and services.